How to Choose a Membrane
Membrane filtration is one of the most energy efficient, compact, and cost-effective separation technologies available. To really seize on these benefits, though, it is essential to have a good system design that fits the process at hand. Since so much of the system design depends on the membrane itself, we’ve compiled some important considerations for selecting a membrane to ensure optimal system performance and maximum ROI.
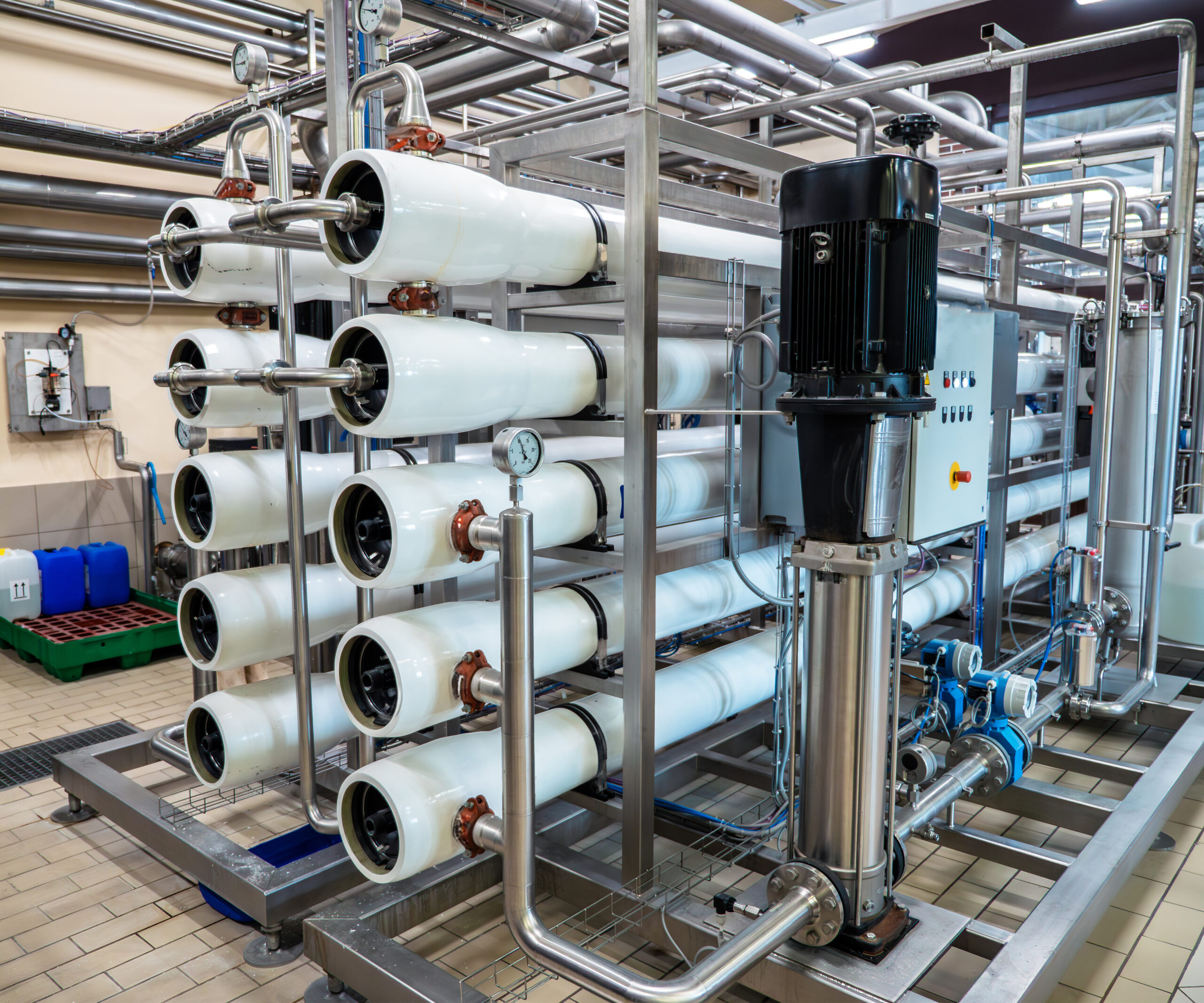
What is a membrane?
To get a sense of how membranes work, imagine straining pasta with a colander. The water flows right through the holes, while the pasta stays behind. A membrane works a lot like a colander in this example, except with a much greater level of precision that allows you to separate out dissolved starch molecules and even salt ions from the water. In essence, a membrane is basically a thin, porous barrier that physically separates microscopic particles from a liquid stream.
