Five Ways Your Industrial Facility Can Conserve Water and Plan Ahead for Shortages
Environmental and water scarcity issues are expected to impact industrial facilities increasingly in the coming years, driving up both sourcing and discharge costs. To conserve water and prepare for these future challenges, many industrial facilities are beginning to look at water conservation strategies.
In this post, we’ll explore “Five Ways Your Industrial Facility Can Conserve Water and Plan Ahead for Shortages.” These approaches range from small to large in terms of initial investment and expected return but will give you a starting point for considering what water conservation strategies are right for your facility.
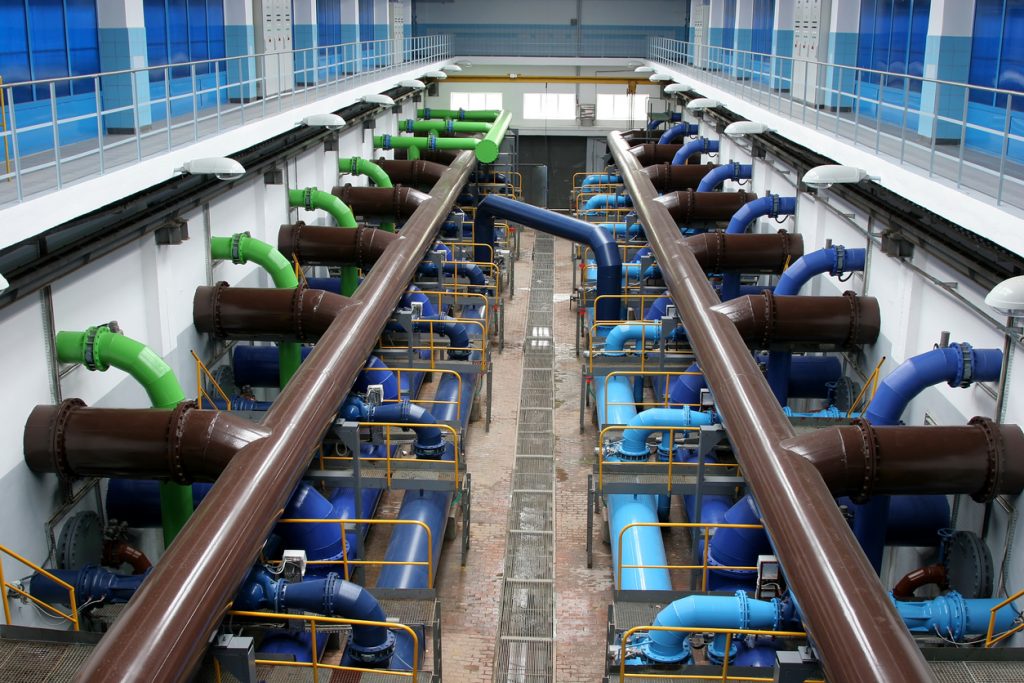
Performing routine maintenance
Leaking equipment and pipes result in a great deal of preventable water waste, so a great starting point for improving water efficiency is to check existing equipment and peripherals for condition and performance. Conduct a thorough check for leaks and repair any that are discovered, then implement a scheduled maintenance plan to proactively find and repair any leaks that may surface later. It may also be helpful to periodically review and adjust equipment and processes to minimize water use. This can include checking with equipment or supply manufacturers to ensure that cleaning agents, IX resins, and equipment are all optimal for your process, for example, or checking minimum flow rates and adjusting downward if appropriate.
Upgrading existing equipment and peripherals
Increasing concern over water availability and cost has spurred development of water-efficient technologies that can be implemented across a wide variety of industrial processes. Reducing water use can be as simple as swapping out small components, such as hoses and sprayers, or as involved as replacing elements of your process trains with newer, more efficient technologies. An example of a popular water-saving upgrade is the use of dry-in-place technologies to replace water-driven cleaning and rinse processes, especially in automotive manufacturing and machining industries. Additional water-saving equipment upgrade approaches are offered below:
Replacing small components
Where possible, use high-pressure, low volume hoses, nozzles, and spray heads for cleaning and rinsing units, or wherever appropriate. Automatic shutoff nozzles can also help to reduce water waste, especially for manual hoses and sprayers used for cleaning purposes. These types of changes typically entail minimal investment and deliver immediate cost savings.
