Ion Exchange vs. Membrane Filtration for Removing Silica from Industrial Process Water: Which Is Better?
As an industrial facility draws in water for its processes, a host of undesirable contaminants that need to be removed will come in along with it. One of the most difficult-to-treat contaminants is also one of the most abundant: silica. Removing silica, which is the dioxide of silicon (SiO2), can be difficult; is found in many raw water sources in different concentrations and forms—mostly dissolved, suspended, or colloidal. Silica is notorious for having complex chemistry (it has four covalent bonding sites, which means the number of possible molecules is large), and even slight variations in the water dynamics can change the way it is able to be filtered or precipitated out.
Removing silica from your feed water is an important part of your raw water treatment process, especially if you are using this water for high-heat or high-pressure applications, such as for boiler feed water. Silica and similar contaminants will quickly foul and harden on your equipment, reducing its service life—so in order to adequately protect your assets, you will always need to treat the water at least to some degree.
In this article, we outline the difference between ion exchange and membrane filtration for removing silica from your industrial process water so you can determine which course of action might be best for your facility.
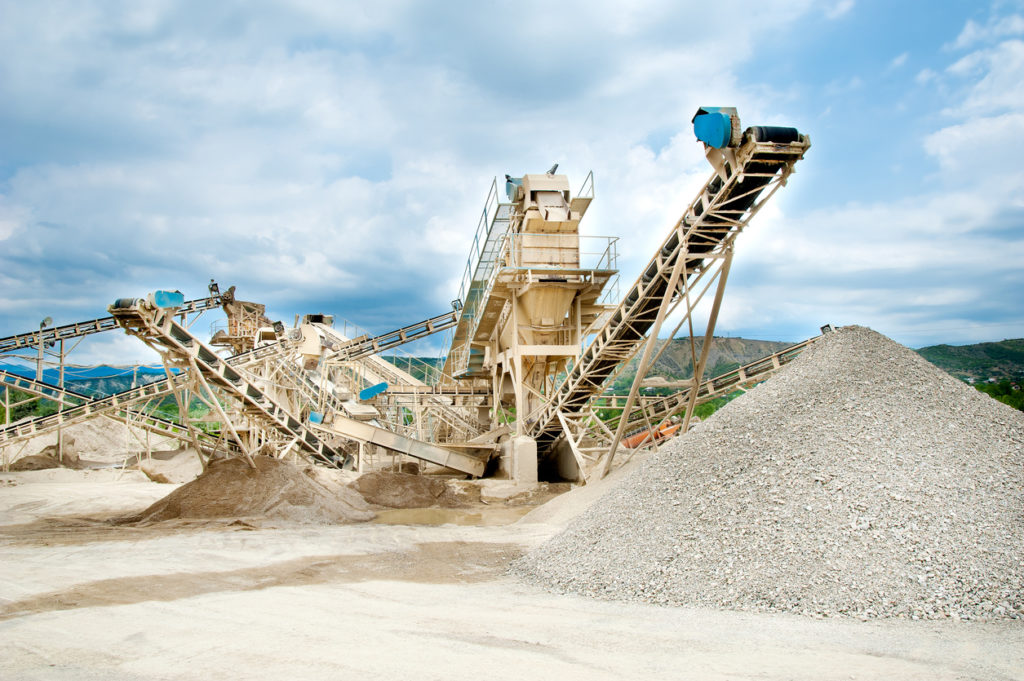
Silica removal with ion exchange
Ion exchange (IX) is a process where a stream is passed through a resin substrate that facilitates removal of ionic contaminants and replaces them with similarly charged particles. IX for silica removal can be a delicate process to manage. When used appropriately, however, IX offers the most complete removal of ionic silica comparative to other treatment technologies. Keep in mind that is IX is the best for your process and there is a large concentration of silica in the feedwater, your ion exchanger needs to be bigger because you have to be careful how much silica you load onto the ion exchanger and prevent fouling the resins.
