Brine Treatment Processes for Reuse or Disposal
Brine treatment processes can be used to improve the suitability of a brine for a given application, make a spent brine stream safe for disposal, or even serve both of these purposes at once. No matter whether a brine stream is destined for reuse or disposal, a well-designed brine treatment process will not only help a facility stay in compliance with stringent environmental regulations, but can also generate cost benefits by minimizing waste.
This article offers a general overview of what brines are and how they are used in industry, how brine treatment works, and the pros and cons of brine reuse and discharge methods so you can better understand the available options for dealing with these often-problematic streams.
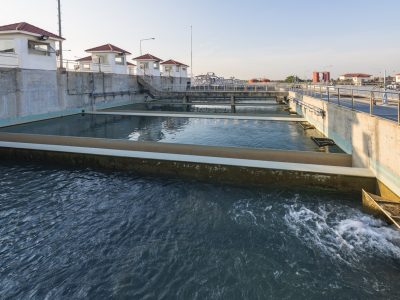
What is brine waste?
By definition, a brine is any solution with a high concentration of salt dissolved in water, such as solutions made with sodium chloride, calcium chloride, potassium bromide, or other salts. Such saline solutions can occur naturally (e.g. seawater, deep-water ocean pools, salt lakes, etc.), or they can result from industrial activity. Brines produced as a byproduct of industry are known as brine waste streams, and they typically contain much higher concentrations of salt than natural brines like seawater.
All industrial brines share in their high salinity (or salt concentration), but streams might vary significantly from one to the next in terms of other constituents present. This is because various materials can end up in the brine stream in the course of normal operations, such as suspended solids and particles, anti-scaling agents, heavy metals, microorganisms, organic material, oil, and grease. Industrial brine streams can also vary significantly in terms of volume, pH, and temperature, all of which can add complexity to a facility’s need with regard to brine waste management.
Common industrial uses of brine
Brines are used or produced by a wide variety of industrial activities. Sometimes, brines are used as a process stream (e.g. chlor-alkali chemical production), while at other times, they are a waste product that results from an industrial process (e.g. desalination waste brine). Some of the more common examples of industrial brine streams include the following:
- cooling tower and boiler effluent
- reverse osmosis (RO) reject streams
- ion exchange (IX) waste or spent regenerant streams
- produced water from oil and natural gas extraction
- spent brines from chlor-alkali and chemical production
- fracking and acid mine drainage
- waste streams from food and beverage production
- desalination brines as a byproduct of potable water creation
- irrigation runoff
Industrial brines such as these may require some form of process purification or wastewater treatment before they are ultimately discharged or recycled according to a facility’s chosen brine waste management strategy.
What is brine management?
Brine management is the strategy that an industrial facility uses to deal with the brine waste streams that it produces. There are two main ways in which a facility may manage its brine wastes: either by disposal, or treatment for reuse applications. To do so, a facility will usually employ some form of brine waste treatment to separate out contaminants and/or adjust the salinity of a brine effluent stream before it is either discharged or recycled for another use. Because brines are used in such a wide variety of industrial applications, waste brine treatment strategies may draw on a number of different technologies and processes. Below, we break down a general overview of the various brine waste treatment and disposal methods available and what they might mean for your facility.
What is brine discharge?
Brine discharge is the disposal of brine waste streams, such as by discharging them to a sewer system or to a nearby body of water. Brine waste disposal can be a very economical means of managing brine wastes, although industrial facilities need to be conscious of wastewater compliance issues when doing so.
Is it necessary to treat before disposal of brine?
Brine effluent will typically require some form of treatment prior to disposal, but not always. Brine waste treatment needs may range from minimal to intensive depending upon the chosen methods of disposal, and other factors, including the stream chemistry, contaminant content, and other attributes (e.g. volume, temperature, etc.). Facilities who discharge directly to a body of water may need to treat brine wastes in order to comply with applicable environmental regulations. In the US, this will usually require compliance with a National Pollutant Discharge Elimination System (NPDES) permit as well as any additional local discharge limits. Facilities that discharge to a centralized treatment facility may need to treat brine wastes in order to comply with any volume limitations and/or water quality standards set by the receiving facility.
At minimum, most discharge regulations will require a reduction in the amount of sodium, total suspended solids, and contaminants present in a stream. Simply diluting brine waste prior to discharge may be a practical solution for some facilities, but this method is not always permitted. As such, when considering dilution as part of your brine waste discharge plan, be sure to fully understand local discharge requirements to ensure that you won’t incur costly fines for non-compliance, or other penalties, like revocation of discharge permits, environmental remediation mandates, or other legal actions.
