What Is DOWEX UPCORE™ Ion Exchange and How Does It Work?
As your facility navigates the various available process water treatment options, perhaps you’ve heard of ion exchange—or, even more specifically, DOWEX UPCORE™—throughout your pure-water solution research. Especially useful for industrial facilities that power their process with steam, these water filtration technologies can increase the efficiency of your process while increasing water demineralization capabilities, essentially providing higher quality water with a safe, compact, and low-cost technology. If you’re interested in learning more about what DOWEX UPCORE™ ion exchange is and how it works, this article provides a general overview of the topic, including a bit of the history of ion exchange and how the conventional methods were improved upon over the years to bring you this vastly improved technology, so you can better understand whether this might be a good solution for your industrial plant.
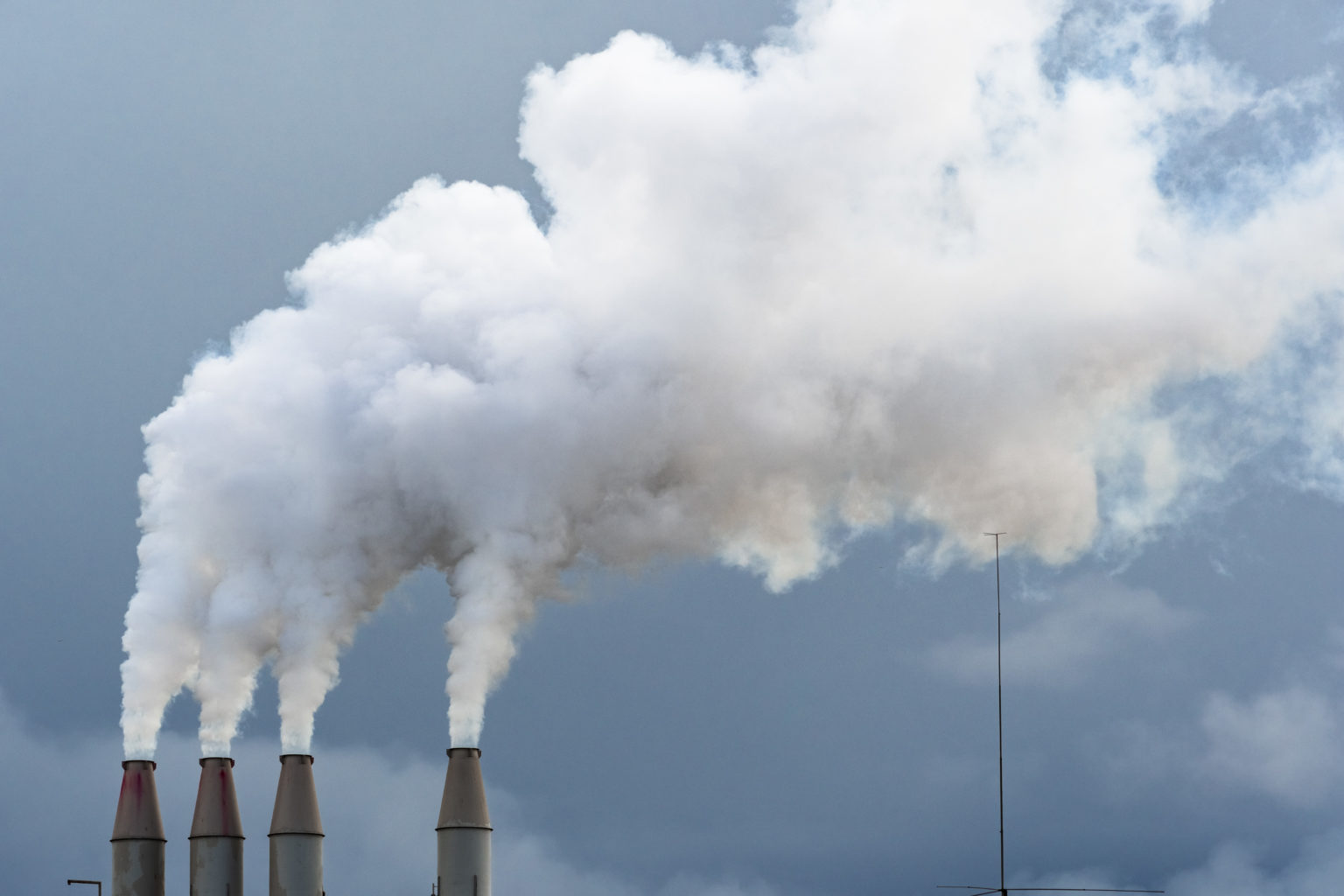
What is DOWEX UPCORE™ Ion Exchange?
