Chip Fab Wastewater Management: Recycling and reuse trends in the semiconductor industry
It’s hard to overstate just how much of our day-to-day life relies on semiconductor chips– those tiny, delicate components that are the brains of our electronic devices. Driven by unrelenting demand for electronics, the semiconductor industry is expected to see growth in the coming years. But with that opportunity comes a challenge, since semiconductor chip manufacturers—chip fabs, as they’re known—require a lot of water to operate. Here, we’ll look at how chip fabs can minimize water use and remain competitive in an age of water scarcity.
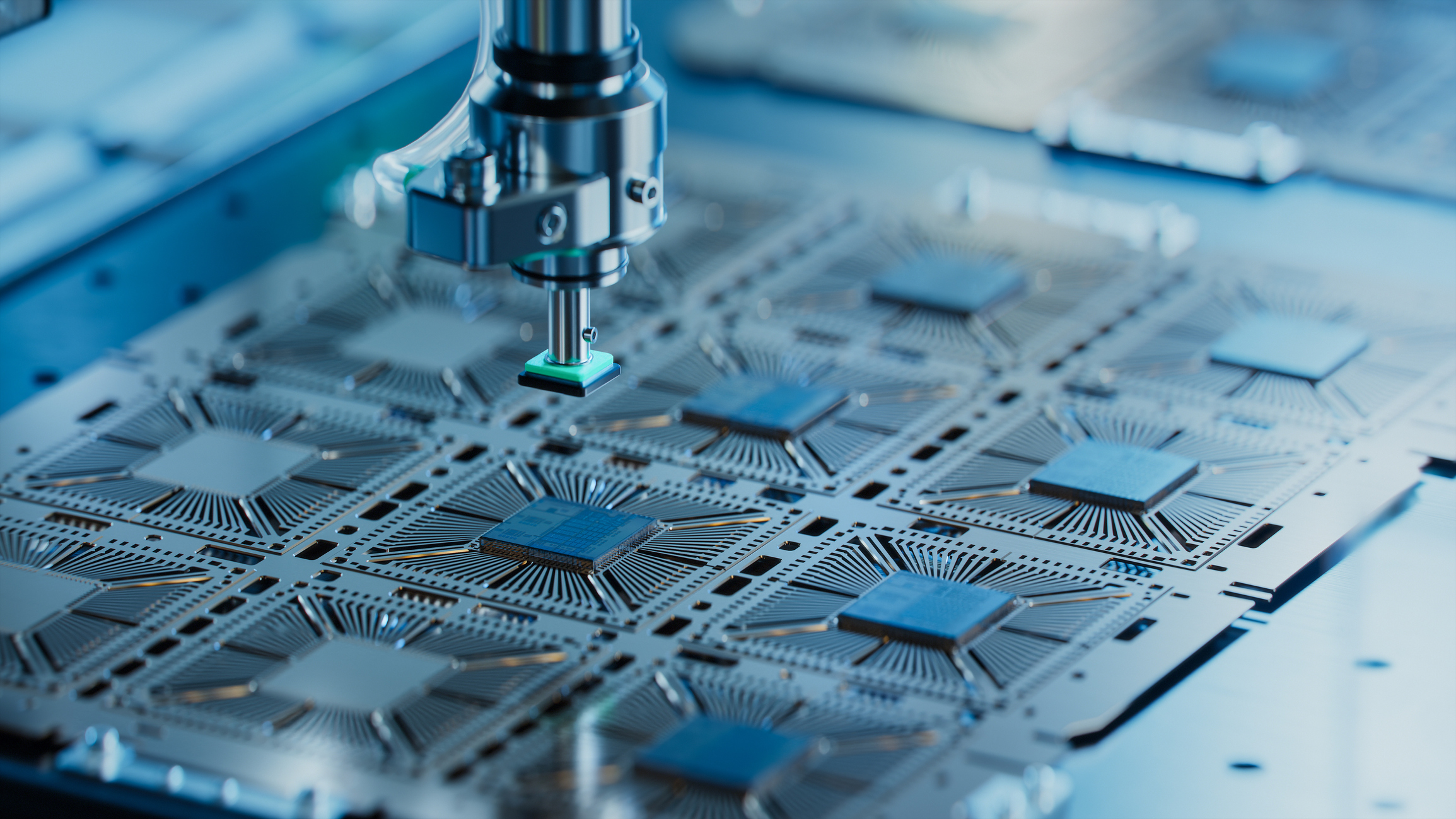
Why do chip fabs need so much water?