Filtration membranes are available in numerous shapes, pore sizes, and materials to fit a variety of specialized separation and water treatment needs. Navigating all the options out there can be overwhelming, so we’ve broken down some key factors that will help to determine the best membrane for your application.
What to consider when choosing a membrane
Membrane selection starts with a good understanding of the stream or streams in need of filtration. To achieve the best performance, you’ll want to consider what materials are present in the stream to be treated, the concentration, pH range, and process conditions, like temperature and flow rate, as each of these will have some bearing what membranes will work best for your application.
Membrane filtration type
A critical first step determining what type of membrane is needed is first determining what type of filtration is needed. This is done by identifying all the materials present in the stream, and selecting the type of filtration based on the size and molecular weight of the substances present in the stream, and which constituents need to be separated out.
This is because membrane separation works on the principle of size exclusion—in short, the membrane acts as a barrier for any particles too large to fit through its pores. There are four main types of membrane filtration, each defined by a specific range of pore sizes:
Type | Size Range | Types of Contaminants |
Microfiltration (MF) | 0.1 – 10 μm | Algae, bacteria, protozoa, yeast, sand, clay, metal particles |
Ultrafiltration (UF) | 0.001 – 0.01 μm | Colloids, plastics, proteins, silica, silt, some viruses, and endotoxins |
Nanofiltration (NF) | 0.002 – 0.005 μm | Larger organic molecules, most viruses, pesticides, and multivalent ions such as calcium or magnesium |
Reverse Osmosis (RO) | 0.0001 μm | Nearly all minerals and monovalent ions |
In general, it’s best to use the coarsest type of filtration possible while still achieving the desired level of separation. As an example, let’s say a dairy processing plant needs to separate out proteins from whole milk. Ultrafiltration (UF) would be useful here because its pores are fine enough to collect the desired protein molecules, but open enough to permit higher flow rates than NF or RO. It is also very common to see multiple types of membrane filtration deployed in sequence. So, in this example, you might see MF used first to separate out large particles like fats and bacteria, followed by UF for protein separation, and finally RO to remove excess water from whey concentrate. Combining different types of membrane filtration in this way allows for very selective separation of liquid streams, allowing for efficient operation with minimal clogging and fouling, as well as recovery of byproducts.
It’s also important to note that most membrane separation units will require some form of pre-treatment. This can include processes like clarification, media filtration, or chemical addition, as appropriate to the feed stream. Pretreatment is important to improve membrane efficiency, and prevent issues like membrane degradation, fouling and scaling, particularly for finer separation technologies like nanofiltration and reverse osmosis.
Membrane element structure
Membrane elements come in a variety of shapes and sizes, each of which offer their own advantages and disadvantages. Common element types include:
- Plate and frame membranes use flat sheets of membrane material that are held by flat frames housed within a larger unit. They are resistant to fouling, and they offer easy cleaning and maintenance, so they are a good fit for streams with high solids content. Their main disadvantage is that they offer relatively low surface area compared to other membrane configurations.
- Tubular membranes consist of an outer housing with a bundle of tube-shaped membrane elements inside. Tubular membranes are best for streams with high TSS or TDS or high oil content since they are easy to clean and resist clogging. Their main disadvantage is moderately low surface area for their size, compared to other membrane configurations.
- Hollow fiber membranes are like tubular membranes, but the elements are much smaller in diameter, giving them greater packing density and thus greater filtration efficiency. Hollow fiber membranes are suitable for low to moderate TSS or TDS and can be operated at low feed pressure. Their main disadvantage is susceptibility to clogs and breakage.
- Spiral-wound membranes consist of layers of membrane material wound around a perforated core. They have the greatest surface area for their size, but this higher packing density means that they are not suitable for streams with larger particles, since they can clog easily.
Membranes for challenging streams
Certain constituents in a stream or process conditions can create some added constraints around what membranes might be appropriate for the application at hand. To ensure the best performance, be sure to account for these types of challenges when selecting a membrane.
High TSS
Streams with a high level of total suspended solids (TSS) contain a lot of floating particles, which can include sand, clay, silt, metal particles, microorganisms or other materials. These particles can wear the membrane material, build up on the surface of a membrane or become lodged in tight spaces of the membrane element. High TSS streams can impede flow or cause pressure to build up, resulting in subpar performance, and the potential for premature membrane failure.
