Industry Focus: Chemical industry trends and how they’re shaping water use in 2025
According to industry experts, a staggering 96% of all manufactured goods rely on products from the chemical sector.[i] The fact that chemical and petrochemical manufacturers touch nearly every corner of industrial production puts them in a unique position when it comes to forecasting the impacts of potential challenges and opportunities facing the industry.
In this article, we’ll – look at some trends in the chemical industry and explore how water management strategies may help manufacturers weather future challenges or take advantage of certain opportunities.
[i] Cybersecurity and Infrastructure Security Agency (CISA), “Chemical Sector Profile,” Mar. 23, 2022.
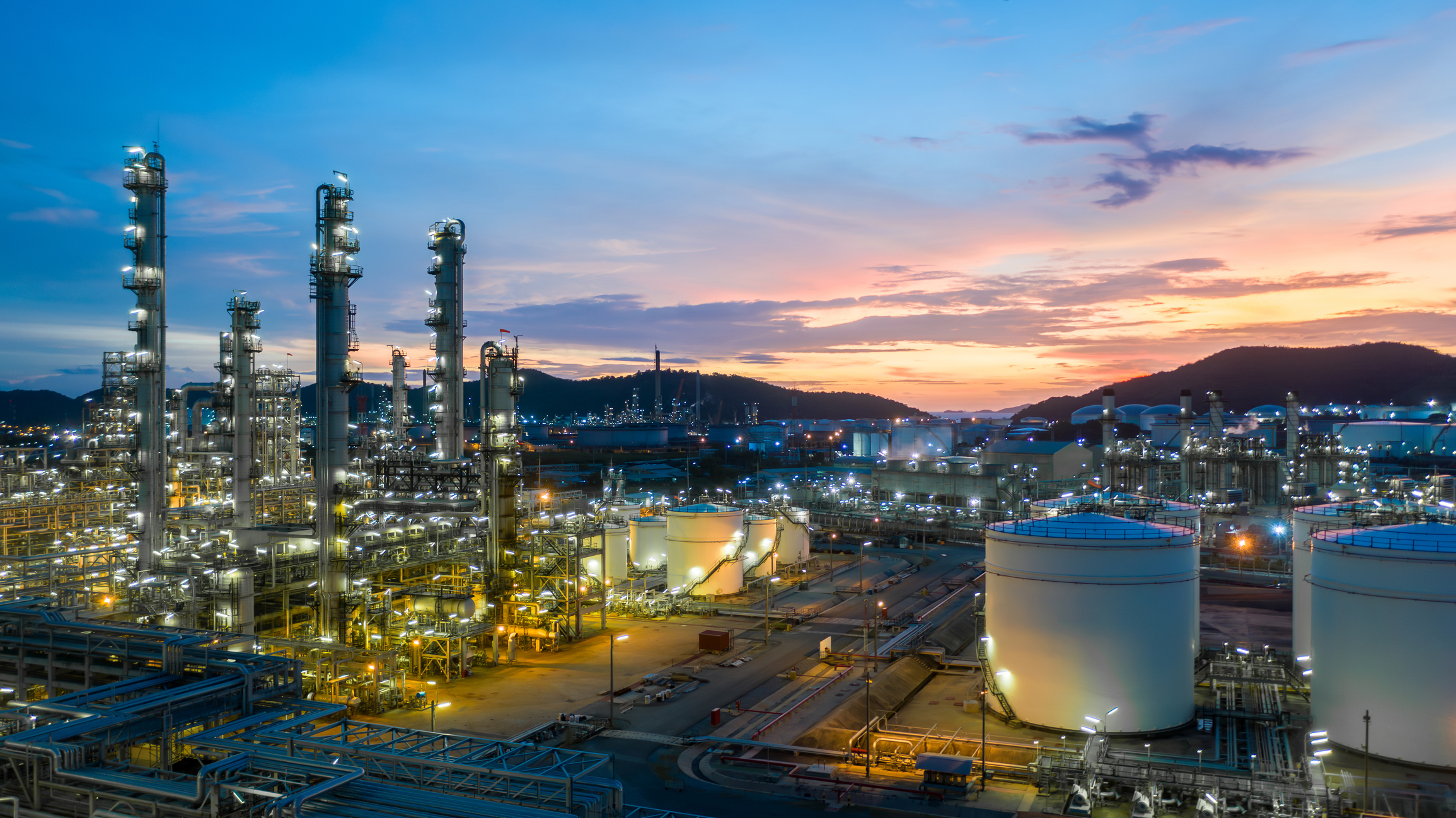
Key trends in the chemical & petrochemical industry
Volatile demand triggers cost-cutting measures
The chemical industry has had a lot of ups and downs in recent years. Back in 2020, it saw some abrupt changes in response to the COVID-19 pandemic, including major shifts in demand patterns for different chemical products. As the world began to recover from supply disruptions in 2021 and 2022, chemical manufacturers saw significant growth in production and revenue, a change that Deloitte analysts attribute in part to manufacturers stockpiling chemical inventory to avoid disruptions due to ongoing supply chain issues.[i] The pendulum swung the other way in 2023, with weak demand resulting from companies destocking their inventories.[ii] This volatility continued into 2024, as well, when demand for chemical products picked up in early 2024, only to fall off again during the latter half of the year, as reported by the American Chemistry Council (ACC).[iii]
Faced with the challenges that come along with volatile demand, chemical and petrochemical manufacturers have begun to implement cost-cutting measures.[iv] Such measures are aimed at improving operational efficiency to help insulate facilities against disruptive market downturns and rising operating costs. Chemical manufacturers are implementing a variety of cost-saving initiatives, including major changes like workforce reductions[v] and plant closures, as well as streamlining administrative operations. Facilities are also investing in new technologies or overhauling processes in an effort to reduce waste, including water discharge as well as time, energy, and other resources.
Sustainability as a growth opportunity