Upgrading existing equipment
Various models or types of equipment are often available to suit the same separation or treatment needs. Whether replacing old or worn equipment, or proactively upgrading functional systems, facilities can save moderate to substantial quantities of both water and energy by choosing high-efficiency models where possible. Selecting a High Efficiency Reverse Osmosis (HERO) system as opposed to a traditional RO unit is just one example among many. In some cases, upgrading to a water-saving model may come at a higher initial cost, but the investment often pays for itself by conserving water or other resources.
Sometimes, it may be in an industrial facility’s best interest to go a little deeper than simply swapping in a newer, high-efficiency model of its existing equipment. In some cases, a facility’s needs may be better served by adopting an additional process step (such as adding a pre-cleaning cycle to reduce water waste in later cleaning, rinse, or rework cycles), or by replacing equipment with different technologies (such as substituting membrane filtration for conventional separation).
Reusing water
For some industrial applications, it is possible to conserve water by reusing it for two or more cycles without pretreatment. Reusing wash or process water may require moderate upfront investment in tanks and pumps, but typically provides a return on investment within the first year after implementation. Implementing water reuse practices can help to cut water sourcing costs, as well as wastewater treatment and discharge costs. Many facilities use contact cooling water that is dumped directly to drain. This water can be captured and pumped back into the facility for alternate uses.
Cleaning baths
Cleaning baths are often a great opportunity for reusing water. To do so effectively, a facility will likely need to monitor pH, conductivity, or other attributes of the bath and wastewater, and possibly set up schedules for replacing the bath and/or maintaining it, generally through the addition of cleaning agents or supplementary water.
Boiler condensate
Condensate collects in steam lines through normal boiler operation. Rather than discharge condensate as wastewater, it is generally more cost efficient to route the condensate back to the boiler. Boiler condensate is typically low in TDS and therefore does not require additional treatment for reuse, meaning that recycling the condensate can be as simple as installing new piping and pumps. In addition to minimizing water use and discharge costs, reusing boiler condensate can also save energy since it retains its high temperature upon return to the boiler, meaning that far less energy is required to heat it.
Other sources of water for reuse
There are a wide variety of industrial applications where water can be reused for multiple cycles. Reuse scenarios are commonly employed for each of the following:
-
-
- Boiler makeup water
- Rinse water from wash, final rinse, and bottle and can lines
- Cleaning water (both equipment and facilities)
- Backwash or cleaning cycle water from filtration units
- Cooling tower blowdown water
- Air conditioner condensate water
-
Pretreating and recycling water
Another way to cut water use is to adopt a wastewater treatment strategy to recycle waste or effluent streams for other applications, such as cooling towers, cleaning, and irrigation, or other uses. Of the approaches mentioned here, a combined wastewater treatment and recycling approach often requires the highest upfront investment but can yield substantial cost savings in the long term.
Common technologies used in a wastewater treatment train include:
-
-
- Filtration: Consisting of media and/or membrane filtration units, these technologies are used to remove particulate solids from waste streams.
- Dissolved air flotation (DAF): Used to remove suspended solids from liquid streams.
- Biological treatment: Comprises a variety of technologies used to break down and/or remove biodegradable solids.
- Ion exchange (IX): Includes a variety of resin technologies used to selectively remove dissolved ionic contaminants.
- Distillation: A heat-driven separation process used to separate liquid components of a mixture, often deployed for recovery of industrial solvents.
- Absorption / adsorption: Utilizes specialized resins for removal of a wide variety of solute contaminant, particularly for solvents, or for applications where high purity is needed.
-
Since industrial waste streams typically contain a variety of contaminants, wastewater treatment trains typically combine a few of these technologies to ensure that the treated stream is suitable for intended applications or discharge. Some systems, such as zero liquid discharge (ZLD), are capable of minimizing water waste right down to nothing at all.
Auditing water use
Water use audits are important for understanding how water is used at your facility so that you can clearly identify opportunities for reducing consumption. While some facilities conduct water use audits internally, hiring a water treatment professional can provide deeper insight into your water usage due to greater access to industrial benchmarking data and knowledge of appropriate treatment technologies. Additionally, since water use audits quantify water usage and waste, they provide valuable data that can be leveraged for initiatives aimed at conserving water through behavioral or cultural changes.
Can SAMCO help?
SAMCO has over 40 years’ experience custom-designing and manufacturing efficient water treatment systems for a range of industries and applications, so please feel free to reach out to us with your questions.
For more information or to get in touch, contact us here to set up a consultation with an engineer or request a quote. We can walk you through options for industrial water conservation solutions that fit your needs and maximize your return on investment.
Head on over to our blog to learn more about available water treatment technologies to help reduce industrial water consumption and prepare for water shortages. Some articles that might be of specific interest to you include: