Power Generation and How Water Systems Make or Break It
Water and energy are so deeply connected that there’s actually a name for the relationship between the two: the water-energy nexus. Indeed, energy production requires the use or consumption of water; likewise, all of the processes used to draw, transport, heat, cool, treat, or dispose of water or wastewater consume energy.
As water becomes scarcer, and demand for energy grows, power generation facilities will need to find ways to make more efficient use of water. Here, we’ll discuss how water is involved in power generation, why energy producers should consider water conservation, and how water treatment systems are used to meet water conservation goals.
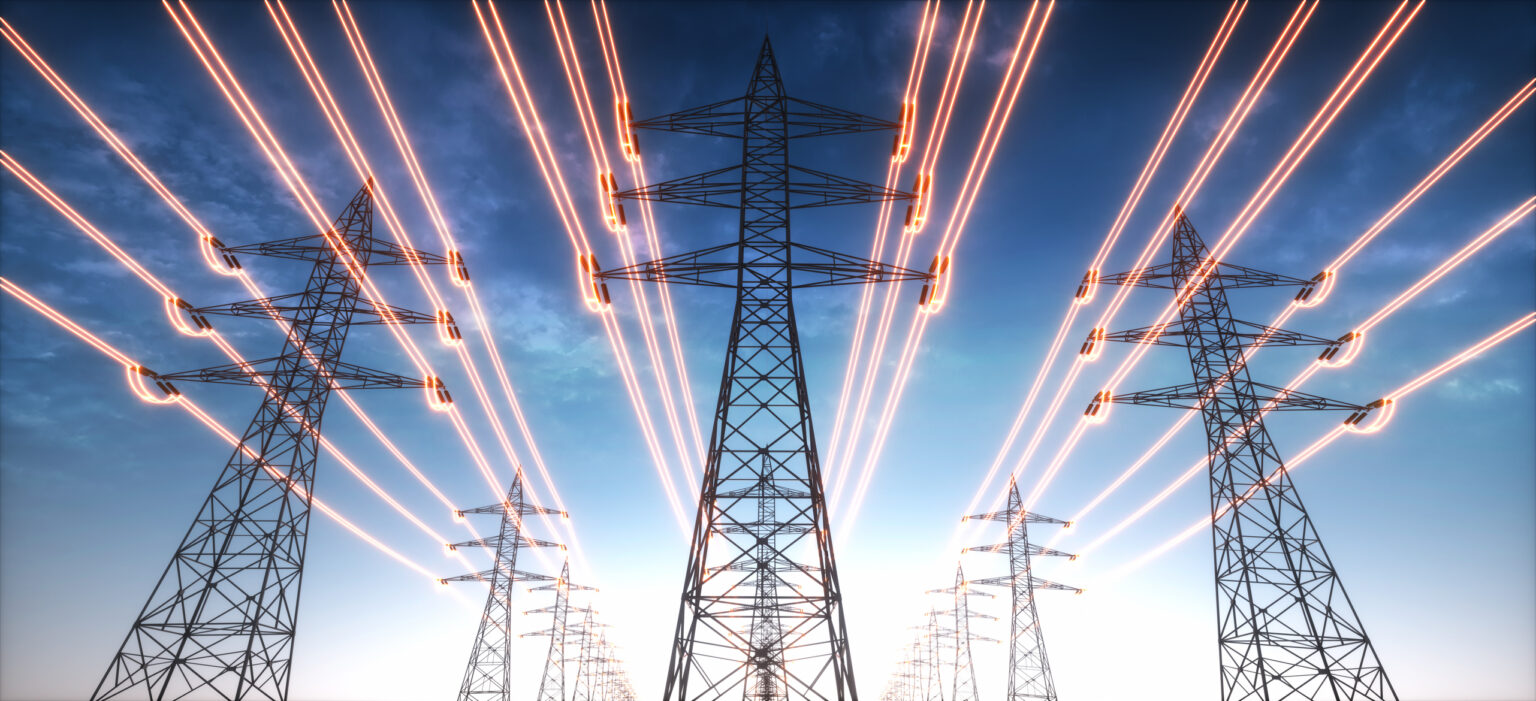
How do power plants use water?
Water uses within the energy sector vary significantly depending on the method of power generation at hand, with renewable energy generation requiring far less water than thermoelectric processes. Thermoelectric plants are responsible for most of the world’s energy production, with at least 82% of energy derived from fossil fuels, and about 4% from nuclear energy as of 2021. For this reason, we’ll focus on the major types of water usage at thermoelectric plants, which include:
-
-
- Internal energy transfer: Thermal power plants work by consuming some type of fuel (e.g. coal, natural gas, uranium) to heat water and produce steam. The steam drives turbine generators to produce electricity.
- Cooling: Water vapor exiting from the turbine is collected and condensed through the use of a cooling system. The quantity of water used or consumed will vary significantly depending upon the type of cooling system used, with closed-loop, dry cooling, and hybrid cooling systems all requiring much smaller volumes of water than once-through systems.
- Emissions control: Many thermoelectric plants are equipped with emissions control systems that are used to capture air pollutants released by the combustion of fuel. These systems require significant amounts of water to operate.
-
But water costs for energy generation don’t end there. Indeed, lots of water is needed to produce the fuels consumed by power plants, so most analyses of the water-energy nexus also consider water impacts across associated industries as well. This can include water used in mining and extraction of materials like natural gas, coal, oil, and uranium, as well as refinery operations to convert raw materials to useable fuels. Additionally, long-distance coal transport is sometimes accomplished by slurry pipelines, which also require large amounts of water.