It is always best to verify discharge, monitoring, and reporting requirements at your specific location, then implement an appropriate brine treatment strategy to ensure that your facility is able to keep up with any permit requirements or other discharge regulations.
Common brine discharge methods
Brine water treatment technologies can vary significantly depending on how the brine waste stream will ultimately be discharged. Typical methods of brine disposal include:
- Sewer discharge: Discharging brine waste to a publicly owned treatment works (POTW), such as a municipal sewer, is generally a low-cost disposal option, although access to a POTW often depends on location. POTWs set their own limits on discharge volumes and acceptable stream constituents based on their capacity and the types of contaminants they are able to handle, so discharge standards may vary significantly from one facility to the next. In some cases, industrial facilities are able to achieve acceptable dilution of brine effluent as it is combined with all the other streams entering the POTW, while in other cases, industrial facilities may need to treat or dilute their own brine streams prior to discharge in order to meet the POTW’s quality standards.
- Surface water discharge: Brines can sometimes be discharged to lakes, rivers, or other bodies of surface water. Surface water discharge can be a relatively low-cost solution, however, facilities must typically comply with stringent regulatory guidelines when doing so, which can mean adopting treatment strategies to remove certain contaminants or adjust the salinity, sometimes by dilution. Depending on the volume and the size of the receiving body of water, it is possible that a brine waste stream may be satisfactorily diluted by all the other streams entering the receiving body. If permitted by regulatory agencies, such a disposal arrangement may mean little or no brine waste treatment is necessary.
- Desalination waste disposal: Desalination processes result in a highly concentrated brine waste stream that can be disposed of through any of the methods listed here, but is most commonly dealt with through direct discharge to the ocean. Unfortunately, the extremely high salt content of desalination brine has been shown to disrupt ocean ecosystems, a fact that has caught the attention of researchers, the public, and regulators. For this reason, industrial facilities are increasingly adopting strategies to lessen the environmental impact, including various dilution strategies, like mixing brine waste with seawater, or spreading out discharge outlets or using high-pressure sprayers to better spread the desalination waste over a larger area.
- Evaporation: Evaporation ponds collect spent brine and leverage solar energy to remove water content through heat exposure. They require minimal investment in terms of operations, maintenance, energy, and compliance, but can take up a large footprint. Newer technologies, such as wind-aided intensification of evaporation (WAIV), can reduce the footprint needed for a traditional evaporation pond and speed up the evaporation process. Brine treatment and/or specialized solid waste management may also be necessary if toxic contaminants are present or if there is a large volume of waste brine.
- Deep well injection: Deep well injection is typically reserved for applications requiring disposal of high volume brine waste streams, such as those produced by hydraulic fracturing operations. This controversial disposal method involves pumping spent brine into porous rock formations found deep underground, and is not permitted in all states. Deep well injection requires brine waste treatment for total suspended solids (TSS), oils, and greases, so as to prevent blockages in receiving wells. Additionally, deep well injection entails substantial costs associated with drilling, permitting, and monitoring the well, making it an impractical disposal option except for certain high-volume, high-salinity waste streams.
- Zero liquid discharge (ZLD): In some locations, costs for liquid waste disposal can run quite high. If this is the case, it may be worth considering ZLD systems, which remove all liquid constituents as a means of cutting discharge costs. While ZLD systems have relatively high capital and energy costs, they can more than make up for it by minimizing liquid waste disposal costs, increasing yields, and facilitating reclamation of valuable materials.
Whichever method your facility uses to treat its brine waste for discharge, make sure it is done so in compliance with any relevant POTW limitations and/or National Pollutant Discharge Elimination System permits.
What is brine reuse?
An alternative option to disposal is recycling or reusing brine streams. While they can entail higher costs for treatment, brine reuse strategies can yield bottom-line cost benefits by reducing wastewater discharge volumes and associated costs, or helping to increase production volumes without exceeding discharge limitations. In some cases, industrial facilities can also realize net cost savings by supplementing fresh water demand with waste brine, especially in regions where access to source water is costly or unreliable. Some industrial plants are also finding external recycling opportunities as well, through mutually beneficial arrangements that allow them to cut wastewater discharge costs by selling or giving away their waste brines to fellow manufacturers, farmers, municipalities or others. Examples of this can range from relatively common use of brines for irrigation of salt-tolerant land and vegetation, to more novel applications, such as the use of cheese brine for road deicing.
