DOWEX UPCORE™ Ion Exchange: Design Considerations for Optimal Performance
For most facilities, DOWEX UPCORE™ technology offers a variety of benefits over other ion exchange technologies, such as greater flexibility in capacity, less chemical and water consumption, and reduced maintenance. UPCORE™ is in many ways a superior ion exchange technology for process water treatment, however, as with any ion exchange system, improper system design, use, or maintenance can compromise performance.
Whether you’re interested in converting an existing plant to UPCORE™ or exploring process water treatment technologies more generally, you’ve no doubt wondered about common problems that affect system performance. In this article, we’ll explore some key system design considerations to optimize performance of DOWEX UPCORE™ ion exchange technology.
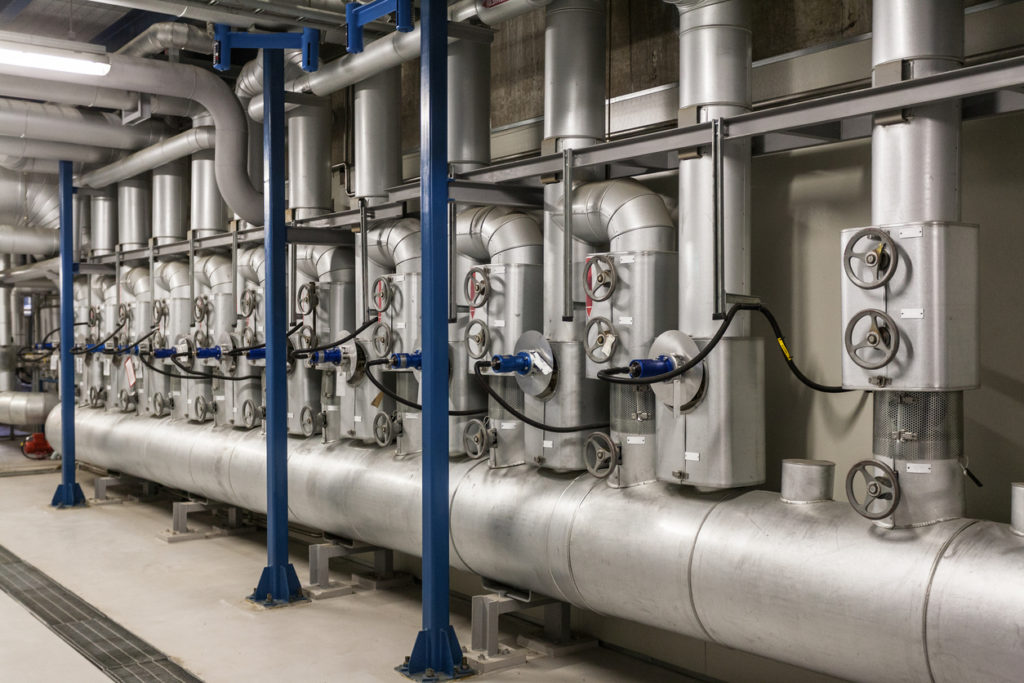
Distributor design and condition
UPCORE™ technology consists of a countercurrent design with service cycles operated in a downflow direction, and regeneration cycles operated in an upflow direction. The IX vessel will therefore include some type of inlet distributor mechanism to evenly disperse the flow of water over the resin during a service cycle. During the course of use, distributor components such as header laterals and nozzles, may become clogged or damaged, resulting in uneven application of water to the resin bed. These uneven flows of water can cause channeling, an issue where water displaces the resin beads rather than flowing around them. Channeling can pose problems due to uneven exhaustion of the resin, and breakthrough of untreated solution into the effluent stream.
To ensure optimal system function, facilities should include routine inspection and cleaning of distributor components as part of their normal maintenance program. It is also a good idea to thoroughly inspect, clean, and repair all distributor components whenever resin replacement is needed. In short, taking steps to ensure that header laterals or other distributor components are performing properly will ensure stable and predictable performance of UPCORE™ systems.
Design of inert layer and freeboard
One of the key benefits of UPCORE™ technology is its self-cleaning ability, meaning that no separate backwashing step is needed to eliminate particulates from the resin bed. However, improper design of the inert resin layer and freeboard space can compromise water quality and self-cleaning performance.
Inert resin layer depth
In UPCORE™ systems, the resin beads not only facilitate ion exchange reactions, but they also serve a secondary purpose: by acting as a media filter to capture suspended solids present in the feed water. These suspended solids and resin fines (fragments of damaged resin beads) rise to the top of the resin bed during regeneration, and remain on the top surface of the resin bed for the next downflow service cycle. The particulates are then flushed from the system during the compaction step of the next upflow regeneration run, with no additional backwashing step required.