What is water conservation and why is it important for power plants?
At the present moment, the power industry is facing some unique challenges. On the one hand, energy demand is growing, and is expected to continue to do so in the long term. On the other hand, water resources are becoming increasingly scarce, meaning that new and existing facilities can no longer depend on affordable access to large volumes of water. In short, power plants will need to do more with less (water). Already, some energy producers have seen negative impacts of drought and water scarcity on their operations, and are increasingly looking at water conservation strategies as a means to meet growing demand and stay viable in future years.
But water conservation strategies are far from universal. What works well for one power plant might not be feasible for another. Below, we’ll briefly look at some water conservation strategies for power plants, and outline key benefits and drawbacks.
Cooling systems
Once-through cooling systems draw the highest volumes of water compared to any other type of cooling system. While they are among the cheapest methods of cooling, they are no longer employed by a majority of power plants due to stricter regulation of water withdrawals in recent years. Switching to another type of cooling system is a potential option for saving water, with available alternatives including closed-cycle wet cooling systems, dry cooling systems, or hybrid cooling systems. While each of these can yield a moderate to significant water savings, they also have tradeoffs in terms of efficiency, so they must be matched to the proper plant and operating conditions. Dry cooling systems, for example, nearly eliminate water use, but they are inefficient to operate in hot weather, meaning that a plant’s output may be inconsistent during warmer seasons. For this reason, dry cooling systems have somewhat limited adoption, such as in water-scarce areas or regions with mild climates. Additionally, because cooling systems are so integrated into the overall design of a power plant, it’s not always possible to simply “switch” to an alternative cooling method as part of a retrofit project. Still, though, water efficiency can and should be a priority when planning a new facility so long as it can be balanced with any performance or energy costs.
Water reclamation and recycling
Water used for energy generation and cooling doesn’t have to be drawn from surface or groundwater. Instead, some facilities have had success with using alternative water sources, including:
-
-
- Seawater or brackish water
- Produced water from oil or gas wells
- Treated sewage effluent
- Stormwater
- Agricultural runoff
- Recycled wastewater
-
Using alternative water sources can save on costs, as degraded streams like these are typically viewed as unwanted wastes. A facility will, however, need to invest in proper water treatment systems to ensure its water is suitable for its intended purposes, and such an investment may well cut into cost savings. The cost-effectiveness of this strategy will also vary depending on the location of the plant and the availability of nearby alternative water sources.
Smart devices and new technologies
Newer approaches to water conservation entail the adoption of smart technologies to track water use, and find opportunities for reducing waste. This trend, also known as digitalization, employs the use of smart sensors, monitoring and automation devices, and analytics tools to collect and use data to make process improvements. While the use of these types of technologies don’t tend to make as huge of an impact as, say, switching to dry cooling or implementing a water recycling program, they are reasonably easy to implement, and are effective in helping plants to reduce both water and energy usage, and run more consistently and efficiently.
How do water systems affect power plant performance?
Power plants may rely on an assortment of water systems, such as boiler feedwater treatment, cooling tower water treatment, wastewater treatment, and zero liquid discharge (ZLD) systems. The reasons for adopting these technologies vary depending upon the plant’s needs and priorities, but water treatment systems can help to meet objectives including:
-
-
- Safety: boilers and other equipment that are operated at high heat or pressure are very sensitive to certain types of contaminants. Water treatment systems help to manage influent water chemistry in order to promote consistent performance, and prevent unsafe operating conditions.
- Efficiency: A properly designed water treatment system can boost efficiency by optimizing water quality for a given process. For example, removing hardness or silica can help to reduce the amount of energy needed to heat boiler feedwater, as these contaminants inhibit heat transfer. Likewise, employing water treatment technologies to remove hardness can help to prolong equipment service life by preventing damage due to issues like scaling and corrosion.
- Reuse and reclamation: Plants looking to cut down on water withdrawals or discharge volumes can sometimes do so by recycling their own wastewater, or sourcing wastewater from other facilities. In most cases, some form of water treatment will be necessary to bring the reclaimed water up to an appropriate level of quality for the intended application. While there are capital and ongoing costs to transport and treat reclaimed water, it may well be worth it, since reuse can help provide a more affordable and consistent source of water, especially for plants in water-scarce or drought-threatened regions.
- Regulatory compliance: As in any other industry, power plants must operate in compliance with relevant regulations—or face hefty fines or other consequences. Water treatment systems can help facilities by removing dangerous contaminants from wastewater or reducing wastewater volumes in order to comply with permitted limits.
-
Can SAMCO help?
SAMCO has over 40 years’ experience in the design and manufacture of water treatment systems for a range of applications within the energy sector, so please feel free to reach out to us with your questions. No matter whether your goals include water conservation, process optimization, or compliance, SAMCO will work with you to plan a treatment solution around your priorities.
Feel free to contact us here to set up a consultation with an engineer or request a quote. We can walk you through the steps for developing the proper solution and realistic cost for optimizing water use at your power generation facility.
For more information, head on over to our blog to learn more about the role of water treatment in the energy sector. Some articles that might be of specific interest to you include:
-
- Industry Focus: How the Power Industry is Evolving and What it Means for Your Wastewater Management Strategy
- Five Ways Your Industrial Facility Can Conserve Water and Plan Ahead for Shortages
- Can Your Facility Save Money by Reducing Its Water Consumption?
- Do You Need a Boiler Feed Water Treatment System for Your Plant?
- How Do You Know If You Need a Cooling Tower Water Treatment System for Your Plant?