What Is a Biological Wastewater Treatment System and How Does It Work?
For an industrial company producing waste as part of its process, some type of wastewater treatment system is usually necessary to ensure safety precautions and discharge regulations are met. The most appropriate wastewater treatment system will help a facility avoid harming the environment, human health, and a facility’s process or products (especially if the wastewater is being reused). It will also help the facility curb heavy fines if wastewater is being improperly discharged into a POTW (publicly owned treatment works) or to the environment (usually under a NPDES, or National Pollutant Discharge Elimination System, permit).
Typically used as a secondary wastewater treatment method after the initial larger contaminants have been settled and/or filtered out, biological wastewater treatment systems can be efficient and economical technologies for breaking down and removing organic contaminants from heavily organic-laden wastes, such as those produced in the food and beverage, chemical manufacturing, oil and gas, and municipal industries.
But “what is a biological wastewater treatment system and how does it work?”
Since this subject can be extremely multifaceted and complex, this article will break down the basics as an overall introduction to some of the more common biological wastewater treatment methods used industrially today.
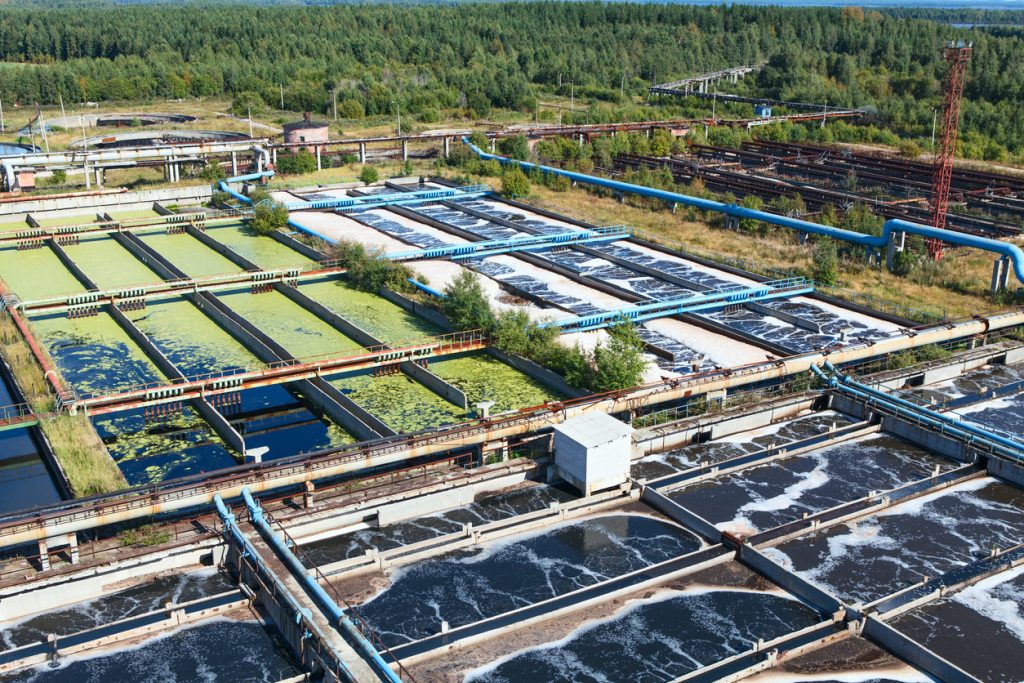
What is a biological wastewater treatment system?
In a simplified, top-level answer to this question, a biological wastewater treatment system is a technology that primarily uses bacteria, some protozoa, and possibly other specialty microbes to clean water. When these microorganisms break down organic pollutants for food, they stick together, which creates a flocculation effect allowing the organic matter to settle out of the solution. This produces an easier-to-manage sludge, which is then dewatered and disposed of as solid waste.
Typically broken out into three main categories, biological wastewater treatment can be:
-
-
- aerobic, when microorganisms require oxygen to break down organic matter to carbon dioxide and microbial biomass
- anaerobic, when microorganisms do not require oxygen to break down organic matter, often forming methane, carbon dioxide, and excess biomass
- anoxic, when microorganisms use other molecules than oxygen for growth, such as for the removal of sulfate, nitrate, nitrite, selenate, and selenite
-
The organic contaminants these microorganisms decompose are often measured in biological oxygen demand, or BOD, which refers to the amount of dissolved oxygen needed by aerobic organisms to break down organic matter into smaller molecules. High levels of BOD indicate an elevated concentration of biodegradable material present in the wastewater and can be caused by the introduction of pollutants such as industrial discharges, domestic fecal wastes, or fertilizer runoff.