Failure rates are a top concern for chip fabs, who must avoid introducing contaminants at any point during a complex manufacturing process. For this reason, chip fabrication takes place in a clean room, which is an environment where dust, vibration, temperature, and humidity are carefully controlled. Additionally, the fab must ensure that process streams are also completely free of contaminants, which they achieve by using ultra-pure water (UPW). Because chip fabs use UPW for process solutions and repeated washing and rinsing steps, a single chip fab can use millions—or even tens of millions—of gallons of water per day. Part of the reason is that producing UPW requires facilities to draw in significantly more water than is needed for their process, since the low tolerance for contaminants means that a lot of water will be end up in a reject stream. And while UPW accounts for most of the water use in a fab, facilities also use lesser quality water for processes such as scrubbing to remove contaminants from vapor and gases, and for cooling of equipment and streams used in thermal processes.
Common water uses in semiconductor chip fabrication
So how exactly is water used in chip fabrication? Here, we’ll look at common water uses at each step of semiconductor chip production:
- Wafer manufacturing: Technically a precursor to chip fabrication, since a chip fab will usually purchase silicon wafers from a supplier. Wafer manufacturers start by producing ingots, which are high purity crystallized silicon formed in a cylindrical shape. Ingots are sliced into wafers less than a millimeter thick and polished to an extremely smooth surface. UPW may be used during each of these steps to wash away debris from cutting and polishing.
- Film deposition: Fabs begin by cleaning the wafer to remove any traces of debris from manufacturing, typically with UPW. The wafer is then oxidized to deposit a protective film of silicon dioxide on the outer surface. Some fabs use a wet oxidation process; in this case, the facility will require purified water vapor to carry out the oxidation reaction. Regardless of the process used, most fabs will use deionized (DI) water to wash away any particles remaining after oxidation.
- Photolithography: A light-sensitive chemical known as photoresist is applied to the wafer, and then a UV light is projected onto the wafer through masks that form circuitry patterns. If the fab uses immersion lithography, they will flood the wafer surface with DI water to eliminate air between the light source and the wafer. The exposed resist is degraded by the light, and can be dissolved with a developer solution, while the masked resist stays on the surface of the wafer to facilitate next steps. The wafer is then washed with solvents and/or UPW.
- Next, the fab will etch circuit patterns into the surface of the wafer. This is achieved either through a wet process in which a liquid etchant such as hydrofluoric or phosphoric acid is applied to the wafer; or through a dry process in which the wafer is exposed to reactive gases. The etchant dissolves areas of the silicon dioxide coating that are not covered by the photoresist, leaving circuit patterns of exposed pure silicon crystal. The wafer is then thoroughly cleaned and rinsed with UPW.
- Ion implantation. Silicon itself is not conductive, so the next steps entail adding ions to give the wafer its semiconductor properties. To do so, impurities like phosphorus, arsenic, boron, indium, aluminum, and gallium are deposited in thin films on the wafer surface and/or implanted at precise depths. These positive and negative charged ions create p-n junctions that ultimately control the flow of electrical current through the chip. Next, the fab will strip away the photoresist coating with a chemical or ashing process, and then thoroughly clean the wafer with UPW.
- At this phase, thin layers of conductive and non-conductive metals are applied to the wafer to interconnect areas of the chip to form circuits, act as barriers, and form contacts. This process is usually followed by application of a protective coating, followed by washing with UPW to remove any particles or contaminants.
- Testing and packaging. The fab will then perform quality testing called wafer probing to check current, voltage, resistance and other performance specs. Acceptable wafers are then cut in a process called dicing, resulting in individual chips known as “dies.” Chip dies are then washed with UPW to remove any particles from cutting, mounted in their outer packaging, and subjected to more quality testing.
Water conservation as a growing trend for semiconductor industry
The semiconductor industry is rapidly growing, thanks to strong demand for electronic devices. But current and future threats of water scarcity loom large as a challenge for the industry. Whether motivated by shortages, or by rising costs for sourcing and discharging water, or rising competition, most chip fabs have already implemented water recycling and reuse to some extent. Even so, fabs will need to continue to adopt and improve upon their water management strategies to cut down on the volumes of water that they take in to ensure long-term sustainability.
