Electrolysis and Green Hydrogen: Impacts and Outlook
As the world looks for more sustainable ways to meet its growing energy demand, green hydrogen is almost always part of the conversation. But what exactly is green hydrogen, and what role does it play in our energy economy? Here, we’ll take a look at how hydrogen is currently used and produced, and how these things might change in coming decades.
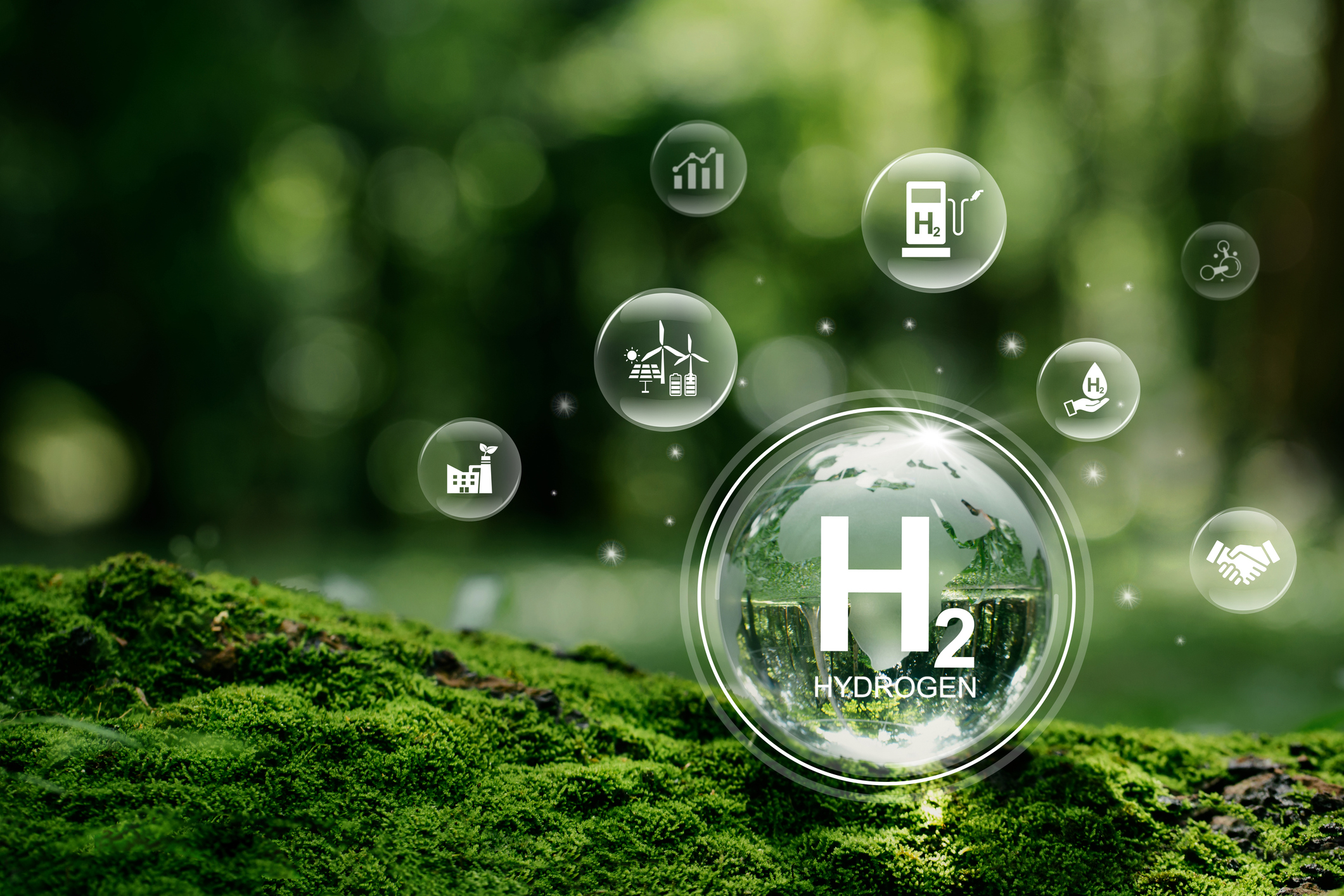
What is hydrogen and why is it important?
Hydrogen as green energy
Like fossil fuels, hydrogen is able to store and release large amounts of energy. But what makes it unique is that hydrogen combustion releases only water vapor when burned in the presence of oxygen. This stands in contrast to fossil fuels, which release greenhouse gases and other pollutants when burned. For these reasons, hydrogen is an excellent zero-carbon alternative to fossil fuels, although there are some challenges that have so far kept hydrogen from more widespread use as an energy source. For one, hydrogen fuel must be stored at extremely low temperatures and high pressure. Because of the need to maintain these conditions, storage tanks tend to be very large and heavy in proportion to the energy capacity they contain. They are also prone to leaks and risks of explosion. Additionally, while it is true that hydrogen burns cleanly in the presence of pure oxygen, combustion in the presence of nitrogen (as is the case in normal atmospheric air) can result in emission of nitrogen oxides, which are toxic pollutants. Lastly, even while hydrogen combustion is clean, many of the current technologies used to produce hydrogen are themselves carbon-intensive. Still, there is hope that these challenges can be solved with further research and development. Recent advancements in hydrogen fuel cells and production technologies are already helping to make hydrogen safer and more accessible to produce, store, and use. In all, the hydrogen economy is projected to see continued growth in coming years, especially with continued investment in carbon reduction initiatives, and growing adoption of hydrogen energy across various industrial sectors.
How is hydrogen produced?
As an element, hydrogen (H) is abundant on Earth, but because of its reactivity, it is mostly bound up in chemical compounds, including water as well as various organics. Industrial production of molecular hydrogen works by breaking down these types of hydrogen-containing compounds, with some production technologies being much more sustainable than others.
Several production methods have evolved to meet the world’s increasing demand for hydrogen. At this time, the most common method for producing hydrogen is steam reformation. While this process is relatively cheap, it has significant environmental costs, including the use of non-renewable natural gas as a raw material, greenhouse gas emissions, and consumption of electricity for heating and other purposes. Hydrogen produced through steam reformation is often referred to as “gray hydrogen.” It is sometimes also called “blue hydrogen” if producers have taken steps to recapture carbon dioxide emissions, although most carbon recapture technologies have not yet proven very effective.
Another process, known as water electrolysis, is a promising new production technique that is steadily gaining ground on steam reformation.
Take a look at the different kinds of hydrogen production and it’s ultimate waste:
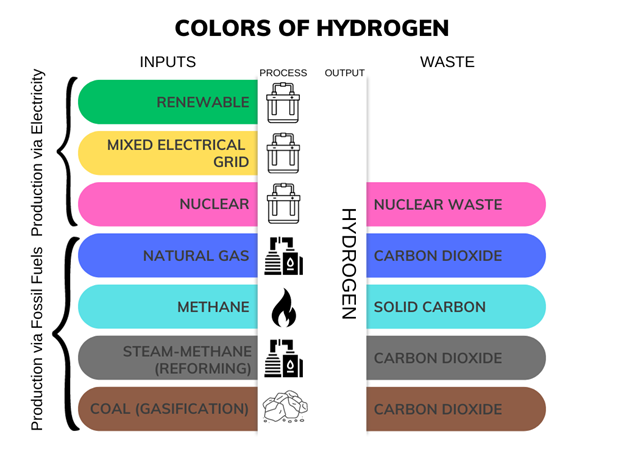
What is water electrolysis?
Water electrolysis, is a process used to produce hydrogen gas from water. Also known as water splitting, electrolysis basically consists of using an electrical current to split water into its component parts—oxygen and hydrogen. The reaction takes place in an electrolytic cell, which is a unit that has two electrodes (an anode and a cathode) and an electrolyte solution. The design of the electrolysis equipment may vary, but the basic reaction is the same: by applying an electrical current to the cell, water reacts with one of the electrodes. As it does so, it releases charged ions that transfer along a circuit to ultimately release oxygen and hydrogen gases from the opposing electrodes. The electrolytic production of hydrogen is itself a green process that does not directly consume or emit carbon. Its carbon footprint depends entirely upon the source of electricity used to supply a current to the electrolytic cell. When the electricity source is derived from a renewable, zero-carbon resource, like solar, wind or hydropower, the produced hydrogen is known as “green hydrogen.”
How much water is needed for electrolytic hydrogen production?
While water electrolysis may be light on carbon emissions, it does require a lot of water. For every 1 kg of hydrogen produced through electrolysis, 9 kg of water is consumed. Moreover, the actual total is higher when you figure in water used for purification, cooling, or other processes. This is because water used in electrolysis must be of sufficient quality to avoid problems with heat and electrical conductivity, as well as deposition of sediment on the electrodes. To prevent these issues, water will typically require pre-treatment by demineralization, deionization, or distillation to ensure adequate removal of dissolved constituents before it is fed to the electrolytic cell. Due to the high water costs of the process, some are skeptical of electrolytic hydrogen production as a viable green energy solution. Scientists and engineers on the other side of the debate are, however, more optimistic about the future of electrolytic hydrogen production. For example, opinion pieces published by the American Chemical Society and the non-profit organization RMI both argue that total water consumption is actually lower for electrolysis than it is for fossil fuel production when all the water used for drilling, extraction, and processing is taken into account. For these experts, electrolytic hydrogen production is a promising strategy for meeting green energy goals, even if the process could still use some improvement from an efficiency standpoint. Time will tell what role green hydrogen will ultimately play in our energy mix, but it is likely that research and development will continue in this arena for years to come.
How can SAMCO help?
- Water recycling and reuse systems: Strategies for a smaller carbon footprint
- Why Your Industrial Facility Should Plan for Water Shortages Sooner Rather Than Later
- Industry and Water Shortages: Is Your Facility Ready?
- Can Your Facility Save Money by Reducing Its Water Consumption?
- Five Ways Your Industrial Facility Can Conserve Water and Plan Ahead for Shortages