How Do You Enhance Lithium Concentration and Recovery from Brine Streams?
As cell phone and electric car markets grow, and they are expected to grow substantially, so will the demand for lithium, a highly reactive alkali metal that offers excellent heat and electrical conductivity. This metal is also used to manufacture glass, high-temperature lubricants, chemicals, and pharmaceuticals. However, because of its high reactivity, pure elemental lithium is not found in nature but instead is present as a constituent of salts or other compounds. Similarly, most commercial lithium is available in the form of lithium carbonate, which is a comparatively stable compound that can be easily converted to other salts or chemicals.
Extracting and processing lithium can depend heavily upon the source; lithium exists in different concentrations and states alongside other valuable metals and minerals, which will vary depending on where the lithium is found. Many methods and technologies for extracting and processing lithium can be inefficient or costly and many difficulties than can arise while managing these often-problematic brine streams.
There can be many variables when discussing this topic and the scenarios and methods can get a bit complex, so this article will look at some of the more typical ways to “enhance lithium concentration and recovery from brine streams” that are widely used today. Please also keep in mind that many of these methods can be used for extracting AND concentrating lithium, and sometimes in conjunction with each other to yield even better results.
Adsorption
One of the methods researchers continue to pursue include using sorbents to adhere to the lithium for selective removal. Lithium ions attach to the sorbents while unwanted ions are washed away. This can be used to extract lithium from geothermal brines, waste brines, or seawater.
Some methods require an acidic solution to wash the sorbent, which can leave your facility with problematic waste, but some recently formulated sorbents that require diluted lithium chloride for rinsing are touted as being more environmentally friendly. As this method is tested and made more efficient, recovery rates could increase.
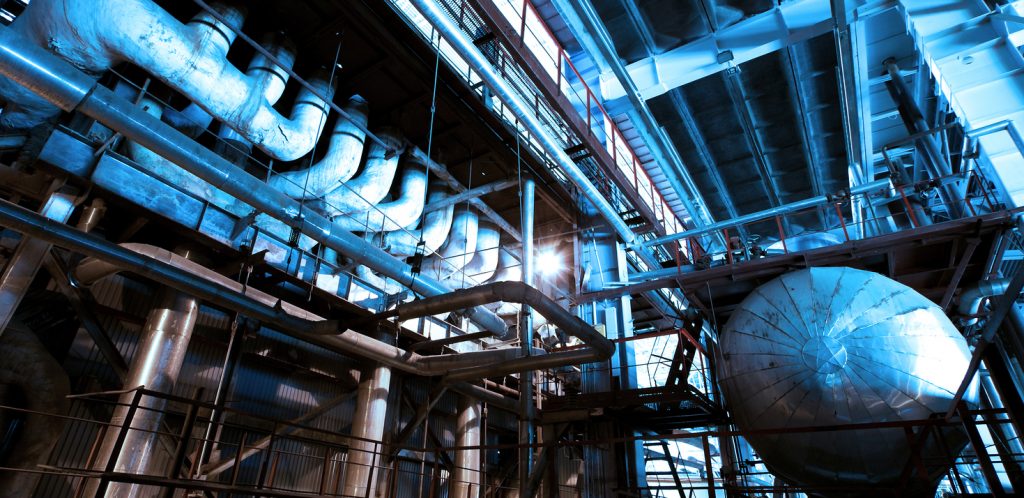
Reverse Osmosis
Reverse osmosis, or RO, is using high osmotic pressure is used to push permeate through a semipermeable membrane while trapping and filtering out any contaminates larger than the pure water that passes through to the lower-pressure side. RO leaves you with pure water and a highly concentrated reject stream that is either used or discarded, depending on the separation/concentration needs of the facility.
In the case of using RO for concentrating lithium, it is often used as a means of providing a higher concentrated stream, such as a concentrate dilute lithium bicarbonate solution to near saturation for downstream lithium carbonate production or prior to evaporation, and is usually used as part of a stepwise process or larger treatment train when it comes to concentrating lithium.