For streams with high TSS, it is generally best to pretreat the feed water using technologies like sand filters, cartridge filters, or clarification to remove excesss solids. In general, the larger the pore size, the more resistant a membrane is to clogging. For this reason, MF and UF are often used ahead of NF and RO to enhance downstream membrane performance. Additionally, choosing membrane shapes with a more open structure, like tubular elements or flat sheet membranes, will also help to prevent clogs and simplify routine cleaning. Finally, if the stream contains abrasive particles, like sand or metal fragments, it is important to choose a membrane material that resists mechanical damage. Some polymeric materials stand up to abrasion better than others; these include cellulose acetate, cellulose nitrate, and polyvinylidene fluoride (PVDF). Ceramic and metal membranes are much more durable than polymeric membranes, however, they are more costly.
Thick or viscous liquids
Filtering thick liquids like oils, sugar syrups, chocolate, paints, solvents, waxes, adhesives, coatings, silicone, glycol, and other products all pose challenges because their innate flow resistance makes it difficult to pass them through a filtration membrane. High-viscosity liquids will typically demand membranes with larger pore openings and higher operational pressures, as well as membrane materials that can withstand high differential pressures. Additionally, the stream composition should be considered when selecting a membrane material. Hydrophilic (or “water loving”) polymer materials tend to perform best for filtering aqueous streams, since their natural affinity for water helps to reduce flow resistance. Examples of common hydrophilic membrane materials include polysuphone (PSU), polyethersulfone (PES), polyamide (PA), or cellulose acetate (CA).
Conversely, hydrophobic materials like polyvinylidene fluoride (PVDF) or polytetrafluoroethylene (PTFE) are best for streams comprised of oils, alcohols, or organic solvents, since these materials reduce resistance and back pressure from non-aqueous streams. It’s also worth noting that some membrane materials can be chemically modified to either repel or attract water. An example of this is modified PES, which is innately hydrophilic, but can be modified to take on hydrophobic qualities for certain applications. In some cases, flow resistance can also be mitigated by using a wetting agent.
Aggressive chemicals
Aggressive chemicals like acids, bases, chlorine, or solvents can degrade polymeric membrane materials, leading to premature membrane failure, and potential contaminant leakage. Many of the polymers typically used in membrane elements resist damage from some chemicals but not others, so it is important to pay close attention to chemical compatibility. Take, for example, the very common membrane material PES, which stands up to hydrochloric acid (HCl), but is not suitable for use with nitric or sulfuric acid. Similarly, PVDF membranes are suitable for use with cyclohexane but not cyclohexanone, although both are organic compounds used to manufacture nylon.
For streams that contain particularly aggressive organic solvents, strong acids, or strong bases, it is worth considering inorganic ceramic membranes. Comprised of materials like aluminum oxide, zirconium oxide, titanium oxide or silicon carbide, ceramic membranes are more durable and chemically inert than polymeric membranes, allowing them to stand up to harsh chemicals. While they typically cost more than polymeric membrane materials, ceramic membranes can more than make up for their higher upfront cost by delivering a long service life.
High temperatures
If you deal with hot liquids or use heat sterilization as part of your process, be sure to select a membrane material that supports the needed range of operating temperatures. Thermal stability can vary greatly from one polymeric membrane material to the next, and some materials may melt, rupture, or deform if they are exposed to high temperatures. Many polymeric membrane materials like polyamide, PSU, and PVDF are thermally stable at moderately high temperatures of 300°F or less. CA and PES have somewhat higher heat tolerance, at 354°F and 437°F, respectively. For very high temperatures, it is best to use inorganic ceramic or metal membrane materials, as these will tolerate temperatures exceeding 600°F.
How can SAMCO help?
SAMCO has over 40 years’ experience in the design and delivery of custom water treatment and process separation systems for a range of industrial applications, so if you’re wondering about how membrane filtration might work for your process, contact us to request more information or set up a consultation with an engineer. Our team of experienced professionals will help you explore membrane separation technologies and design a solution that aligns with your goals and budget.
To learn more about membrane filtration and other process separation technologies, click on over to our blog. There, you’ll find articles on a range of relevant topics, such as:
- Ultrafiltration: common industrial applications and uses
- What is Reverse Osmosis and How Is It Used For Industrial Applications?
- How Much Do Reverse Osmosis and Nanofiltration Systems Cost?
- Does Your Facility Need a Reverse Osmosis or Nanofiltration System?
- What Are the Different Types of Membrane Fouling and What Causes Them?