Water Treatment Technologies to Reduce Chemical Use
Water treatment is a set of processes used to make water suitable for industrial use or consumption. Since raw water typically contains various impurities ranging from chemicals to biological material, achieving the proper level of water quality has traditionally meant a complex, multi-step process that requires lots of hazardous chemical inputs.
Increasingly, newer separation technologies are helping to minimize the use of chemicals in water treatment for a safer and more efficient process. Here we’ll look at examples of chemicals used in conventional water treatment, what purposes they serve, and how technologies like membrane separation and ion exchange can reduce reliance on chemicals.
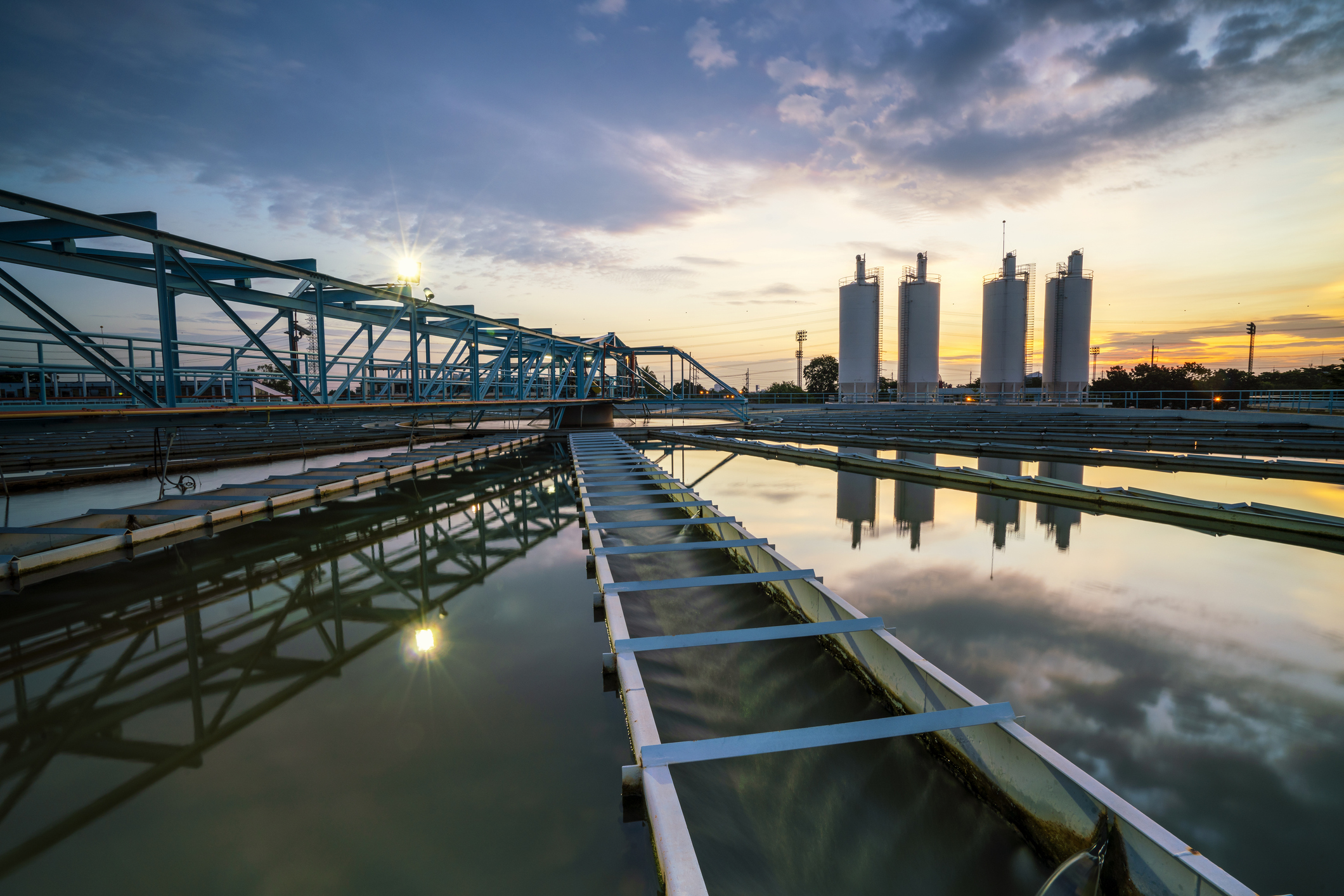
How are chemicals used in conventional water treatment?