Ion exchange
When contaminant removal needs are highly specific, such as pulling lithium from geothermal brines, wastewater brines, or seawater, many times IX chelating resins are ideal. IX systems can be used to remove selected contaminants from the stream so lithium can be extracted more efficiently, and these systems can also be used to extract the lithium itself.
In general, using IX to recover and concentrate lithium is done more or less by:
-
-
- removing divalent metal ions with cation IX resins
- removing sodium and potassium with a specialty IX resins
- recovering lithium as a precipitate of lithium carbonate
-
Since sodium and potassium, along with other metals and minerals, can be present is higher concentrations than lithium, it is often recommended that these be removed first to improve lithium recovery rates. Although there are countless other methods for selecting lithium for removal, these general steps, however they are carried out, are typically pursued with selective removal methods such as IX.
Electrodialysis
Electrodialysis is also a form of ion exchange that can be used to separate out and concentrate lithium. It’s a process that uses positively or negatively charged ions to allow charged particles to flow through a semipermeable membrane and can be used in stages to concentrate the brine.
This process can be complex to get just right; minor variations in acidification levels, current strengths, temperature fluctuations, and membrane configurations could greatly affect the rate at which lithium can be extracted and concentrated.
Precipitation
Some methods for extracting and concentrating lithium from brine use precipitation as a means for isolating the metal. Using precipitation will usually require several steps, as you need to precipitate and isolate the lithium (usually in the form of lithium chloride), and further separate it out.
For example, a study done by the Bureau of Mines was able to yield a 99% recovery of lithium with precipitation. First, they treated brine samples with a lime slurry to increase the pH. Next, they used filtration technologies to remove iron, manganese, lead, and zinc. The resulting lithium/aluminum precipitate was then dissolved, separated, and evaporated out in a series of mixing, rinsing, and filtration steps.
Evaporation
Lithium brine recovery by evaporation is typically a straightforward but lengthy process that can take anywhere from several months to a few years to complete. Brine is distributed among evaporation ponds for a period of months or years until most of the liquid water content has been removed through solar or wind evaporation. Facilities usually operate several large evaporation ponds of various ages and may extract other metals (e.g. potassium) from younger ponds while waiting for the lithium content to reach a concentration optimal for further processing. In some cases, and as mentioned prior, RO is used to concentrate the lithium brine to speed up the evaporation process.
Once the brine in an evaporation pond has reached an ideal lithium concentration, the brine is pumped to a lithium recovery facility for extraction. This process varies depending upon the brine field composition, but usually entails the following steps:
-
-
- Pretreatment. This step usually employs filtration and/or ion exchange (IX) purification to remove any contaminants or unwanted constituents from the brine.
- Chemical treatment. Next, a series of chemical solvents and reagents may be applied to isolate desirable products and byproducts through precipitation.
- Filtration. The brine is then filtered to separate out precipitated solids.
- Saleable lithium production. The brine is finally treated with a reagent, such as sodium carbonate to form lithium carbonate, and the product is then filtered and dried for sale. Depending upon the desired product, different reagents may be applied to produce other commonly sold forms of lithium, such as lithium hydroxide, lithium chloride, lithium bromide, and butyl lithium.
-
Once the lithium extraction process is complete, the remaining brine solution is returned to the underground reservoir.
Can SAMCO help?
SAMCO has over 40 years’ experience in identifying appropriate brine and water treatment solutions to help lower costs and waste volumes while increasing lithium production yields. For more information or to get in touch, contact us here to set up a consultation with an engineer or request a quote. We can walk you through the steps for developing the proper solution and realistic cost for your brine waste treatment system needs.
To learn more about SAMCO’s innovative technologies that we commonly apply for lithium production facilities, visit our page on brine and lithium recovery, softening, and purification.
To learn more about lithium recovery, read these other blog articles that might interest you:
- How Much Does It Cost to Extract Lithium from Geothermal Brine or Crushed Ore?
- Best Companies for Extracting Lithium from Geothermal Brine and Other Produced Water Streams
- Is it Possible to Extract Lithium from Seawater?
- What Is the Best Way for Recovering Lithium from Geothermal Brine?
- What is Lithium Extraction and How Does It Work?
- How is Brine Mining Used for Lithium Recovery?