Sustainability initiatives aim to achieve long-term viability by improving resource use, such as through circularity, conservation, waste minimization, and/or increased efficiency. Over the last few years, perceptions of sustainability programs have begun to shift in the chemical industry, with companies seeing opportunities where they once saw only regulatory compliance obligations.[vi] In a recent report from McKinsey, for example, market data showed that investors see value in sustainable chemical products because they align with consumer priorities and provide sourcing advantages, and because they represent a rapid growth area.[vii] Further, McKinsey analysts found that chemical manufacturers who aggressively invest in sustainability tend to be more competitive and perform better from a financial perspective. [viii]
Chemical manufacturing companies are responding to these trends in a variety of ways. For one, they are redesigning their own processes to make their existing product offerings more sustainable, such as by reducing carbon emissions, or overhauling processes to reclaim water or chemical resources. More innovative initiatives are also beginning to take hold, with some chemical manufacturers replacing fossil fuel-based feedstocks like crude oil, natural gas, and naphtha with renewable feedstocks derived from biomass, like forestry or agricultural residues.[ix] Opportunities related to sustainability are also spurring vigorous research and development into emerging technologies, like green chemistry and green engineering.
Sustainability is also providing growth opportunities for chemical manufacturers in another important way. This is because the chemical industry manufactures an array of products that are critical for building renewable energy infrastructure, such as certain adhesives and silicon carbide used in wind turbines, or specialty chemicals used in batteries,[x] to name just a couple of examples. As the world continues to invest in clean energy and other sustainability projects, chemical manufacturers will likely continue to modify their portfolios to align with demand.
Managing risks
The chemical industry, like many other industries, is facing growing concerns around competition for resources, as well as growing risks of reputational harm or litigation. Such risks include:
- Water scarcity. Chemical manufacturing is a thirsty enterprise, and it is getting more challenging and expensive for facilities to reliably source the water they need. As the ACC notes, competition for water resources is on the rise due to the growth of both population and industry, and reliable access is threatened by extreme weather events, such as droughts or storms that compromise the availability or quality of groundwater or surface water sources.[xi] However, as Bluefield analysts point out, relatively few chemical manufacturers currently use water recycling or reuse strategies, with most opting to simply treat and discharge wastewater [xii] As scarcity becomes a bigger threat, chemical companies may need to consider more ambitious water conservation strategies to ensure long-term viability.