Wastewater treatment challenges
Chip fabrication is a multi-step process that involves many different chemical constituents, resulting in highly complex wastewater streams with a variety of different contaminants, including:
- Acids (e.g. hydrofluoric acid, phosphoric acid, sulfuric acid)
- Ammonia
- Boron
- Chelating agents (e.g. cyanide, PBTC)
- Chemical oxygen demand (COD)
- Heavy metals (e.g. copper, zinc, lead, nickel)
- Hydrogen peroxide and ozone
- Metallic particles (e.g. aluminum, gallium, indium, and molybdenum)
- Metal oxides
- Organic compounds (e.g. isopropyl alcohol)
- Silicon
- Suspended solids
Because of the range of constituents in chip fab wastewater, facilities typically need to combine multiple wastewater treatment technologies. This can include carbon, media, and/or membrane (MF/UF) filtration, as well as oxidation to degrade and remove organics or other hard-to-treat compounds. If the facility reuses all or some of its wastewater streams, as most do, they will also likely use reverse osmosis (RO) as well as ion exchange (IX) or deionization (DI) to bring the water up to ultra-pure water quality levels. While the benefits of treating wastewaters for reuse or responsible discharge are clear, cost and space constraints can still be barriers to adopting a more robust water management strategy.
Water conservation applications at chip fabs
Over the past decade, severe drought events have directly impacted major chip producers, including Intel and TSMC, both of whom have expanded their water management initiatives to help mitigate future threats of water shortage. Key water conservation strategies at chip fabs today include upgrading to more efficient water treatment technologies, adoption of water reuse/recycling programs, and switching to more water-efficient manufacturing techniques.
Water reuse approaches vary in scope and complexity, but some research estimates that chip fab facilities can achieve a recovery rate as high as 60% by simply re-routing spent process streams to be recycled for use in a different process with less exacting quality standards, such as cooling. While potentially more complex and costly, chip fabs can also greatly reduce the amount of water they draw in by treating and recirculating spent streams for UPW production.
The way in which semiconductor fabs adopt water reuse and recycling does differ a bit from other industries. While comprehensive, end-of-pipe wastewater treatment systems can work well for some industries, semiconductor fabs are usually better served by a more targeted approach. This is because all those steps of chip fabrication, like etching, rinsing, lithography, and die cutting, each contribute very different contaminants to a wastewater stream. When combined, a facility then must treat a large volume of highly complex wastewater. The more efficient approach is to segregate spent streams and treat them individually for recycling or reuse.
A side benefit of treating wastewater for reuse is that fabs can reclaim valuable resources while they’re at it. Depending on the processes at hand, chip fabs may be able to recover materials like silicon, fluoride, copper, and isopropyl alcohol, which could potentially be reused internally to cut costs associated with sourcing these materials. Additionally, chip fab water treatment can produce byproducts like ammonium sulfate (used in fertilizer) and calcium fluoride (used to produce cement), both of which can be sold for an additional revenue stream.
Another water conservation strategy that chip fabs can adopt is the replacement of wet processes with dry processes. There are both wet and dry methods for oxidation, etching, and resist stripping steps of fabrication. Wet processes are often cheaper, but dry processes offer benefits beyond reduced water use. Among these, dry processes tend to offer greater precision, an advantage that has contributed to their rising popularity as chips have gotten smaller.
How can SAMCO help?
- SAMCO has over 40 years of experience designing and manufacturing custom water treatment systems that optimize industrial water use. We have helped clients in the electronics and semiconductor industries meet important goals, like conserving water, cutting waste, and reclaiming valuable resources—and we can help you too. If you have questions about what water management solutions may be right for your facility, contact us to set up a consultation with an engineer. Our experts will help you understand the process for developing an optimal water treatment solution and determine a realistic budget for your project.
You can also click on over to our blog to learn more about water management and wastewater treatment issues impacting electronics manufacturers, chip fabs, and other industries. Relevant articles include:
- Industry Focus: Electronics Industry Trends and What They Mean For Your Water Management Strategy
- Water recycling and reuse systems: Strategies for a smaller carbon footprint
- How Much Do Reverse Osmosis and Nanofiltration Systems Cost?
- How Do You Remove Silica from Industrial Water and Wastewater?
- What to Do If You Have Cyanide in Your Industrial Wastewater
- Five Ways Your Industrial Facility Can Reduce Wastewater Discharge Volume