During the normal course of use, an IX system will need to be maintained through a resin regeneration step. Improper application of caustics during regeneration cycles is a primary cause of silica scaling on IX resins and equipment. To prevent resin fouling and leakage, facilities should carefully monitor IX treatment cycles and follow manufacturers’ recommendations to properly regenerate IX resins.
Additionally, softening can be used as a pre-treatment ahead of IX silica removal. Doing so ensures that calcium and/or magnesium that is also present in the stream won’t precipitate during a cycle and interfere with the IX silica removal process
Silica removal with membrane filtration
When it comes to membrane filtration and higher loads of silica, you just have to make sure that your membranes are flowing freely and not clogging—you will have to clean them more often. Concentration is extremely important when it comes to using membranes for treating silica. If the right parameters aren’t set and care isn’t taken to minimize fouling, it can be difficult to clean your membranes and you’ll need to change them out more often.
If you get too high a silica concentration, you have to go to a precipitation step, and you will typically need to use chemicals and a change in pH to clump everything together and create a floc. In many cases, you will need to use lime softening, and that will, in addition to removing lime and alkalinity, take silica out with it.
Sometimes with these steps you can run into issues, especially if the process requires a change in temperature, as is the case with hot lime softening. This change in temperature affects the value solubility of calcium carbonate, which will also affect your treatment of silica. Most facilities will try to avoid this, if possible, because of the energy costs for heating the water.
You might have to look at upfront precipitation before you can even think about membranes. And even then, you have to be careful because when precipitating, you create a situation where you’ve made the solubility of a compound its minimum. Let’s say you’ve changed the temperature, or you’ve added a certain chemical such that it’s going to go from a dissolved ion to something that’s going to precipitate as a solid. What’s left will be an equilibrium and a situation where the solution is at the right concentration to make a solid, and as you remove water with an RO, you’ll see more solid waste.
Some facilities that need to get extremely low levels of silica could use RO followed by a mixed-bed polisher. Coming out of RO, you’re generally going to see low silica levels to begin with, but if you need to get very pure water, then you have to have the ion exchange on the back end of the RO to polish it up.
Which is better for your process?
As with any challenge your facility seeks to solve, the right solution often depends on the circumstances and what you’re trying to accomplish. The same is true with silica removal, in part because water sources and the level and form of silica vary so much, and also because, as we mentioned in the introduction to this article, silica exists in natural water sources in a number of different forms, such as dissolved material or ion or polymerized (very large molecules) and colloidal form (which is more of a particle than a molecule).
The form your silica takes is typically the driving factor of choosing between ion exchange and membrane filtration; and the concentration will dictate to what degree. For example, if you have colloidal silica, ion exchange might not the best choice because an ion exchanger removes ionic material from the water, not suspended solids. Using RO or ultrafiltration (UF), on the other hand, will remove suspended solids, but silica can also foul your membranes quickly if you’re not using them correctly. When using membrane filtration to remove silica, you can only process a certain incoming concentration before it starts to coat the membrane surfaces.
While this is an extremely simplified answer to a complex question, if you’re looking to get rid of dissolved or reactive silica, ion exchange is probably the best choice. If you have colloidal or polymerized silica, then you’re probably having to use a membrane process.
Can SAMCO help?
SAMCO has over 40 years’ experience in identifying appropriate silica removal technologies to help lower costs and improve system efficiency. For more information or to get in touch, contact us here to set up a consultation with an engineer or request a quote. We can walk you through the steps for developing the proper solution and realistic cost for your particular silica removal needs, or your larger raw water treatment needs.
To learn more about SAMCO’s innovative solutions, visit our page on raw water treatment technologies here.
If you want to learn more about silica removal, these other articles might be of interest to you:
- Do You Need a Raw Water Treatment System for Your Plant?
- How to Choose the Best Raw Water Treatment System for Your Plant
- Five Common Problems with Raw Water Treatment and How to Avoid Them
- Five Common Problems with Raw Water and How You Can Treat Them
- Treated vs. Untreated Raw Water for Your Plant
- 12 of the Best Raw Water Treatment Equipment Supply and Technology Companies
- How Much Does a Raw Water Treatment System Cost? (Pricing, Factors, Etc.)