How to Perform an Effective Wastewater Treatability Study
Ultrafiltration has been around in concept for over a century, but it has only just come into broad use within the last few decades as advances in the technology have made it more cost-effective. Analysts are expecting that the ultrafiltration market will continue to show strong growth over the next several years, with rising demand by municipal water treatment, refinery, dairy, food and beverage, biopharmaceutical, and hospital facilities driving the growth trend. Here we’ll take a look at what ultrafiltration is, how it works, and dig into some key design variations that contribute to its versatility in serving a range of process separation, water purification, and wastewater treatment applications.
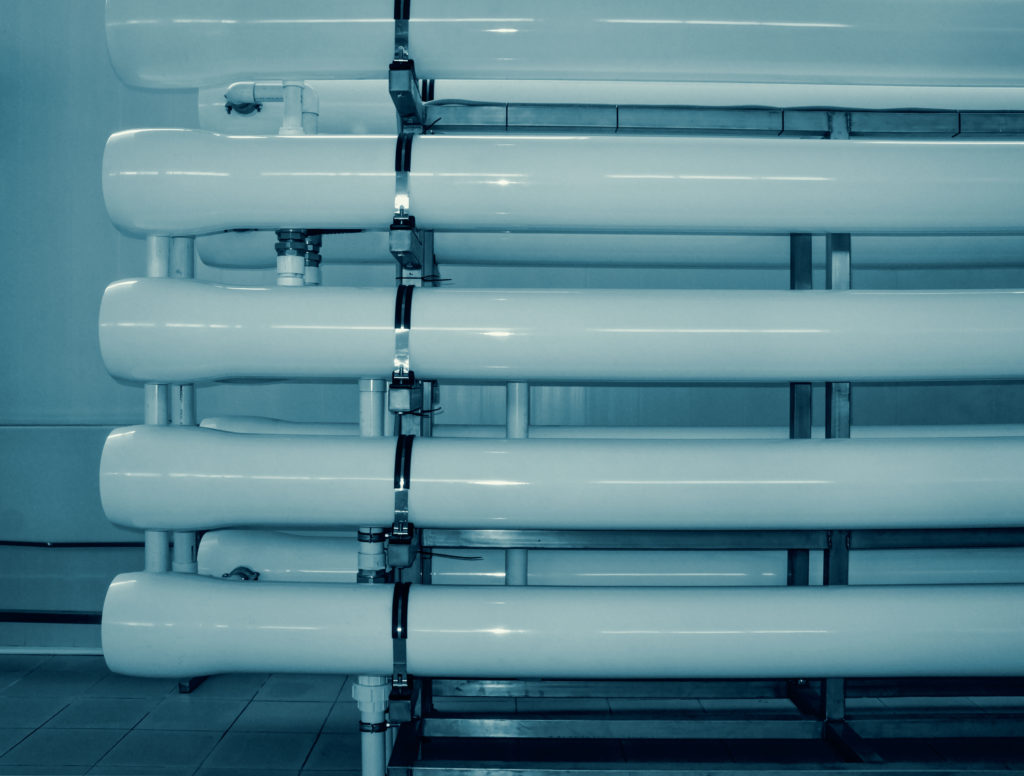
What is ultrafiltration?
By definition, ultrafiltration (UF) is a type of physical separation that uses a membrane with precisely sized openings to filter certain solid particles or large molecules out of a liquid stream. In addition to UF, there are other types of membrane filtration, including microfiltration (MF), nanofiltration (NF), and reverse osmosis (RO), all of which have distinct pore size ranges, and are thus suited for separation of various contaminants based on particle size. With pore sizes ranging from 0.001 to 0.1 µm in size, UF is suited for separation of very fine particles, which can include silica, silt, endotoxins, plastics, proteins, smog, and viruses.
How does ultrafiltration work?
Form a conceptual standpoint, ultrafiltration is a fairly straightforward process that basically consists of passing a liquid stream through a porous membrane. Any particles that are larger than the pores in the UF membrane are unable to pass through, and in this way, UF is said to work based on the principle of size exclusion. Depending upon the type of UF unit used, these larger constituents can become a concentrated liquid stream known as the retentate, or they may collect on the surface of the membrane as a solid known as a filter cake. The liquid portion of the stream, and smaller particles that are able to pass through the UF membrane, are referred to as the filtrate or permeate stream.
Dead-end vs. cross-flow filtration
Fluid dynamics, or the way in which a liquid moves through a water treatment system, are especially important to the design of an ultrafiltration system. There are two main flow pattern configurations for UF systems—dead-end filtration and cross-flow filtration. Ultrafiltration proceeds in fundamentally the same manner in both types, however, there are some key differences between the two that make either approach more or less suitable for certain applications.
Also known as direct flow filtration, dead-end filtration is a type of membrane separation where the feed stream is forced through a porous membrane at a perpendicular angle. Particles that are too large to fit through the membrane pores build up on the surface of the filter in a residue known as a filter cake. As the filter cake layer accumulates, the high concentration of contaminants on the surface of the membrane can result in decreased permeate flux, or in other words, a decline in the flow of the solvent liquid through the membrane. For this reason, dead-end filtration is generally used for batch or semi-continuous flows, allowing the membrane to be cleaned between use cycles to remove filter cake buildup. Dead-end filtration provides a high recovery rate of the feed stream, typically over 95%, and is well suited for streams with a low concentration of particulates, or in applications where a purified filtrate stream is needed.
A different operational design type, cross-flow filtration is a type of membrane separation where the feed stream flows along the surface of the membrane at a parallel angle. Otherwise known as tangential filtration, cross-flow systems produce two liquid streams, including both a purified filtrate stream, and a concentrated retentate stream that is usually recirculated through the UF unit. Cross-flow filtration is typically operated as a continuous process because the constant flow of the feed stream across the surface of the membrane prevents the accumulation of solids on the surface. This characteristic has several implications, including little to no filter cake formation, less frequent cleaning needs, a longer membrane lifespan, and more consistent flux. However, because the retentate is reciculated, cross-flow systems tend to consume more energy, and offer a lower feed stream recovery rate compared to dead-end filtration. As such, cross-flow filtration is best suited for treating feed streams with high concentrations of solids, or for applications where a concentrated retentate solution is needed.
Types of ultrafiltration membranes and their uses
As we’ve said, the separation work of an ultrafiltration unit is done by a component called a membrane. But what exactly is a UF membrane and how does it work? The answer to that question is actually more complicated than you’d think, since commercial UF membrane elements come in a variety of shapes, sizes, and materials, all of which are factors that play a role in how ultrafiltration works within a particular unit. Below, we’ve summarized the main types of UF membrane elements and how they work:
Tubular UF membranes
Tubular modules consist of an outer housing, typically made of PVC or steel, with a bundle of smaller tube-shaped UF membrane elements running the length of the interior. Each membrane tube element is typically only about 5-15 mm in diameter. As the feed stream passes through the unit, the liquid solvent permeates through the walls of the interior membrane elements in an outward direction toward the outer shell. During cleaning cycles, the system can be run in reverse, with the backwash solution flowing from the outer channel inward through the membrane elements. The relatively large diameter of tubular membrane elements provide easy cleaning and blockage resistance, and as a result, feed streams are less apt to require pre-treatment. Most membranes are fabricated from polymeric materials, however, tubular modules can also be made out of ceramic material, typically when needed to handle extremes in temperature and pH. The main downsides of tubular UF elements include lower packing density and lower permeability, which can translate to longer process times.
Common applications for tubular ultrafiltration membranes include wastewater treatment and recycling, especially for membrane bioreactors (MBRs), or wastewaters with high oil content, as well as treatment of streams with moderate to high concentrations of solids.
Hollow fiber modules
Hollow fiber modules are similar in design and principle to tubular modules, however, the interior UF membrane elements are much finer, at only about 0.2 to 3 mm in diameter. Because of their fineness, the hollow fiber elements offer greater flexibility than tubular units, and the greatest packing density comparative to other membrane elements. They are also easy to clean with backwash cycles, can tolerate higher levels of TDS and TSS, and can be operated at very low feed pressure. The downside is that hollow fibers are more prone to blockages, are susceptible to breakage at pressures above 30 psi, and can be costly to replace.
Common applications for hollow fiber ultrafiltration modules include MBR wastewater treatment, pretreatment ahead of RO or ultrapure water treatment, juice and beverage processing, drinking water treatment, raw water treatment, and industrial process water treatment.
Spiral-wound modules
Spiral-wound modules are constructed from layers of membrane material and perforated screen that are essentially rolled up around a perforated tube core. Most are designed in an outside-in configuration, meaning that the stream moves through the layers of membrane from the outer layers toward the center, forming a permeate stream that is collected within the perforated tube. Comparative to hollow fiber and tubular membranes, spiral-wound membranes offer good throughput due to their higher surface area. They are also affordable, easy to clean, and can be operated at low to moderate feed pressures. Due to the small spaces between the layers of membrane material, they can, however, be prone to blockages when used to treat streams with high suspended solids.
Common applications for spiral wound ultrafiltration modules include protein isolation and concentration, gelatin purification, juice concentration, sulfate removal, acid and caustic recycling, paint recovery, dye desalting and concentration, endotoxin and pyrogen removal, oil/water separation, and industrial wastewater treatment.
Plate and frame modules
Plate and frame modules use sheet-like membranes that are attached to porous membrane supports known as frames. A plate and frame unit houses many of these flat membrane plates, which are layered together with feed flow spacers, and sealed with end plates at each end. The feed stream flows through the unit, and the permeate that passes through the membrane plates is channeled into a collection manifold. Plate and frame units can be designed in either a dead-end or cross-flow configuration. In cross-flow types, there will generally be separate outlets for a concentrated retentate stream, and the purified permeate stream. In dead-end types, solid deposits form into a filter cake between membrane plates. Depending upon the system design, plate and frame modules may allow membranes to be rotated or selectively replaced, which can extend the life of the membranes, and some units provide the ability to scale up capacity by adding additional plates. They are also resistant to fouling, and able to handle streams with high concentrations of solids. The downsides to plate and frame elements include lower packing density and efficiency compared to other types of membrane elements, and higher cost.
Common applications for plate and frame ultrafiltration modules include cosmetics production, MBR wastewater treatment, wastewater reuse, and treatment of food and beverage streams with high solids concentration.
Can SAMCO help?
SAMCO has over 40 years’ experience custom-designing and manufacturing ulrafiltration systems for a range of industries and solutions, so please feel free to reach out to us with your questions.
For more information or to get in touch, contact us here to set up a consultation with an engineer or request a quote. We can walk you through the steps for developing the proper solution and realistic cost for your ultrafiltration system needs.
You can also check out our blog to learn more about other industrial filtration and process separation technologies. Some articles that might be of interest include:
- Microfiltration vs Ultrafiltration Processes: What is the Difference?
- What is Reverse Osmosis and How Is It Used For Industrial Applications?
- Case Study: UF Wastewater Treatment Solution for a Steel Mill
- What Is Membrane Fouling and How Can You Avoid It?
- What Are the Different Types of Membrane Fouling and What Causes Them?