Is it necessary to treat brine wastes prior to reuse?
Ultimately, the feasibility and cost of brine reuse and recycling can depend on a number of factors, including facility location, brine constituents, and stream volume. Commissioning a treatability study is one way to get a better understanding of the salinity levels, as well as metals, total dissolved solids (TDS), and other contaminants present in your waste brine so you can better determine whether brine waste treatment for recycling and reuse is a cost-effective option.
Common brine recycling and reuse applications
With appropriate treatment, waste brines can be used for a number of different applications. Below, we’ve summarized a few of the more typical brine reuse and recycling strategies:
- Acid and caustic production: Caustic soda (sodium hydroxide) and chlorine are used extensively across industry. Production of these chemicals involves electrolysis of a sodium chloride brine solution, an energy-intensive process that uses large volumes of brine. To improve overall efficiency, many acid and caustic producers have implemented brine electrolysis recovery strategies, allowing for reuse of brine waste through multiple electrolysis cycles. Similarly, mining and metals industry brines can be reclaimed for acid and caustic production. In this way, facilities are able to reduce their brine waste volumes, while simultaneously producing chlor-alkali products that can be used internally or sold.
- Softener brine recycling: Brines resulting from both ion exchange (IX) softeners and reverse osmosis (RO) systems can be treated and reused for additional treatment cycles. Doing so can reduce overall water and salt consumption. Brine waste reclamation setups capture a portion of used brine, treat it (if necessary), and return it to the brine tank during IX resin regeneration. While brine recycling can be a great way to improve softener efficiency, it is generally viable only for softeners that use a high salt dose and that have a relatively high sodium chloride concentration following an active cycle. Additionally, brine reuse can result in an even more concentrated effluent that can be more difficult or costly to discharge.
- Irrigation and agriculture: In some cases, waste brine streams can be applied to land for irrigation and agricultural purposes. Generally speaking, waste brines used for agriculture must have relatively low TDS and be free of toxic constituents, such as heavy metals. In some regions, reuse strategies have included application of waste brines to salt-tolerant crops. Alternatively, some facilities have been able to leverage waste brines to produce liquid fertilizer, especially for brine waste streams that contain a mix of sodium and hardness. In this case, the brine is typically treated through an IX process to selectively remove sodium, while retaining hardness that is valuable to plant development.
- Deicing and dust control: In an effort to cut discharge costs, some facilities have begun offering waste brines to cities and municipalities for controlling ice, snow, and dust on roads. Different regions or municipalities may be more or less willing to accept waste brines for road treatment due to concerns over hazardous constituents, or the potential for harm to the local environment or water supply. Local governments have been known to accept waste brines from food and beverage production, as well as mining and gas extraction, and other industries. The level of treatment needed prior to use for road treatment applications is variable depending on stream constituents, but in some cases, municipalities may go beyond mere acceptance, and may even compensate industrial facilities for their waste brines.
- Recovery and sale of solid salts: Solid salts can be recovered from brines through zero liquid discharge (ZLD) systems. These typically consist of a brine concentration step, followed by crystallization and solids dewatering. While ZLD technologies can be costly, they are effective in eliminating wastewater discharge costs, and can be leveraged to produce solid salts. Brine byproduct salts can be used or sold for a variety of industrial applications, such as detergent manufacturing, dyeing, chemical production, curing, water treatment, and deicing, among other uses.
- Cooling: While commonly used by power plants, oil refineries, chemical plants, and other facilities, cooling towers consume large quantities of water. With proper treatment, recycled brine can be a great solution for reducing water use in cooling and thermal equipment. Recycling brine for this purpose will generally demand some form of cooling tower water treatment to minimize corrosion and scaling, which can include reduction of salt content, chlorides, phosphates, sulfates, and oxidizing bacteria. Recycling for cooling applications is limited by the salt concentration and other contaminates, as it inhibits heat transfer and may cause foaming.
- Desalination brine reuse: Desalination processes result in large volumes of extremely salty waste brines that can be difficult or costly to discharge responsibly. With the increasing numbers of desalination plants worldwide, however, new technology for desalination brine reuse is emerging. In addition to some limited agricultural uses, desalination brines can be recycled for use in producing caustic soda (sodium hydroxide) and hydrochloric acid, both of which have uses for cleaning and pre-treatment applications within the desalination facility. This is essentially the same as how any waste brines are used for caustic production, but at this time, desalination brine reuse is not as widely implemented as it is in other industries.