In its most simplified form, DOWEX UPCORE™ is an ion exchange technology that utilizes downflow currents for service cycles and upflow currents for regeneration. Because this technology has two different flow patterns, it’s known as a “counter-current” technology. This technology was developed over time to improve conventional ion exchange technologies that flowed in one direction for both its service and regeneration cycles, both going downwards by gravity in what is known as “co-current” technology (more on these processes later in the article).
For industrial facilities looking to create high-purity water from their raw water source, whether it draws from a lake, river, well, or local municipality, these systems often exhibit a large improvement in a variety of ways.
They can be ideal solutions for industrial facilities looking to:
-
-
- increase demineralizer flows; for example, 500 gallons per minute (GPM) of demineralized water to 1,000 or more
- decrease chemical use; in some cases, this technology can help your facility cut its chemical usage by more than half
- improve water quality; this technology drastically improves water quality, which can be beneficial for industries that use steam in its processes
-
In short, DOWEX UPCORE™ is an ion exchange system that can help your industrial facility increase the flow of demineralized water it is able to access while decreasing chemical use and providing a much higher-quality water for making steam than other more conventional technologies, all while decreasing the amount of waste your facility creates.
How Does DOWEX UPCORE™ Ion Exchange Work?
Like other ion exchange technologies, DOWEX UPCORE™ removes scale-forming calcium or magnesium ions from raw water and other solutions. When the solution passes through an ion resin composed of concentrated sodium ions, the calcium and magnesium ions are effectively captured from solution and held by the resin, while the sodium ions are released from the resin into the effluent stream.
In order to understand how DOWEX UPCORE™ differs from conventional ion exchange technologies, however, we need to examine how the conventional technologies worked and the ways in which DOWEX UPCORE™ have improved upon the process.
Conventional ion exchange and the need for something better
When ion exchange technology was first invented, it was generally used for creating high-quality boiler feed and makeup water as a co-current technology. What co-current means is the raw water being demineralized goes from the top of the resin bed, through the vessel, and exists from the bottom of the resin bed. Then, once the resin bed is exhaustedand requires replenishing (whether it is hydrogen replenishment for the cation resin or the hydroxide replenishment for the anion resin). The regenerant chemicals also follow the same path, being fed into the top of the bed and exiting the bottom. So, as described here, “co-current” simply mean that both the service and regenerant cycles flow downward through the vessel, using the same direction.
This co-current technology, for some time, was a common practice. Those designing and using the original co-current ion exchange technologies found the vessels required a very small number of internal parts (all that was basically needed was a big vessel or tank where the resins sat on a plate with a perforated strainer at the bottom), which was a good thing. But soon people realized the co-current technology needed improvement, especially when it came to minimizing chemicals and increasing efficiency when regenerating the resins.
How conventional co-current ion exchange technologies work
During the ion exchange demineralization process, determining if the bed is exhausted and in need of regeneration is accomplished by measuring conductivity. Ion exchange vessels need to be taken out of service for regeneration once this meter shows a conductivity of around one microsiemen. This means the system can no longer demineralize the raw water to the quality desired and the resin beads need to be replenished.
What many found is that sodium—which results from ion exchange on sodium chloride (sodium coming from the ion exchange process of the cations and chloride coming from the ion exchange process of the anions)—was the main driver of this increase in conductivity.