- Carbon emissions. Decarbonization remains a key trend across all industrial sectors, including the chemical industry. KPMG reports that 44% of chemical companies have already implemented or plan to implement internal carbon pricing (ICP) within the next two years.[xiii] This points to a growing recognition that carbon has costs of its own, and manufacturers will need to plan carefully to stay competitive in the future. This will mean overcoming certain challenges, of course, as Deloitte analysts note that many chemical companies struggle to meet decarbonization goals, either because renewable energy sources are not available, or because of the high cost and red tape keeping them from building their own onsite clean energy generation infrastructure.[xiv]
- Waste management. Chemical manufacturers are well-accustomed to complying with regulations regarding handling and disposal of dangerous materials. Bare regulatory compliance goes a long way in insulating a company from risk, but as a recent rise in litigation related to PFAS contamination[xv] shows, chemical manufacturers may need to go further with their own corporate responsibility goals to protect themselves from future risk.
Whether due to pressure from investors, regulatory bodies, non-government organizations (NGOs), consumers, or all of the above, it is likely that chemical manufacturers will continue to revise environmental, social and governance (ESG) goals in the years to come.
Opportunities for water savings in chemical manufacturing
As of 2022, the chemical manufacturing industry was responsible for 14% of water releases across all major industries, according to the Environmental Protection Agency (EPA).[xvi] This places the chemical industry among the top 4 most water-intensive industrial sectors, and projected growth trends would only increase water use in the years to come. Thus, as threats of water scarcity loom, it is important that chemical manufacturing companies look for ways to reduce overall water usage. Here, we’ll take a closer look at major water uses within the industry, and common water conservation strategies for each.
Cooling
Cooling accounts for the most water use of any applications in chemical manufacturing. Chemical manufacturers use cooling systems to absorb excess heat energy generated by chemical reactions, heating systems, or other equipment. Water remains the heat exchange medium of choice because it is able to absorb significant amounts of heat energy, and has historically been cheap and plentiful to source.
How to reduce water use in cooling applications: Once-through cooling systems have the largest water impact, since they use water for only a single cooling cycle before discharging it. For this reason, many facilities are phasing them out in favor of more water-efficient equipment, such as closed-loop cooling towers. Other alternatives include dry-cooling technologies that use air to exchange heat, and fluid coil cooling systems. These types of systems can be a good fit for situations where water conservation is a top priority, and for facilities that can tolerate less cooling efficiency.
Boilers & steam generation
Chemical manufacturers use boilers and steam generators for electrical generation and process heating applications. Because these systems typically involve high heat and pressure, facilities must typically employ some form of boiler feedwater treatment or other pre-treatment to achieve a high enough level of purity to ensure safe operation of equipment.
How to reduce water use in steam generation applications: Facilities can conserve water use by collecting and recycling steam condensate for reuse. When employing this strategy, facilities can reduce the amount of raw water that they need to draw in and treat, however, it is still important to monitor and maintain water quality for recirculated water to protect equipment against scaling and corrosion. Other water savings strategies can include implementing high-efficiency heat exchangers and monitoring for leaks.
Production
Many chemical products use water directly in their manufacturing processes, where it may serve as an ingredient, solvent, reactant, or diluent. Due to the sensitivity of chemical processes, a facility will need to ensure that any water used directly in products is free of contaminants. In most cases, chemical manufacturers employ raw water treatment to achieve this high level of purity.
How to reduce water use in production applications: Depending on the process at hand, it may be possible to capture production solutions for recycling or reuse. In some cases, relatively little treatment is required to treat water for reuse, and added benefits can include opportunities to reclaim valuable materials from spent product streams.
Other uses
In addition to the above applications, chemical manufacturing facilities may use water to clean or rinse equipment and facilities, in sanitary systems, for transportation, or for irrigation and fire suppression, among many other uses.
How to reduce water use in general applications: Chemical companies can cut their overall water use by using degraded water from other plant processes for some of the above general purpose applications. In some cases, this can be done with little to no treatment, while in others, toxic or dangerous constituents may need to be removed prior to use in recycled water applications.