There are many other reuse applications beyond those listed here. Whatever brine recycling strategy might be appropriate to your facility, keep in mind that brine leftover from production often accumulates contaminants along the way, such as silica, heavy metals, hardness, organic compounds, sulfates, nitrates, phosphates, and suspended solids, any of which can cause problems for downstream processes or equipment if left uncontrolled. Additionally, varying salt concentrations in the brine stream will also determine how the temperature, pressure, and other threshold limitations will need to be adjusted during production, so facilities that use brine as part of their process continuously monitor their brine streams to maintain adequate quality. For this reason, it’s extremely important to have your water treatment specialist evaluate what the brine is being used for in addition to where and how it is being recycled and/or discharged to ensure its composition remains appropriate for the reuse process at hand.
What water treatment technologies are used for brine?
The type of technology that goes into a brine treatment system will vary depending upon the application at hand. Here, we’ve identified some of the more common technologies used for treatment of brine streams:
Pre-treatment technologies
Brine waste streams can be some of the most challenging to treat or discharge because their composition and purification requirements can be rather dynamic and complex. As such, brine waste is sometimes pretreated with coagulants, polymers, additives, and pH adjustment to settle out many of the larger contaminants, including metals, sulfates, and other suspended solids that can foul membranes and cells down the production line.
Ion exchange
Ion exchange (IX) systems are used across a variety of industries for water softening, purification, and specialty separation purposes. IX is a physical-chemical process that is able to selectively remove dissolved contaminants from solution, making it an effective solution for precision separation needs.
IX works by using specialized resins to target specific contaminants, and effectively pull them out of a liquid stream by forces of electromagnetic attraction. There are many types of IX resins, but the most common one used in brine softening applications are specialty chelating resins. Weak acid cation (WAC) exchange resins are also commonly used to remove cations associated with alkalinity or temporary hardness, and are therefore useful for brine softening applications. There are also many proprietary resins on the market for very specialized contaminant removal applications.
For example, say a chlor-alkali plant wishes to reuse its brine stream. However, during normal operations, the brine stream is contaminated with metals like iron, vanadium, or manganese, which can foul downstream equipment, causing unscheduled plant downtime and other delays. To make the brine suitable for reuse, the plant may treat the brine with specialty chelating resins that target the contaminant metals for removal without being exhausted by sodium, thereby removing the unwanted contaminants while preserving the salt concentration in the brine solution.
Membrane filtration
Brine filtration systems are one of the more cost-effective technologies for treating brine waste streams. Membrane filtration technologies are widely used across various industries, and when treating brine, it’s common for ultrafiltration (UF) to be used ahead of reverse osmosis (RO). Doing so allows UF to remove various contaminants in order to protect downstream RO membranes from premature wear and fouling. UF membranes are available in pore sizes ranging from 0.001 to 0.1 μm, which means UF removes a more comprehensive range of contaminants than some other membranes (such as microfiltration), and is suitable for removal of very fine particles, including proteins, colloidal silica, and silt.
Following UF, a brine stream is usually passed through an RO system, which is a membrane technology that uses a semipermeable medium to remove certain ions and particles from a liquid stream that are 0.0001 µm or larger, including salt. This produces a high-quality water stream in addition to a highly concentrated waste stream, which can be used or discarded depending on the needs of the facility. This sequence of membrane treatment is effective for protecting equipment and minimizing chemical costs and system downtime for cleaning, and is generally considered a low energy–consuming technology. Where material recovery is a priority, such as in lithium carbonate or lithium hydroxide production, a brine treatment train with IX followed by high-pressure membrane filtration can be an excellent solution. In this use case, the IX serves to remove unwanted contaminants, while the membrane unit concentrates the purified brine solution to optimize recovery of valuable materials.
A related technology, electrodialysis is a hybrid form of treatment that leverages aspects of IX and membrane filtration. Electrodialysis uses charged ions to separate out targeted contaminants, but it does so by allowing charged particles to flow through a semipermeable membrane. Electrodialysis can be used in stages to concentrate brine streams and reduce liquid stream volumes, and it is often used in conjunction with RO to yield extremely high recovery rates. Combined, these technologies can concentrate a brine stream down to a high salinity while pulling out up to 60–80% of the water.
Evaporation and crystallization
For some brine treatment applications, it may be desirable to minimize liquid wastes. In these cases, a facility may incorporate evaporation and crystallization as part of its brine treatment train. These technologies are used to separate out water from other stream constituents, resulting in a more concentrated brine solution, and/or solid wastes that can be disposed of in a landfill.
