Case Study: UF Wastewater Treatment Solution for a Steel Mill
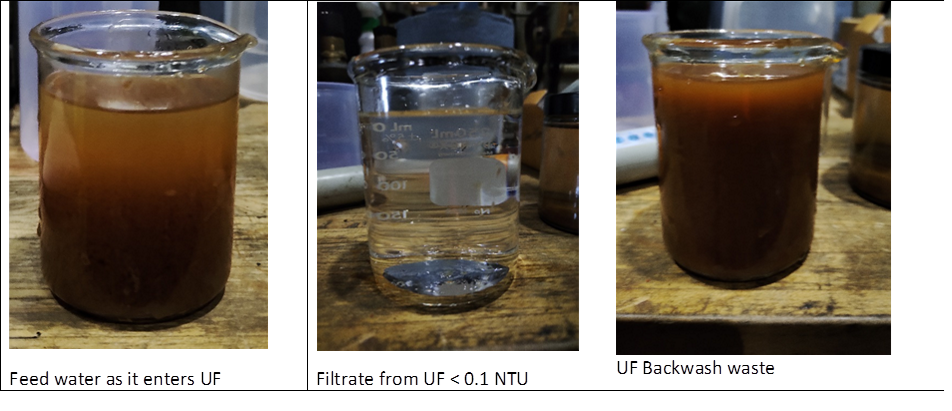
Membrane technologies deliver expanded capacity, reuse-ready effluent in an innovative wastewater treatment application for hot-formed steel manufacturing
Background
When a North American steel mill decided to expand its production capacity, it knew an expansion of its wastewater treatment plant was in order as well. But as the steel mill took stock of its existing challenges and limitations—like limited space, stringent environmental regulations, and high source water costs at its location—it decided to go beyond a simple expansion of its existing systems, and take the opportunity to build new efficiencies into its wastewater treatment processes.
Previously, the steel mill relied on a conventional wastewater treatment train consisting of pre-treatment with oil skimming and sand filtration, followed by chemical treatment for pH adjustment and precipitation, and rapid sand filtration before ultimately discharging its wastewater to a neighboring river. While this approach kept the steel mill’s wastewater discharges in compliance with National Pollutant Discharge Elimination System (NPDES) permit limits, the complex treatment train required labor-intensive monitoring and management. Additionally, the existing WWTP had a large footprint, and high operational costs due to its significant chemical consumption. Correcting these types of inefficiencies became major objectives for the steel mill’s WWTP expansion project.
Following a competitive bidding process, the steel mill awarded the WWTP expansion project to SAMCO based on a forward-thinking design that was both more cost-effective, and delivered much improved effluent quality.
Challenges
The main goal of the project was to expand capacity to allow for future growth, but in order to do so, the solution needed to overcome a few challenges. These included:
- Limited space. The WWTP is housed on the interior of the facility’s grounds, surrounded by buildings and machinery. As such, its footprint could not be easily enlarged to expand overall treatment capacity.
- High levels of metals and phosphates. The steel mill uses large amounts of water for cooling in its production of hot-formed steel. During casting, rolling, and other activities, its streams pick up a complex blend of oils, metals, phosphates, and other contaminants that are subject to strict limits and monitoring under the facility’s NPDES permit.
- Inconsistent stream. The steel mill produces wastewater streams that vary both in volume and makeup, factors that can trigger system upsets in traditional physical-chemical wastewater treatment technologies.
While fairly common to steelmakers, this combination of constraints added complexity to the WWTP expansion project.
Solution
After gathering solution proposals from a number of wastewater treatment system providers, the steel mill selected a design by SAMCO. Featuring an innovative use of ultrafiltration (UF) technology for a steel mill application, SAMCO’s design improves upon the facility’s former wastewater treatment capabilities by producing higher-quality effluent that leaves the facility with plenty of room for expansion while still operating well within regulatory limits on its wastewater discharges.
To achieve this, SAMCO provided full-cycle services to design and deliver a turnkey wastewater treatment system to meet project goals. SAMCO consulted closely with the facility to identify the client’s needs and opportunities for process improvements before developing an appropriate solution design. To ensure that the system would run smoothly from day one, SAMCO also worked with the steel mill to conduct a series of onsite pilot studies to evaluate system efficacy and fine-tune system settings. SAMCO then fabricated and delivered the full-scale system, and provided installation and startup support services. Remarking on this close partnership, the plant’s wastewater treatment manager asserted: “I can’t say enough about SAMCO—their dedication to making sure this ran correctly. They had definitely done their homework on what we were up against and what we were trying to do, and it made my job significantly easier.”
