Common Problems Removing Silica from Industrial Water and How to Avoid Them
Silica removal and reduction technologies are an important component of many raw water treatment and process water treatment trains. No matter what technology is used, it can pay to look out for some common problems removing silica from industrial water and how to avoid them.
In this article, we’ll look at how issues such as silica fouling, scaling, and leakage can crop up, as well as some solutions to help prevent or mitigate their effects.
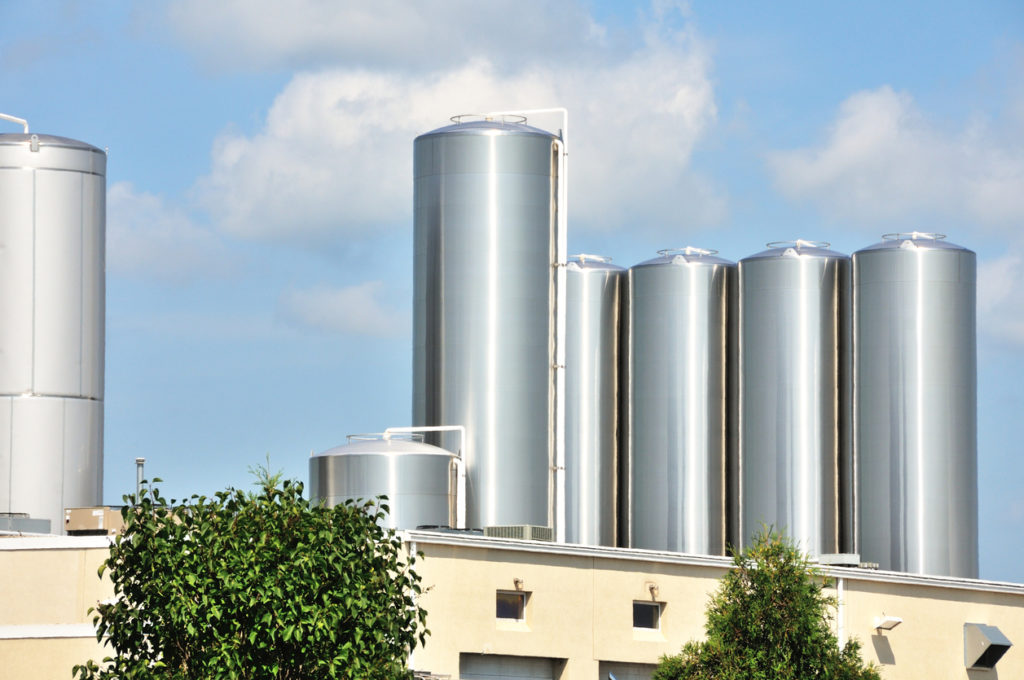
Seasonal variations in silica content
The problem:
Ground, surface, and well waters can contain variable concentrations of silica depending on seasonal changes in the environment. A problem known as silica leakage occurs when silica levels rise beyond the capacity of a facility’s raw water treatment system and break through into the effluent. Excess silica in the effluent can cause a number of issues, such as inadequate process water quality, wastewater treatment challenges, as well as potential damage to downstream equipment due to scaling and fouling.
The solution:
Avoiding problems due to variable silica levels comes down to smart planning. When designing a raw water treatment system, be sure that you have a full understanding of how your source or feed water may fluctuate throughout the year. Chemical feeders and sludge handling components used in lime softening systems should be of adequate capacity to handle silica removal even when feed stream concentrations are at their highest.
IX resin fouling and silica leakage
The problem:
Silica is less reactive than most other ions, making it tricky to deploy selective treatment approaches like ion exchange (IX). Removal of ionic silica (present as silicic acid) is most often accomplished by a strong base anion (SBA) exchanger. Indeed, SBA exchange is effective for reactive silica removal, although facilities can run into problems such as IX resin fouling and silica leakage if the process isn’t carefully managed.
Maintaining proper pH is a major factor in effectiveness of IX silica removal. During a service cycle, the freshly regenerated SBA resin has a high enough pH to ensure that silica remains ionized, and able to bind with hydroxide exchange sites on the resin. As the cycle proceeds, however, the resin is exhausted, the pH drops, and the silica detaches from the resin, flowing out in the effluent in increasing concentrations in what is known as leakage. Additionally, the lower pH of the IX system encourages polymerization of silica molecules. Polymerized silica forms a gel that is messy to clean, and can foul IX resins by remaining attached to exchange sites, compromising performance in future cycles.
The solution:
IX can be a delicate process to manage, especially for selective silica removal. When deployed properly, however, IX offers the most complete removal of ionic silica comparative to other treatment technologies.
During the normal course of use, an IX system will need to be maintained through a resin regeneration step. Improper application of caustics during regeneration cycles is a primary cause of silica scaling on IX resins and equipment. To prevent resin fouling and leakage, facilities should carefully monitor IX treatment cycles, and follow manufacturer’s recommendations to properly regenerate IX resins.
Additionally, softening can be used as a pre-treatment ahead of IX silica removal. Doing so ensures that calcium and/or magnesium that is also present in the stream won’t precipitate during a cycle, and interfere with the IX silica removal process.
Membrane fouling
The problem:
Certain membrane technologies are effective for colloidal and dissolved silica removal, including both nanofiltration and reverse osmosis. Under the right conditions, however, silica has a tendency to adsorb to surfaces, including RO and filtration membranes. Membrane fouling is a situation where silica particles accumulate in the pores or on the surface of membranes, ultimately obstructing the normal flow of water through the membrane. There are a number of consequences of membrane fouling, including reduced efficiency of the separation process, as well as premature membrane failure.
The solution:
It is almost always more cost-effective to properly maintain membrane filtration units than to remediate fouling that has already occurred. Silica’s reactivity is dependent upon a complex interplay of factors such as pH, temperature, membrane material, and what other constituents are present in the stream. These factors all influence the likelihood that silica will polymerize and/or form scale deposits. Therefore, fouling prevention may entail any of various steps, such as pretreating the stream, applying antiscalant chemicals, switching to a different membrane material, adjusting pH or temperature, as well as other approaches. Therefore, it is important to thoroughly evaluate the process to ensure that silica removal goals are met while also optimizing the performance of any membrane filtration technologies.
Can SAMCO help?
SAMCO has over 40 years’ experience in identifying appropriate silica removal technologies to help lower costs and improve system efficiency. For more information or to get in touch, contact us here to set up a consultation with an engineer or request a quote. We can walk you through the steps for developing the proper solution and realistic cost for your particular silica removal needs, or your larger raw water treatment needs.
To learn more about SAMCO’s innovative solutions, visit our page on raw water treatment technologies here.
If you want to learn more about silica removal, these other articles might be of interest to you:
- Do You Need a Raw Water Treatment System for Your Plant?
- How to Choose the Best Raw Water Treatment System for Your Plant
- Five Common Problems with Raw Water Treatment and How to Avoid Them
- Five Common Problems with Raw Water and How You Can Treat Them
- Treated vs. Untreated Raw Water for Your Plant
- 12 of the Best Raw Water Treatment Equipment Supply and Technology Companies
- How Much Does a Raw Water Treatment System Cost? (Pricing, Factors, Etc.)