Evaporation can be done through either a thermal process or under vacuum. Thermal evaporation may take the form of large evaporation ponds that leverage solar energy, or vessels that require application of heat to evaporate off water content from the brine. Vacuum evaporation also works on the same principle, however by evaporating the effluent under vacuum, the boiling point is reduced, thereby saving energy. In some applications, facilities will choose to acidify the brine stream prior to evaporation as to avoid scaling and damage to heat exchangers as the brine is heated. Facilities may also use deaeration at this phase to release dissolved oxygen, carbon dioxide, and other gases to further protect equipment from corrosion and other damage. Following evaporation, the concentrated brine stream may then be routed to a crystallizer, which continues to boil off all the water until all the impurities in the water crystallize and are filtered out as solid wastes.
Evaporation and crystallization are usually quite costly, both in terms of capital outlay, and operations, as they consume large amounts of energy. Because of the costs involved, evaporation and crystallization are generally used only by facilities who must employ a zero liquid discharge (ZLD) strategy to comply with stringent environmental and discharge regulations.
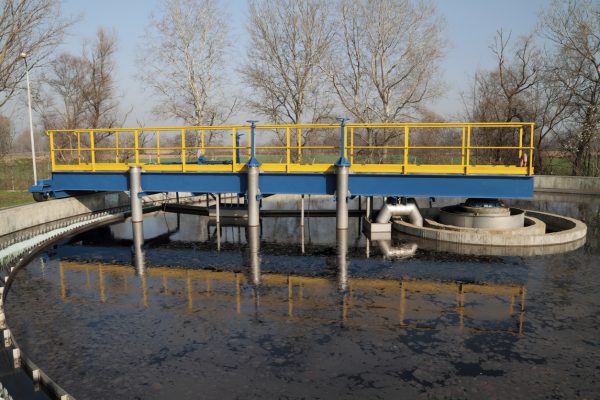
How much do brine water treatment systems cost?
Costs for brine water treatment systems can vary significantly from one application to the next, but in general, high stream volumes, complex brine chemistry, and stringent purity specifications will all drive the cost of a brine treatment system upward. Here, we’ve offered some ballpark figures for costs associated with some common brine treatment setups.
At the lower end are basic separation systems. These systems are designed to remove certain targeted contaminants only, resulting in a purified brine stream suitable for reuse or recycling. Basic separation technologies for brine reuse applications include membrane separation, precipitation, carbon adsorption (for removal of organics), oil and water separation, metals precipitation, and ion exchange polishing. Rough costs for a 100 GPM basic separation system would run somewhere between $750,000 and $2,500,000, depending on which technologies are used.
For facilities needing to reduce the salinity of their brines, both ion exchange and high pressure membranes can be good solutions. Of these, ion exchange is generally more affordable, as a 100 GPM ion exchange system for brine treatment would likely run around $1 to $1.5 million in capital costs, although it may not be an ideal choice for salinity reduction application. High-pressure membrane systems, while more costly, are generally more effective where significant reductions in salinity are needed or where salt streams don’t precipitate easily.
In applications where the objective is to minimize liquid waste streams, thermal polishing may be required in addition to other treatment technologies. Thermal polishing processes, including evaporation and crystallization, will increase capital and operating costs exponentially. For example, in order to achieve zero-liquid discharge, a facility might use a multi-step brine treatment train with basic oil-water separation or adsorption, RO concentration to create a salt stream, and crystallization unit to remove water content. For a 100 GPM capacity system, costs for front-end pretreatment and RO concentration could be $1 to $2 million, while a crystallization system might be another $10 to $20 million in capital costs. Additionally, evaporation and crystallization processes also have high operations costs, as they tend to be energy-intensive.
While a brine water treatment plant can entail significant investment, it can well be worth it if it yields cost savings in other areas—such as by cutting source water costs or reducing discharge costs. In some cases, facilities are even able to use their treated brines or brine treatment byproducts as a revenue stream by selling them to other manufacturers.
How can SAMCO help?
SAMCO has over 40 years’ experience in identifying appropriate brine waste treatment solutions to help lower costs and waste volumes while increasing recycling and reclamation of valuable materials. For more information or to get in touch, contact us here to set up a consultation with an engineer or request a quote. We can walk you through the steps for developing the proper solution and realistic cost for your brine waste treatment system needs.
To learn more about SAMCO’s innovative technologies that we commonly apply for spent brine stream treatment, head over to our blog articles on reverse osmosis and ion exchange resin systems.