A conventional water treatment train consists of several steps, including coagulation, flocculation, sedimentation, filtration, and disinfection. Below, we’ve outlined the common types of chemicals used for conventional water treatment, and what purposes they serve:
- Coagulants work by neutralizing the charges of suspended particles so that they clump together for easier removal via settling and/or filtration. The most common coagulant chemicals are inorganic iron or aluminum compounds such as aluminum sulfate or ferric sulfate. Organic coagulants are also available, but they tend to be more expensive, and are generally used for special circumstances, such as situations where a facility wants to avoid adding metals, or to treat streams that contain chlorine.
- Flocculants encourage coagulated particles to clump into even larger particles known as flocs. This process uses organic polymers like acrylamide, and are sometimes applied at the same time as coagulants.
- Reducers are used to break down substances like ozone, hydrogen peroxide, and chlorine to prevent membrane degradation, as well as to remove oxygen from boiler feedwater. Examples of common chemicals used for this purpose include sodium bisulfite, sodium hydrosulfite, ferrous sulfate.
- Oxidizers are used for disinfection, preventing bio-fouling in heat exchangers, breaking down organic compounds into simpler substances that can be separated out, and oxidizing metals into an insoluble form to be removed by precipitation and/or filtration. Examples of oxidizing agents include sodium hypochlorite, ozone, chlorine dioxide, and permanganate.
- Sludge conditioners are used to help optimize the performance of filter presses or other equipment used to remove excess liquid and reduce the volume of sludge before disposal. Common chemicals used for sludge conditioning include ferric chloride, lime, sulfuric acid, alum, ferrous sulfate, or organic polymers.
- Degreasers and cleaners are used to break down grease or oil to make it easier to separate them out of the stream. Typically sold as commercial products, cleaning and degreasing agents often have proprietary formulations, with ingredient lists that may include organic solvents, enzymes, fatty acids, sodium hydroxide, potassium hydroxide, phosphates, or a variety of other chemicals.
- Biocides and disinfectants are used to kill off or otherwise inactivate pathogens that may be present in the water. The most common disinfectants used in water treatment are chlorine-based chemicals such as sodium hypochlorite or chloramine, although other options include bromine compounds, hydrogen peroxide, and non-oxidizing biocides for special applications.
- Precipitants are used to remove soluble metal ions and phosphates by reacting with the dissolved substances to form a solid that can then be removed through filtration or other means. The specific chemicals used will depend upon what dissolved materials are being targeted for removal, however common precipitants include lime, soda ash, potassium permanganate, and chlorine.
- Odor control chemicals like ozone, hydrogen peroxide, or chlorine dioxide may be applied to the stream itself to prevent unpleasant odors. Alternatively, other methods like air scrubbing, biofiltration, or activated carbon filtration can be used to contain odors released into the air.
- Antifoam and defoamer products are used to prevent overflows and related safety issues by inhibiting foam. Defoaming chemicals are typically formulated from silicone, mineral oil, alcohol, or surfactants, and the type used will depend on what constituents are present in the stream, as well as process conditions.
- Acids and bases are used to adjust the pH of a stream to bring it within a range suitable for treatment, reuse, or disposal. Acids such as sulfuric acid, hydrochloric acid, sodium hydroxide, nitric acid and phosphoric acid are commonly used to lower the pH of an alkaline stream, while bases such as calcium hydroxide (lime) or ammonium hydroxide are commonly used to increase the pH of an acid stream.
- Anti-scalants are used to prevent mineral scaling in water distribution networks, heat exchange surfaces and membranes. Common anti-scalants used are phosphates, phosphonates, polyacrylates, and other polymers.
In essence, conventional treatment relies on chemical reactions to alter contaminants, either to make them innocuous for the intended application, or easier to separate from the liquid stream using basic filtration equipment. Each chemical is effective for its given role in the water treatment process, but the number of chemicals needed can quickly add up, especially for facilities dealing with complex raw water or wastewater streams with lots of different contaminants. Many of these chemicals present health and safety hazards, so they require special handling or storage and need to be chosen carefully to avoid dangerous interactions with stream constituents and/or other chemicals used for treatment. Many organizations have also begun to look at how chemical applications affect their environmental footprint due to increasing regulations and a desire to minimize chemical discharges. In short, conventional chemical treatment can be an affordable solution, but not necessarily a convenient, efficient, or environmentally sound one.
Strategies to reduce chemical use in water treatment
Given some of the disadvantages that come along with chemical treatment, it’s no wonder that more and more facilities are looking for water treatment solutions that are simpler, safer, and more cost-effective. Researchers have even coined the term “minus approach” to refer to water treatment methods that seek to remove constituents without adding chemicals. Fortunately, there are proven water treatment technologies like membrane filtration, ion exchange (IX), electrocoagulation, and adsorption that use less chemicals while still offering excellent separation and water treatment performance.
Membrane filtration
Whereas conventional treatment relies on chemical reactions, membrane filtration works by physically removing contaminants from a liquid stream. To do so, a membrane filtration system uses pressure to force the stream through a semipermeable barrier known as a membrane. Tiny pores in membrane keep out any particles too large to fit, while allowing the stream to flow through. For this reason, membrane filtration systems are classified into four basic types depending upon their respective pore size ranges:
- Microfiltration (MF) offers the coarsest filtration of all membrane separation types. With pore sizes ranging from 0.1 to 10 μm, MF is suitable for removal of contaminants such as algae, bacteria, protozoa, sand, clay, and metal particles.
- Ultrafiltration (UF) systems offer pore sizes ranging from 0.001 to .01 μm, making UF suitable for removal of very fine particles, including plastics, proteins, silica, silt, viruses, and endotoxins.
- Nanofiltration (NF) systems offer pore sizes ranging from 0.002 to 0.005 μm, making NF suitable for larger organic molecules, pesticides, and divalent ions such as calcium or magnesium.
- Reverse osmosis (RO) offers the finest pores of any membrane filtration type, at only 0.0001 μm in For this reason, RO removes all contaminant ions or particles larger than water molecules, yielding a filtrate of extremely high purity.
Chemical use for membrane filtration systems is typically constrained to periodic cleaning with acid or alkaline solutions to remove scale or other deposits on membranes. In some cases, anti-scalants, dispersants, reducing agents, or biocides may also be used during treatment to prevent membrane fouling, especially for RO. All in all, though, membrane filtration offers excellent separation while greatly reducing chemical use compared to conventional water treatment.
Gas transfer membranes
Related to membrane filtration, gas transfer membranes (GTMs) are a special type of separation used to remove and/or change the composition of dissolved gases in a liquid stream. They can be used between the first and second pass of a double-pass reverse osmosis system to remove carbon dioxide and eliminate the need to handle and manage injection of caustic (sodium hydroxide). GTMs are also useful for removing oxygen from boiler feedwater streams, which can eliminate the need to feed sodium bisulfite or other oxygen scavengers to the system.
Ion exchange
In contrast to both membrane filtration and chemical treatment, ion exchange (IX) provides more targeted contaminant removal. This is because ion exchange leverages forces of electrochemical attraction to selectively remove ionic contaminants by swapping them out for substances with similar ionic charges. For this reason, IX is good for applications such as demineralization, reducing TDS, producing high purity water, removing alkalinity, removing or recovering metals, and selective contaminant removal. Compared to conventional chemical treatment, IX requires less steps and less chemicals to achieve these types of separation goals.
The IX process is driven by a special material called resin, which is essentially a matrix that holds functional groups that serve to attract ions of the opposing charge. With active use cycles, the resin becomes depleted and will need to be refreshed periodically by applying a chemical regenerant. This process—known as resin regeneration—accounts for nearly all chemical usage in IX. While this does technically mean that IX entails some chemical use, in most cases IX regenerants tend to be relatively safe and affordable acids, bases, or salt solutions.
Take, for example, sodium zeolite softening. This common and effective IX process is used to remove hardness from water in order to prevent scaling and other issues. A sodium zeolite softener works by swapping out scale-forming ions like calcium and magnesium with sodium ions that are loosely held by the resin. When the sodium ions are depleted, the resin is regenerated with a simple sodium chloride solution—the same cheap and readily available substance we know as table salt.
Adsorption
Adsorption is a physical separation process where contaminants are bound to a solid material based on forces of molecular attraction. While no chemicals are needed, the adsorption media will need to be replaced periodically, and disposed of properly as solid waste. Some of the more common adsorbents include activated charcoal, zeolite, silica gel, although new and proprietary adsorbent materials are being introduced all the time.
Electrocoagulation
Electrocoagulation (EC) is yet another water treatment technology that offers an alternative approach to chemical addition. Instead of chemical coagulants, EC uses an electrical current to destabilize surface charges of stream constituents, such as suspended solids, emulsified oils, metals, and hydrocarbons, causing them to clump together such that they can be removed by settling or filtration. While its use has been somewhat hampered by its operational complexity, EC is growing more popular due to its ability to produce high quality effluent, as well as its low chemical and energy use.
How can SAMCO help?
When it comes to water treatment, there’s often more than one way to achieve separation or purification goals—but that doesn’t mean that every solution is equal. At SAMCO, we have over 40 years’ of experience in building custom water treatment systems that are designed around our customers’ specific goals. Whether you are looking to use less chemicals, lower energy costs, cut water use, or meet some other objective, SAMCO can help you navigate available water treatment technologies like IX or RO, and make an informed choice.
For more information or to get in touch, contact us here to set up a consultation with an engineer or request a quote. We can walk you through the steps for developing the proper solution and realistic cost for your water treatment system needs. Or, if you would like to learn more about the topics discussed in this article, here are some blog posts that might interest you: