Five Ways Your Industrial Facility Can Reduce Wastewater Discharge Volume
As populations rise and continue to tax waterways alongside the effects of climate change, increasing water-access fees and ever-tightening effluent regulations can all seem to create a losing battle for industrial facilities that are looking to keep ahead of the water-shortage curve. If your facility, however, does a little preparation now in order to reduce wastewater volume and mitigate these future burdens, chances are your business will be able to better adapt to a water-stressed world.
Even though wastewater reduction solutions and industrial water conservation methods largely vary from industry to industry, there are some things all industrial facilities can do to ensure conserving water and reducing discharge waste is part of their short- and long-term strategies.
In this article, we’ll be looking at how industrial facilities are curbing wastewater discharge costs by reducing the volume of wastewater they have to discard—and, in turn, saving on sewer connection and transport fees, which can be steep depending on the level of contaminants present in your waste.
Many of the solutions below are similar to some information we’ve shared in a previous industrial water conservation post. This article, however, will focus on what facilities can do to reduce the volume of wastewater specifically, not just water usage overall. Many of the methods are throughout the entire production and manufacturing process.
Here are the ways your industrial facility can reduce its wastewater discharge volume.
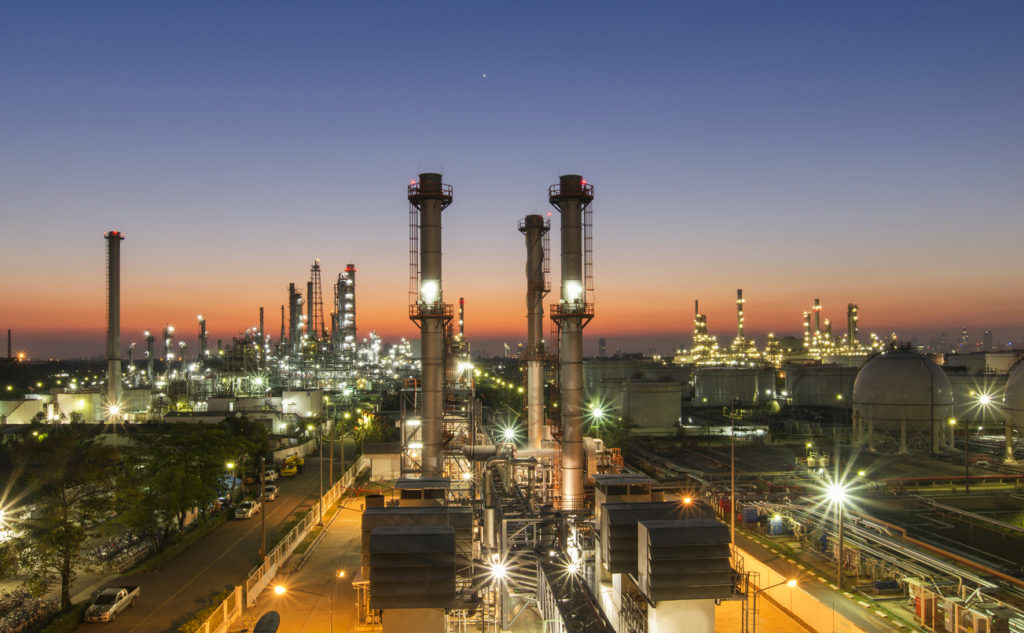
Identify problematic runoff and connection issues
One of the many ways industrial facilities can reduce its wastewater volume is by identifying any point of the process where groundwater, rainwater, or fractured pipes might be leaking fresh water or untreated process waster into your effluent streams. What might seem an unlikely place to find and reduce excess wastewater, it’s fairly common for extra water from these sources to seep directly into your effluent stream.
It’s also common for facilities to find that process piping has been routed inefficiently or that valves and connections are fractured or poorly sealed, which can all pose an issue when a facility is looking to tighten up its wastewater volume. Complete a thorough water usage audit that takes into consideration how much water is used at various parts of your production process and continue to set goals to tighten them. Also keep in mind that some of your process and wastewater will evaporate. Each small fix can add up to big savings over time.
Modify equipment and install water-saving devices like meters
It’s important to understand your facility will be using water in more places than just in its production processes. In addition to these other water uses (think high-efficiency toilets, drinking water units, and sinks), ask yourself if it is possible to lessen the water flow, replace water-intensive equipment with other technologies, or use water from one part of the process in another. Sometimes there are portions of a production process that can use a lesser quality of water.
Also metering devices can help to reduce wastewater volume by ensuring levels are continually audited. Some can be used as automated shutoff mechanisms or overuse alarms, and they can go a long way in helping assess needed makeup water for cooling towers and boilers. Track the usage and adjust based on the device’s finding.
Reuse and recycle water at various parts of your operation
Implementing water recycling and reuse as part of your process can greatly reduce the volume of effluent your plant will have to discard. This approach can come with a high investment upfront, but the long-term savings are often worth the cost. This is becoming especially true, too, with the growing call for facilities to be more responsible with their water usage, which is, as mentioned earlier in the article, taking the form of costly fees and stringent regulations. For this reason, many facilities are setting goals to make sure they’re not taking more water than they are able to (cleanly) replace. A thorough analysis can help determine which recycling measures will pay off for you.
Shift to waterless processes when able
There are countless technological advancements that are replacing water-intensive processes with those that little water or even no water at all. Look into some of these solutions for your own facility.
When it comes to treating your process water and wastewater for specific instances where you can’t discharge water at all, your facility might benefit from zero liquid discharge, a range of technologies that work to recover all fluid waste, leaving the facility with a solid cake of waste that is easier to discard.
Incorporate biological wastewater treatment technology
If your industrial or municipal facility generates organic-laden wastes, biological wastewater treatment might be an appropriate choice for your facility. These systems can be efficient and economical technologies for breaking down and removing organic contaminants from wastes such as those produced in the food and beverage, chemical manufacturing, oil and gas, and municipal industries. Bonus for facilities able to use this method: it’s a natural process that produces a useful biogas that can be used as energy for other parts of the facility’s process.
Can SAMCO help?
SAMCO has over 40 years’ experience in the design and manufacture of custom water treatment systems for a range of industries and applications, so please feel free to reach out to us with your questions.
Get in touch with us here to set up a consultation with an engineer or request a quote. We can walk you through solutions that fit your water reduction and reuse needs and maximize your return on investment.
Head on over to our blog to learn more about available water treatment technologies to help reduce industrial water consumption. Some articles that might be of specific interest to you include: