Reducing and Reusing Water in the Steel Manufacturing Industry
Steelmaking on an industrial scale dates back well over 100 years. Throughout its history, the steel industry has generated products that not only meet a variety of consumer needs but also play a critical role in manufacturing, construction, and transportation industries, among others. Whether produced from iron ore or recycled from scrap, steel production is a resource-intensive process that requires large volumes of water for various cooling and process applications. To ensure long-term sustainability, steel plants are increasingly looking at treatment strategies to improve efficiency in terms of water and energy consumption.
In this article, we’ll take a look at how and why plants are “reducing and reusing water in the steel manufacturing industry,” and explore some considerations for facilities looking to develop an effective water resource optimization plan.
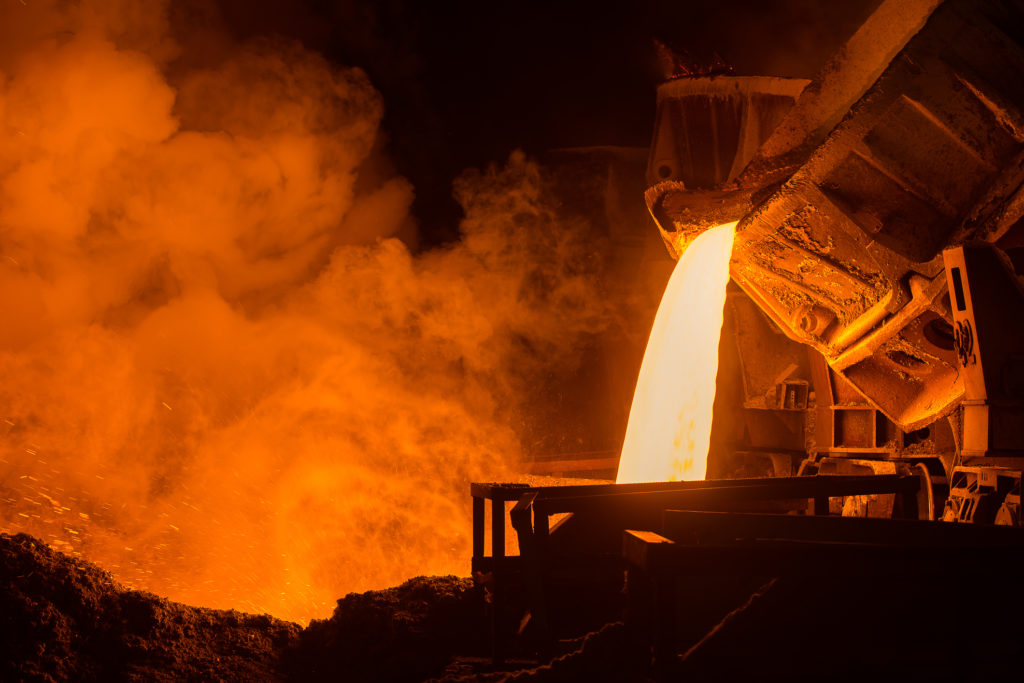
Why is water reduction and reuse important for steel plants?
Over the past fifty years, the steel industry has seen some significant changes, including fluctuations in growth, a shift toward scrap recycling, wider geographic distribution of production facilities, and increased adoption of water management strategies. In many ways, these changes are interrelated, as facilities have had to look for ways to sustainably meet the world’s increasing demand for steel.
While large quantities of water are used in steel production, relatively little water is consumed. In fact, for many facilities, less than 10% of the water drawn into the facility is consumed by production processes, with losses mostly attributable to evaporation during cooling. Therefore, water reuse is important for steel plants because it allows them to potentially recover upwards of 90% of the water they source. Water management strategies help steel plants to recover, reuse, and/or recycle water, which can in turn generate significant cost savings by minimizing the facility’s demand for source water and by reducing discharge volumes.
What are some strategies for reducing water use?
Reducing water use starts with understanding the major uses of water in steel plants. Facilities use water in ways that both directly and indirectly support production, some of which lend themselves more or less readily to water use reduction efforts. Below, we have summarized the major types of water usage within steel plants and highlighted opportunities for reduction and reuse:
Cooling water
Cooling water refers to streams that are used to dissipate excess heat from steel products and associated machinery. Cooling applications account for the bulk of water used in a steel plant, and include contact cooling in hot and cold rolling processes, off-gas cooling and containment, cooling of ovens and furnaces, and other applications.
The amount of water drawn and discharged by a facility will vary significantly depending upon the type of cooling system used. Once-through cooling systems have the highest demand for water; thus, facilities looking to reduce draw and discharge volumes may well be served by switching to recirculating cooling systems that retain some or nearly all water for repeated cooling cycles.
Process water
Process water broadly includes streams that make contact with the raw materials or end products of steel production, or which becomes a part of the final product. There are many process water applications, including physical separation of ore constituents, quench hardening, descaling, galvanizing, and plating. Process water is also a component of solvents, acids, and emulsions used for cleaning, degreasing, and rinsing steel surfaces.
Water reuse and recycling approaches depend upon which process water streams are in question. In general, it is possible for facilities to collect spent process water streams and employ appropriate separation technologies to remove contaminants and bring the water to an acceptable quality range, either for reuse in subsequent process applications or recycled for other uses within the facility. The benefits of pre- and post-treatment of process water can include reduction of overall water draw and discharge volumes as well as reducing wastage costs through the recovery of raw materials and chemicals.
Boiler feed water
Boiler feed water is used to generate process steam used to power many processes involved in steel production. Boilers are used to produce energy for process heating and cooling, as well as powering mechanical drive systems and pressure control systems.
Boiler systems often have high water quality standards to ensure safe function under their typically high temperature and pressure operating conditions. With proper pre-treatment, however, water from various sources can be recycled for use as boiler makeup water.
Other water use
Steel plants also use water for an array of miscellaneous applications to support plant operations, including water for general cleaning purposes, drinking, sanitary systems, and other needs. Many of these applications have less stringent water quality requirements than those required by cooling and process equipment employed in steel production. As such, and in response to more restrictive draw limitations on fresh water sources, some plants are implementing strategies to source and/or recycle gray water for certain applications.
How can facilities treat water for reuse?
Industrial water treatment systems span a wide range of technologies to support various water reuse strategies. For steel plants, this has traditionally included treatment trains consisting of physical and chemical separation technologies, coagulation, flocculation, and activated sludge treatment. In recent years, however, steel plants have increasingly incorporated membrane technologies such as ultrafiltration and reverse osmosis as a cost-effective means of producing high quality water for reuse within the facility. For steel plants facing stringent discharge requirements, zero liquid dischargesystems provide a means of eliminating liquid waste streams completely.
As we’ve discussed above, there are many component processes and systems involved in steel production, each of which might have different water quality standards. Component systems may also produce effluent streams that are widely divergent in terms of temperature, constituents, and other characteristics. Depending upon the individual needs and priorities of a given facility, a plant may choose to implement pre- and post-treatment technologies specific to each component process, such that more precision can be employed in treating specific effluent streams for reuse and/or recycling. Alternatively, a facility may choose to treat wastewater consisting of combined cooling, process, or other streams. While going this route may seem simpler, complex wastewater streams are generally more challenging and less efficient to treat, making it difficult to achieve a level of quality appropriate for recovery and reuse.
While it’s clear that water reduction and reuse strategies offer many benefits, it is still important for steel plants to balance a few factors when deciding on a specific approach to water management. These might include:
-
-
- Source water quality and availability: Facilities need to consider whether adequate volumes of water are available to the plant, and what types of source water treatment might be necessary to make the water suitable for use within the facility. Treating effluent streams for reuse within the facility is generally more cost-effective than sourcing and treating large quantities of raw water, however, factors like the geographic location of the plant, seasonal fluctuations, and source water quality all affect the bottom line.
- Energy efficiency: In developing a water management plan, steel plants need to consider how much energy would be needed to treat water for reuse, recycling, and/or discharge. Operating a water treatment train will entail its own energy consumption, costs, and environmental impacts that, in some cases, will outweigh the benefits of reduced water usage. Balancing overall impacts is critical to maximizing the effectiveness of a water management program.
- Legal, regulatory, and safety requirements: Steel plants must consider regulations and local limitations on withdrawal and discharge volumes, and as well as effluent water quality standards. An effective water management plan should help the facility achieve and maintain compliance with regulations and local requirements, while also allowing the facility to operate at its target production capacity.
-
In short, steel production presents a significant opportunity for cost savings related to reduction and reuse of water, though water management strategies that balance their unique needs.
Can SAMCO help?
SAMCO has over 40 years’ experience in the design and manufacture of custom water treatment systems for a range of industries and applications, so please feel free to reach out to us with your questions.
Get in touch with us here to set up a consultation with an engineer or request a quote. We can walk you through solutions that fit your water reduction and reuse needs and maximize your return on investment.
Head on over to our blog to learn more about available water treatment technologies to help reduce industrial water consumption. Some articles that might be of specific interest to you include:
- Why Your Industrial Facility Should Plan for Water Shortages Sooner Rather Than Later
- Industry and Water Shortages: Is Your Facility Ready?
- Five Ways Your Industrial Facility Can Conserve Water and Plan Ahead for Shortages
- How Can You Reduce Water Used in Electrical Generation?