The resulting WWTP design leverages a clarifier for pre-treatment followed by ultrafiltration (UF) membrane separation for secondary treatment. All told, the new WWTP is easily able to handle the steel mill’s capacity of 27 million gallons per month while keeping operations costs at a minimum.
Front-end system for economical primary treatment
To maximize system performance and minimize operations and maintenance costs, SAMCO’s wastewater treatment system design leverages a primary treatment step consisting of a front-end reactor and pre-screening. The system allows for removal of particulate solids down to 150 micron (µm) in size, and is resistant to system upsets for consistent performance despite variability in stream makeup and volume. The design produces an effluent with a relatively low contaminant concentration that ensures efficient operation of downstream systems.
Ultrafiltration for high-quality effluent
SAMCO’s solution design features an innovative application of ultrafiltration (UF) for secondary treatment of the steel mill’s wastewater. The UF unit uses direct flow filtration, resulting in a high-quality effluent stream that far exceeds the plant’s minimum quality standards for direct discharge, and is now clean enough for reuse applications. To maximize membrane life and overall cost-effectiveness, the system leverages upstream pretreatment as well as an automated backwash, flux recovery, and an enhanced chemical cleaning system, as well as PLC controls for automation of monitoring and maintenance activities.
Results
SAMCO delivered on the steel mill’s objectives with a solution design that expanded treatment capacity, cut water use, and kept costs under control, as detailed below:
Expanded capacity
The delivered solution doubled the treatment capacity of the former WWTP, accommodating flows of 400 gallons per minute (GPM) to 1000 GPM at peak. Despite this significant increase in capacity, the new system takes up only a third of the space of the previous system, leaving the facility with plenty of room for further expansion.
Reduced water use
The new system results in a significantly cleaner effluent than that produced by the old system, with the facility’s treated wastewater now comparable in quality to city water. This is evident in samples taken before and after treatment:
Feed water (mg/L) |
Percent removal |
|
Aluminum (Al) |
20 – 50 |
99.84 % |
Iron (Fe) |
20 – 50 |
99.90 % |
Manganese (Mn) |
0.1 – 2 |
95.00 % |
Phosphorus (P) |
1 – 3 |
76.00% |
As such, the steel mill now has the ability to reuse its treated wastewater. Given that source water costs in the region sit at $5 per 1000 gallons—well above the national average—the steel mill stands to generate substantial cost savings just from water reuse capabilities alone. Additionally, by improving the quality of its treated wastewater, the steel mill can stay well within the limits of relevant environmental regulations, even as it scales up production.
Cost-effectiveness
A key objective for the project was to introduce cost savings wherever possible. SAMCO achieved this with a solution that offered both a competitive capital cost compared to other bids received, as well as minimal operating expenses (OPEX) afforded by its smart design.
These types of process improvements were made possible through intensive discovery, which allowed SAMCO to identify specific opportunities for building greater operational efficiencies into the facility’s wastewater treatment process. In leveraging membrane separation technologies to replace the steel mill’s conventional treatment process, SAMCO was able to deliver a solution that eliminated the facility’s need for hazardous chemicals like chlorine, bisulfide, and other caustics. As a result, the facility was able to realize a significant cost savings by minimizing its chemical consumption.
Another way in which SAMCO’s solution design kept OPEX to a minimum is by incorporating automated maintenance components that not only reduce the burden on operators, but also keeps system components in excellent working condition. The UF unit is equipped with clean-in-place (CIP) and system monitoring technologies that simplify maintenance routines to maximize the usable life of the membrane elements so that fewer replacements are needed over time. “We’re 9 months in to running this system and I’m still seeing 100% recovery rates on all of my trains,” said the steel mill’s wastewater treatment manager, “That’s just a testament to the setup of the equipment from SAMCO.” As a result of the performance they have seen so far, the steel mill now expects the membranes to last for seven to ten years before they will need replacement—well beyond than the initial five-year projection used for budgeting.
Conclusion
In all, the higher quality effluent opens up new avenues for making more efficient use of water resources within the plant, ensuring that the steel mill will have ample flexibility to adapt to changes in production volumes, wastewater discharge regulations, and source water costs that may arise in years ahead. Or, in the words of the plant’s wastewater treatment manager, “I feel without a doubt that the SAMCO system far surpassed what we needed to see. Our process has become better than anticipated.”
How can SAMCO help?
SAMCO has over 40 years’ experience custom-designing and manufacturing water treatment systems designed to conserve water and energy resources, so please feel free to reach out to us with your questions.
For more information or to get in touch, contact us here to set up a consultation with an engineer or request a quote. We can walk you through the steps for developing the proper solution and realistic cost for optimizing water use at your electrical generation facility.
Head on over to our blog to learn more about industrial filtration and process separation technology. Some articles that might be of specific interest to you include: