What Technologies Usually Make up a Brine Water Treatment System
Although brines are sometimes used in manufacturing (for example, during chlor-alkali processes that uses the electrolysis of sodium chloride to create chlorine and sodium hydroxide), they are also created as an industrial byproduct or waste that can be challenging to treat and dispose of (such as flowback water from fracking natural gas wells). Filtering and concentrating brines often generates other problematic wastes that can be difficult to treat for reuse or cause harm to the environment if improperly discharged or disposed of, so it’s no surprise that brine treatment and disposal regulations have been increasingly prohibitive and difficult for industrial facilities to meet and work around.
If your facility can benefit from more information about properly treating brine waste, one of the questions you might have is “What technologies usually make up a brine waste treatment system?”
This article provides a general overview of what brine wastes are and what technologies are commonly used to treat them, which can vary depending on what contaminants are present and whether the facility is treating the brine for discharge or recycling and/or reusing in its process.
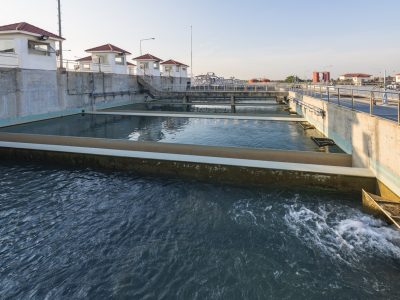
What is brine?
In general, “brine” is any solution with an extremely high concentration of salts, such as sodium chloride, which can occur either naturally (as with seawater, deep-water ocean pools, salt lakes, etc.) or as a byproduct of industry. These byproducts, or “brine waste” streams, are typically highly concentrated salt solutions that, in some cases, contain more than twice the amount of concentrated salts than natural brine solutions.
Brine waste streams can also be highly concentrated with total dissolved solids (TDS), such as waste streams in many chemical manufacturing processes, and they can be some of the most challenging to treat or discharge because their composition and purification requirements are dynamic and complex.
Some examples of brine waste created as a byproduct of industry include:
-
-
- cooling tower and boiler effluent
- reverse osmosis (RO) and ion exchange waste/reject streams
- produced water from extracting oil and natural gas
- chlor-alkali and chemical plant waste
- acid rock and mine drainage
- food preservation and manufacturing waste streams
- desalination waste from potable water creation
- irrigation runoff
-
Brine waste is typically either recycled for use in the facility’s process or treated for disposal, but these processes are rarely straightforward or practical, and can even be costly.
A typical brine treatment system might include:
Membrane filtration
One of the more cost-effective technologies for treating brine waste, membrane filtration is still widely used across various industries. When treating brine, it’s common to see systems that begin with ultrafiltration (UF) and end with reverse osmosis (RO).
When UF is used prior to RO, it effectively removes various contaminants while protecting downstream membranes from premature wear and fouling. UF membranes are available in pore sizes ranging from 0.001 to 0.1 μm, which means UF removes a more comprehensive range of contaminants than some other membranes (such as microfiltration) while leaving behind ions and organic compounds of low molecular weight. UF is suited for removal of very fine particles, including proteins, colloidal silica, and silt.
The stream is then passed through an RO system, which is a membrane technology that uses a semipermeable medium to remove certain ions and particles from a liquid stream that are 0.0001 µm or larger, including salt. This produces a high-quality water stream in addition to a highly concentrated stream of waste, which can be used or discarded, depending on the needs of the facility.
This sequence of membrane treatment is effective for protecting equipment and minimizing chemical costs and system downtime for cleaning and is generally considered a low energy–consuming technology.
Evaporation and crystallization
After brine is concentrated by membrane filtration, thermal processes or evaporation are often used as the next step to dry solids. Excess water is evaporated off, collected, and reused (adding acid at this point will help to neutralize the solution so, when heating it, you can avoid scaling and harming the heat exchangers). Deaeration is often used at this phase, as well, to release dissolved oxygen, carbon dioxide, and other noncondensible gases to further protect equipment from corrosion and other harmful occurrences.
The leftover waste then goes from an evaporator to a crystallizer, which continues to boil off all the water until all the impurities in the water crystallize and are filtered out as a solid. This process is often used in facilities that aim for zero liquid discharge, but it’s generally reserved for only facilities that require it (most likely due to stringent environmental and discharge regulations) as it is considered a costly and high energy–consuming process.
Ion exchange
Ion exchange (IX) systems are used across a variety of industries for water softening, purification, and separation purposes. These systems separate ionic contaminants from solution through a physical-chemical process where undesirable ions are replaced by other ions of the same electrical charge. This reaction occurs in an IX column or vessel where a process or waste stream is passed through a specialized resin that facilitates the exchange of ions.
When contaminant removal needs are highly specific, many times IX is ideal. Chelating resins are the most common type of specialty resin and are often used for brine softening.
Weak acid cation (WAC) exchange resins are also often used to remove cations associated with alkalinity (temporary hardness) and are therefore also ideal for softening brine. Facilities can also use various proprietary resins to separate contaminants, such as metals, from the brine stream to support production and manufacturing of lithium carbonate and lithium hydroxide.
Electrodialysis is also a form of ion exchange that can be used in the brine treatment system. It’s a membrane process that uses positively or negatively charged ions to allow charged particles to flow through a semipermeable membrane and can be used in stages to concentrate the brine. It is often used in conjunction with RO to yield extremely high recovery rates. Combined, these technologies can concentrate a brine stream down to a high salinity while pulling out up to 60–80% of the water.
Other things to consider when treating brine
As mentioned previously, when looking at basic separation for a contaminated brine stream, you will always be left, essentially, with a more purified brine (such as a sodium chloride stream). The cost to treat a brine stream like this can be relatively low and would include treatments such as:
-
-
- membrane filtration
- precipitation
- carbon adsorption of organics
- oil and water separation
-
Using IX, the facility can take out easy-to-remove contaminants, which might leave you with something like a sodium chloride or brine sulfate brine stream, which is a salt stream that doesn’t easily precipitate.
These technologies are relatively low cost compared to removing the salt directly out of the brine (such as with sodium chloride or sodium nitrate). In these instances, it’s very difficult to remove the salts and almost always involve high-pressure membrane systems to concentrate the brines (pulling the water out of the brine).
In situations where membrane filtration won’t be effective, evaporation and crystallization will help remove the water from the brine, but such thermal polishing processes are exponentially more expensive when it comes to purchasing the relative technology in addition to high operational and energy usage costs.
Essentially, by trying to solve one problem your facility can easily create another.
The only true ways to dispose of brine are to reuse it or dilute and slowly release it back into the environment. For example, if you have a very large river near your facility that is available of discharging your treated brine, you can slowly bleed the brine in, dissolving it back into the body of water with a minimal impact to the river. If you have a smaller stream, your facility will not be able to do this; doing so could pose catastrophic harm to the environment, killing off fish and other wildlife in the surrounding areas. In some areas, where permitted, waste brines can be deep-well injected although this option is becoming more restricted.
Facilities can reuse brine, but recycling it will concentrate it more, which would leave you discharging a smaller stream with a higher concentrate of salt and TDS.
As always, it is usually best to discuss any treatment options with a water-treatment professional who is able to analyze your facilities needs, specifically, and help you determine the best treatment options, as they can be highly individual.
Can SAMCO help?
SAMCO has over 40 years’ experience in identifying appropriate brine waste treatment solutions to help lower costs and waste volumes while increasing recycling and reclamation of valuable materials. For more information or to get in touch, contact us here to set up a consultation with an engineer or request a quote. We can walk you through the steps for developing the proper solution and realistic cost for your brine waste treatment system needs.
To learn more about SAMCO’s innovative technologies that we commonly apply for spent brine stream treatment, visit our pages on reverse osmosis and ion exchange resin systems.
Some other brine treatment articles you might also find useful include:
- How Much Does It Cost to Treat Brine for Reuse and/or Disposal?
- In What Ways Can a Facility Reuse Brine Waste?
- What are the Best Brine Waste Treatment System Equipment and Supply Companies?
- Is it Necessary to Treat Brine Waste Before Discharging or Disposal?
- What Is Brine Waste, and How Can It Be Treated for Reuse or Disposal?