Why a Membrane Clean-In-Place (CIP) System?
Membrane separation technologies are a cost-effective and dependable solution for a wide variety of water purification and process liquid separation applications. But in order to operate as economically and reliably as expected, membrane separation systems demand a regular cleaning regimen that can be a burden when done manually. That’s where clean-in-place (CIP) systems come in. By streamlining and automating cleaning processes, CIP systems help to keep reverse osmosis (RO), nanofiltration (NF), ultrafiltration (UF), and microfiltration (MF) membranes in top operating condition.
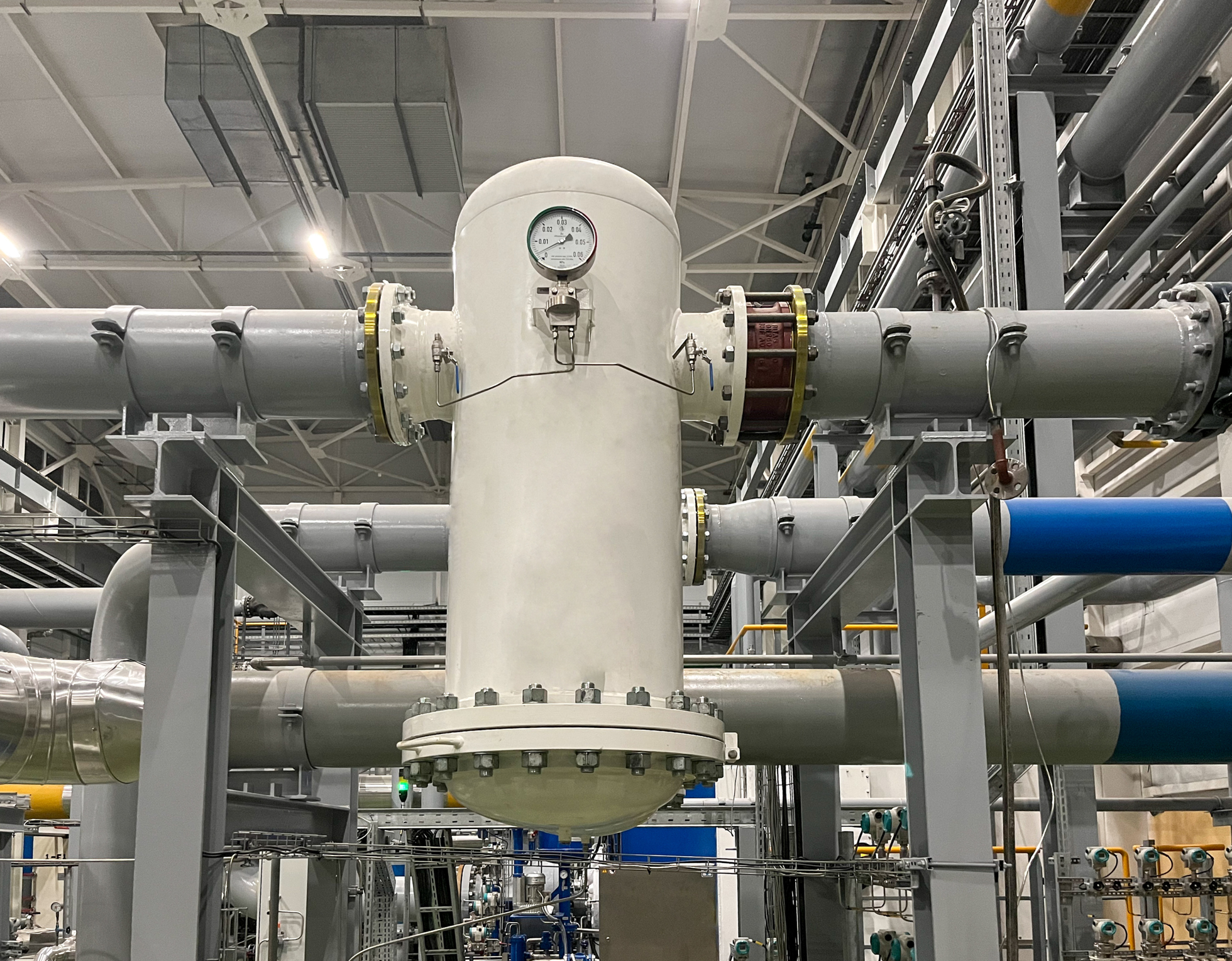
What are membrane CIP systems?
As a membrane separation system is used, foulants will tend to accumulate on the surface of the membrane element. Over time, these foulants can restrict the flow of liquids through the membrane, and lead to problems with inconsistent pressure, reduced permeate quality, and membrane fouling. Regular cleaning is essential for removing foulant buildup, but doing so manually requires disassembly of the equipment and removal of the membrane elements—which can be a time-consuming and labor-intensive task.
A membrane clean-in-place (CIP) system is a piece of equipment that cleans the active membrane surface of membrane modules without the need to disassemble the unit. To do so, a CIP system will pump cleaning solutions through the membrane system to remove any particles or residues that have accumulated during use. Most membrane CIP systems are automated and employ programmable logic controls (PLC) to manage cleaning and rinse cycles, allowing them to maintain controlled temperatures, flow rates, and cycle durations specific to the equipment and application at hand.
Overview of the membrane CIP process
The general CIP process consists of a series of cleaning and rinse cycles that are designed around the exact maintenance specifications of the membrane unit. Common steps in a membrane CIP process include:
- Pre-rinse: The membrane unit is flushed with clean water or permeate to remove excess process liquids or loose particulates present. The initial system flush also provides the opportunity to check that valves are properly oriented so that streams flow through the unit in the correct direction during later CIP cycles.