Now, in a normal service cycle, resin has a high affinity for multivalent cations (Ca2+, Mg2+, etc.) so they naturally gravitate toward the top of the bed. Sodium, on the other hand, is monovalent (Na+) and settles toward the bottom of the bed. During conventional ion exchange co-current regeneration, the regeneration acid is coming from the top and it is displacing everything to the bottom, so the top of the bed is extremely polished, and the sodium, which, again, is the cause of the breakthrough for the conductivity, is receiving the weakest acid possible in the co-current, meaning the acid isn’t able to treat the sodium (which is needed most) as quickly and efficiently by the time it get to it in the bottom of the bed.
How DOWEX UPCORE™ counter-current ion exchange technologies improve regeneration
As we explained above, ion exchange resins have a low affinity for monovalent cations, so the monovalent cations naturally settle toward the bottom of the bed. And sodium, being one of them, comes into contact with a much stronger regenerant acid when the acid is pushed up into the vessel from the bottom. Since the sodium is the element that needs a stronger acid the most (because it causes the conductivity and accelerates the need to run a regeneration cycle), having the acid enter the bottom of the system helps the regeneration cycle become more efficient, reducing the need to use as much acid and increasing its effectiveness in treating the sodium, making the counter-current technology far superior in this way to the conventional co-current method.
How DOWEX UPCORE™ counter-current internal design improves distribution and decreases waste
DOWEX UPCORE™ is also beneficial in the way its internal design improves upon the way your regeneration waste exits the vessel. With the chemical (acid or caustic) coming in the bottom of the vessel, the upflow can fluidize the resin beads, which would decrease the contact efficiency the resin beads would have with the chemical solution, thereby decreasing its ability to recharge the resins. Some of the original counter-current ion exchange system designs utilized a simultaneous downflow of water while the acid was coming in and up the vessel to block the beads from moving around. This “water block” was used to hold the beads in place, increasing the contact time with the acid, and forcing all the dilute acid and water waste to exit through the side of the tank (versus the bottom of the tank in conventional ion exchange technologies).
One of the issues many began to see with this design included the inability to control the flow of acid in the vessel. What people continued to see was that there wasn’t a way to process a 1,000 GPM flow of raw water during the service cycle then decrease this to 100 or 200 GPM flow of acid during the regenerating flow without adding an overly excessive number of distribution lines and connectors, making the technology too expensive to build and impractically complex.
To solve this, DOWEX UPCORE™ uses a top and bottom plate, which accomplishes the counter-current with minimal internal distribution hardware. These plates are also useful in performing backwash cycles, which helps cut chemical cost, and the bottom plate is fitted with special nozzles that restrict the flow depending on the direction. For example, some of the nozzles in the bottom contain small balls that will plug the flow when acid is added from the bottom of the vessel. They also open up allowing larger flows when the system is in service, allowing the system to seamlessly switch from 1,000 GPM service cycles to 100 GPM regeneration despite having a much simpler internal design.
Also, in most conventional resin beds, the vessel can be double the size of the space the resins take up, yet with DOWEX UPCORE™, the resin and vessel heights are nearly equal. This results in less resin volume and a smaller vessel, making the system much more compact. As a result, you use far fewer chemicals and much less water, often by half.
Can SAMCO help?
-
SAMCO has over 40 years’ experience in identifying efficient IX resin technologies and regeneration strategies to minimize downtime and maintain consistent product quality. For more information or to get in touch, contact us here to set up a consultation with an engineer or request a quote. We can walk you through the steps for developing the proper solution and realistic cost for your IX treatment system needs.
To learn more about SAMCO’s IX resin solutions, visit our pages on our innovative ion exchange resin technologies and off-site resin regeneration services.
If you want to learn more about ion exchange resins, these other articles might be of interest to you:
- How Much Does It Cost to Buy, Maintain, and Dispose of Ion Exchange Resins?
- Common Problems with Ion Exchange Resins and How to Avoid Them
- What are the Best (and Cheapest) Ways to Dispose of Ion Exchange Resins?
- What is the Difference Between Cation and Anion Exchange Resins?
- What Are the Different Types of Ion Exchange Resins and What Applications Do They Serve?
- What Are the Best Ion Exchange Resin Manufacturing and Supply Companies?
- What Is Ion Exchange Resin and How Does It Work?