For this self-cleaning process to work as intended, the IX unit must have an adequate layer of inert material in addition to the charged resin layer. Proper depth of the inert layer is a critical factor in maintaining optimal self-cleaning performance, as it must allow spent regenerant chemicals, rinse water, and suspended solids to flow through so that they may be easily flushed out of the system. Insufficient inert layer depths may allow the resin beads to migrate through, resulting in problems such as lateral blockages or excessive resin losses. On the flip side, when the inert resin layer is too thick, particulates may lodge there, unable to exit the vessel with the effluent waste stream.
Freeboard space
Another factor that determines the effectiveness of the self-cleaning capability is the amount of freeboard space within the IX vessel. The freeboard allows for expansion and classification of the IX resins during service and regeneration cycles. For most units, proper system design should include a minimal amount of freeboard space while still accommodating resin expansion. A competent system design should recognize that the amount of freeboard space needed will depend heavily on the types of resins in the vessel, and can range from just an inch to a foot or more in thickness. It’s also worth noting that a larger freeboard space can enhance the self-cleaning effect, while less freeboard space can enhance water quality.
Resin compatibility
Resin selection is of critical importance for any IX system, including those that leverage UPCORE™ technology. UPCORE™ vessels house an inert resin as well as one or more types of charged cationic or anionic resins, depending upon the application. Thus, there is added complexity, as resin selection must consider compatibility with the constituents of the feed stream and process conditions, as well as compatibility with other resins contained in the IX vessel.
Chemical incompatibility can lead to a number of issues that can compromise resin performance, such as fouling, which occurs when constituents bind to the resin material and block ion exchange sites. Other signs of incompatibility with process conditions include oxidation and thermal degradation, both of which cause damage to the resin material that makes it mechanically unstable and prone to fragmentation. For UPCORE™ systems, such issues may be signaled by compromised performance of self-cleaning capabilities, damage to plant equipment, and/or reduced water quality.
Additionally, improper resin bead sizes may negatively impact system performance. Too large, and the resin may not compact properly during service and regeneration cycles. Too small, and the resins may pass through into the inert bead layer or be lost to the effluent. In most cases, Dow recommends uniform particle size (UPS) resins for optimal performance of the UPCORE™ technology.
To prevent premature resin failure, it is advisable to thoroughly analyze feed streams and process conditions, and select resins that are not only compatible with one another, but that can also withstand stream constituents, temperature, and other factors.
Regeneration strategy
All IX systems require systematic regeneration cycles to recharge spent resins. Systems that leverage UPCORE™ technology offer greater efficiency in terms of chemical and water use, however, improper regeneration strategies can result in issues including excess consumption of water and chemicals.
One of the most important aspects of an effective regeneration strategy is careful management of flow rates. Due to the nature of the UPCORE™ technology, differing flow rates may be utilized during various phases of the regeneration cycle. In the compaction phase of a regeneration cycle, for example, water is directed upward from a bottom inlet at a relative high flow rate in order to dislodge particulates from the bed, and to force the resin beads to compact against the inert layer at the top of the vessel. Water flow rates are typically kept lower during the ensuing phases, which include chemical injection, settling, and rinse phases. This aspect of UPCORE™ technology—the ability to modify flow rates to ensure efficient and complete regeneration of resins—sets it apart from other IX technologies by minimizing the overall consumption of water and regenerant chemicals used.
In addition to flow rates, there are a number of other interrelated factors that will affect the regeneration strategy, including resin bead size, density, freeboard volume, and water temperature, among other characteristics. In all, an optimal regeneration strategy should include carefully considered flow rates, contact times, and regenerant concentrations to ensure that the benefits of the UPCORE™ technology are fully realized.
Can SAMCO help?
SAMCO has over 40 years’ experience in identifying efficient IX resin technologies and regeneration strategies to minimize downtime and maintain consistent product quality. For more information or to get in touch, contact us here to set up a consultation with an engineer or request a quote. We can walk you through the steps for developing the proper solution and realistic cost for your IX treatment system needs.
To learn more about SAMCO’s IX resin solutions, visit our pages on our innovative ion exchange resin technologies and off-site resin regeneration services.
If you want to learn more about ion exchange resins, these other articles might be of interest to you:
- How Much Does It Cost to Buy, Maintain, and Dispose of Ion Exchange Resins?
- Common Problems with Ion Exchange Resins and How to Avoid Them
- What are the Best (and Cheapest) Ways to Dispose of Ion Exchange Resins?
- What is the Difference Between Cation and Anion Exchange Resins?
- What Are the Different Types of Ion Exchange Resins and What Applications Do They Serve?
- What Are the Best Ion Exchange Resin Manufacturing and Supply Companies?
- What Is Ion Exchange Resin and How Does It Work?