- High pH CIP: A caustic cleaning solution is pumped through the membrane unit to remove dissolved organic material, silica, and biological growth.
- Intermediate rinse: The membrane unit is flushed with clean water or permeate to remove residues that can interfere with other cleaning agents.
- Low pH CIP: An acid cleaning solution is circulated through the membrane unit to remove iron, salts, mineral deposits, and scale.
- Post-rinse: Following application of cleaning agents, the CIP process concludes with a final rinse and/or quality rinse to flush out remaining cleaning chemicals and ready the membrane unit to return to operating status. Post-rinse steps are complete when foaming subsides, or when the quality of effluent and retentate streams are roughly equivalent.
Exactly which of these steps are included and the order in which they are executed will differ from one system to the next, depending on factors such as the type of filtration (RO, NF, UF, or MF), the membrane element configuration (spiral wound, tubular, etc.), and what types of foulants are present.
Benefits of a membrane CIP system
The primary benefit of installing a membrane CIP system is to minimize labor and costs associated with cleaning activities. Without a CIP system, workers will need to disassemble the unit, remove the membrane modules, and reassemble the system once cleaning is complete. Some facilities elect to ship membranes to an offsite cleaning service, and may invest in additional sets of membrane elements that can be swapped in during cleaning cycles. For all these reasons, traditional cleaning methods can be costly, time-consuming, and vulnerable to human error. CIP systems streamline the cleaning process by allowing the membrane separation unit to remain intact, thereby reducing the amount of labor and downtime needed for each cleaning cycle and eliminating the need to purchase and store additional sets of membrane elements. As a result, membrane CIP systems can greatly reduce costs associated with routine cleaning.
CIP systems generate other benefits as well. For example, by preventing excess foulant buildup, membrane CIP systems help maintain lower operating pressures and more consistent permeate quality. Additionally, CIP systems ensure that cleaning is performed correctly and consistently, which can maximize the membrane separation system’s overall cost-effectiveness by extending membrane service life.
Optimizing your membrane CIP system
Membrane CIP systems need to be able to efficiently remove foulants from membrane surfaces without causing premature wear on the membrane itself. The best CIP system designs balance several variables, including the type and concentration of cleaning chemicals, temperature, pressure, and time, while staying within the operating limits of the membrane product. Below, we’ll look at some key considerations for optimizing a membrane CIP system design.
Determining a CIP schedule
There are typically two approaches to the timing of CIP cycles for a membrane system. For stable systems with consistent performance, system operators can perform a CIP on a consistent basis, such as on a semi-annual or quarterly schedule. The other approach is to conduct cleaning cycles as needed based on an observed degradation in system performance. When membrane function declines by a given amount, running a CIP cycle is an effective way to restore the membrane performance to the desired parameters.
For RO and NF systems, a CIP is generally warranted when any of the following occur:
- Normalized permeate flow rate declines by 10-15%;
- Normalized pressure differential (dP) increases by 15%;
- Normalized rejection rate decreases by 10%; and/or
- Salt passage rate increases by 5-10% (for RO systems).
For UF and MF systems, CIPs are typically done when any of the following occur:
- Permeability decreases significantly;
- Normalized trans-membrane pressure (TMP) increases significantly; and/or
- Operational TMP meets or exceeds the limit for the membrane product.
While these are common guidelines for membrane CIP systems, they won’t necessarily apply to all membrane systems. CIP schedules should always be devised in accordance with membrane manufacturer recommendations. Additionally, be sure to use normalized data when monitoring these metrics, since fluctuations in operating conditions can naturally affect membrane operations and result in misleading measurements. Normalized data provides a standardized measurement that is a more accurate indication of membrane performance.
Choosing CIP chemicals
There are a wide variety of cleaning chemicals used in CIP systems, each of which is chosen based on what residues or foulants are present, as well as the material composition of the membrane element. To get the best results, cleaning chemicals need to efficiently remove foulants without damaging the membrane material. CIP systems may use a combination of different cleaning chemicals, especially if membranes are exposed to a complex set of foulants. This may include acid detergents to remove mineral scale deposits, alkaline detergents to remove grease or organic residues, and/or disinfectants to neutralize any pathogens that may be present.
For any membrane CIP design element, is always best to use the mildest approach possible to achieve cleaning objectives. This principle applies not only to chemical selection, but to other parameters as well, such as using the minimum chemical contact time, maintaining a pH as close to neutral as possible, and avoiding extreme temperatures. In general, it is best to stay strategic in balancing these variables rather than resorting to harsher cleaning methods. Doing so will help to avoid degradation of membrane materials so they will need to be replaced less frequently. It is always a good idea to consult with membrane manufacturers as well as suppliers of specialty membrane cleaning chemicals for advice on selecting appropriate membrane cleaning chemicals for use in a specific application.
How can SAMCO help?
SAMCO has over 40 years’ experience in the design and delivery of complete membrane separation systems with CIP capabilities. Whether your needs include retrofitting existing equipment with a clean-in-place system, or adding new separation systems with built-in CIP technology, SAMCO can help you determine the cleaning procedure that best fits your membrane separation system. Additionally, SAMCO has a team of field service technicians that can assist in running your CIP process and provide training so your system operators can confidently perform CIP cycles on their own.
Contact our team of experienced professionals today to discuss your needs. We offer specific guidance and training on the best CIP procedures to ensure optimal performance for RO, NF, UF and MF systems.
To learn more about membrane filtration and other process separation technologies, click on over to our blog. There, you’ll find articles on a range of relevant topics, such as:
- Ultrafiltration: common industrial applications and uses
- What is Reverse Osmosis and How Is It Used For Industrial Applications?
- How to Choose a Membrane
- Water Treatment Technologies to Reduce Chemical Use
- Can a membrane bioreactor be right for your municipal wastewater treatment facility?