Wastewater produced through any of these processes will need to be treated in some way prior to discharge. Regardless of whether the wastewater is destined for direct discharge to a nearby body of water, or to a publicly owned treatment works (POTW), the facility will need to employ adequate wastewater treatment to comply with any applicable permit limits on regulated constituents in the wastewater. As such, water conservation strategies can be doubly beneficial—not only because they help facilities save on the amount of source water they need, but also because they minimize the amount of wastewater a facility ultimately discharges.
How can SAMCO help?
Over our 40 years in business, SAMCO has designed and manufactured custom water treatment systems that help clients in the chemical and petrochemical industries conserve water and other valuable resources. If you would like to discuss you specific needs, please contact us here to set up a consultation with an engineer or request a quote. We can walk you through the steps for developing the optimal solution for your needs, and realistic cost for your project.
You can also check out our blog to learn more about how industrial filtration and process separation technologies are helping industrial facilities achieve their water management goals. If you’re interested in the topics discussed here, we recommend the following for further reading:
- Water recycling and reuse systems: Strategies for a smaller carbon footprint
- What are the Best Ways Manufacturing Facilities in the Chemical Industry Can Reduce Water Usage?
- Are you in compliance? A checklist to prepare for changing environmental regulations
- Industry Focus: Power industry outlook and impacts on water management strategies
[i] D. Yankovitz, K. Hardin, R. Kumpf, A. Christian, “2025 Chemical Industry Outlook,” Deloitte Insights, Nov. 4, 2024. Retrieved Feb. 19, 2025.
[ii] Ibid.
[iii] American Chemistry Council (ACC), “Chemical Manufacturers Report Rising Cost Pressures and Weak Demand,” Feb. 19, 2025. Retrieved Feb. 19, 2025.
[iv] A. Tullo, “Chemical makers cut costs in slow market,” Chemical & Engineering News, Nov. 11, 2024. Retrieved Feb. 24, 2025.
[v] M. Burke, “Dow to cut 1500 jobs as global chemicals industry reshapes,” Chemistry World, Feb. 6, 2025. Retrieved Feb. 21, 2025.
[vi] J. Arp, A. Domingos, and G. Morris, “Market outlook: Finding ways to rebound from recession,” Reaction Magazine 39 (10), KPMG International Ltd., Jun. 2024.
[vii] O. Ezekoye, H. Lavandier, C. Lorbeer, W. Rehm, & J. Wallach, J., “Chemicals and capital markets: Growing sustainably,” McKinsey & Company, Apr. 22, 2022. Retrieved Feb. 21, 2025.
[viii] Ibid.
[ix] Elsevier, “Key chemicals industry trends in 2025,” www.elsevier.com, Nov. 25, 2024. Retrieved Feb. 21, 2025.
[x] A. Akram, C. Catgiu, and E. Middleton, “The chemistry of the energy transition,” Reaction Magazine 38 (14), KPMG International Ltd., Jun. 2023.
[xi] ACC, “Implementing a Water Body Risk Assessment Framework,” Oct. 18, 2023. Retrieved Feb. 19, 2025.
[xii] Bluefield Research, “Water for Chemicals: Market Trends and Forecasts, 2023–2030,” Nov. 11, 2024. Retrieved Feb. 19, 2025.
[xiii] A. Bajwa, G. Chiles, K. Perry, and M. Roling, “Internal carbon pricing for chemicals and materials companies,” Reaction Magazine 39 (39), KPMG International Ltd., Jun. 2024.
[xiv] D. Yankovitz, K. Hardin, R. Kumpf, A. Christian, “2025 Chemical Industry Outlook,” Deloitte Insights, Nov. 4, 2024. Retrieved Feb. 19, 2025.
[xv] X. Henderson, V. Lott, B. Pilawski, “Shifting PFAS Regulation, Litigation Trends Raise New Challenges,” Bloomberg Law, Feb. 3, 2025. Retrieved Feb. 24, 2025.
[xvi] Environmental Protection Agency (EPA), “Water Releases by Chemical & Industry,” 2022 Toxic Release Inventory (TRI) National Analysis, Mar. 20, 2024. Retrieved Feb. 19, 2025.