When pollutant levels are elevated, BOD can deplete the oxygen needed by other aquatic organisms to live, leading to algal blooms, fish kills, and harmful changes to the aquatic ecosystem where the wastewater is discharged. Because of this, many facilities are required to treat their wastes, perhaps biologically, prior to discharge—but it’s the level of organic and inorganic pollutants in relation to their discharge requirements that will dictate what specific unit operations a facility’s biological wastewater treatment system will need and how they are sequenced and operated.
In short, biological industrial wastewater treatment systems optimize the naturally occurring process of microbial decomposition to break down industrial wastewater contaminants so that they, along with other unwanted materials, can be removed. They also often replace (and are sometimes used alongside) physical and chemical treatments, which can be among the pricier treatment alternatives.
How does a biological wastewater treatment system work?
Depending on the chemical makeup of the wastewater in relation to the effluent requirements, a biological wastewater treatment system might be composed of several different processes and numerous types of microorganisms. They will also require specific operational procedures that will vary depending on the environment needed to keep biomass growth rates optimal for the specific microbial populations. For example, it often is required to monitor and adjust aeration to maintain a consistent dissolved oxygen level to keep the system’s bacteria multiplying at the appropriate rate to meet discharge requirements.
In addition to dissolved oxygen, biological systems often need to be balanced for flow, load, pH, temperature, and nutrients. Balancing a combination of system factors is where the biological treatment process can become very complex. Below are examples of some common types of biological wastewater treatment systems, including a brief description of how they function within an industrial wastewater treatment regimen to give you an idea of the types of technologies and systems that might benefit your industrial facility.
Aerobic wastewater treatment technologies
Activated sludge was first developed in the early 1900s in England and has become the conventional biological treatment process widely used in municipal applications but can also be used in other industrial applications. Wastewaters from the primary treatment phase enter an aeration tank where it is aerated in the presence of suspended (freely floating) aerobic microorganisms. The organic material is broken down and consumed, forming biological solids which flocculate into larger clumps, or flocs. The suspended flocs enter a settling tank and are removed from the wastewater by sedimentation. Recycling of settled solids to the aeration tank controls levels of suspended solids, while excess solids are wasted as sludge. Activated sludge treatment systems typically have larger space requirements and generate large amounts of sludge, with associated disposal costs, but capital and maintenance costs are relatively low, compared to other options.
Fixed-bed bioreactors, or FBBRs, developed as forced-air industrial treatment systems in the 1970s and 80s, consist of multiple-chambered tanks in which the chambers are packed tight with porous ceramic, porous foam, and/or plastic media; the wastewater passes through the immobilized bed of media. Of all biological treatment systems, FBBRs can hold the most contaminant-eating microbes in the smallest volume, which makes FBBRs space-saving and energy-efficient technologies ideal for treating wastewaters from medium to medium-high BOD feed levels down to very low effluent levels. The media is engineered to have a high enough surface area to encourage a robust biofilm formation with long solids lifespan, resulting in low sludge formation and lowest sludge disposal costs. A well-engineered fixed-bed will allow wastewater to flow through the system without channeling or plugging. Chambers can be aerobic and still have anoxic zones to achieve aerobic carbonaceous removal and full anoxic denitrification at the same time. More advanced biological processes can be facilitated with these systems (for example, nitrification, denitrification, deselenation, sulfide-reduction, and anammox), by having unique bacterial populations colonize the biofilm media in separate tank chambers, which can be uniquely configured to treat your facility’s specific wastewater constituents.
Moving bed bioreactors, or MBBRs, invented in the late 1980s in Norway, already has been applied in over 800 applications in more than 50 countries, with approximately half treating domestic wastewater and half treating industrial wastewater. MBBRs typically consist of aeration tanks filled with small moving polyethylene biofilm carriers held within the vessel by media retention sieves. Today the plastic biofilm carriers come from many vendors in many sizes and shapes, are typically half- to one-inch diameter cylinders or cubes and are designed to be suspended with their immobilized biofilm throughout the bioreactor by aeration or mechanical mixing.
Because of the suspended moving bio-film carriers, MBBRs allow high BOD wastewaters to be treated in a smaller area with no plugging. MBBRs are typically followed by a secondary clarifier, but no sludge is recycled to the process; excess sludge settles, and a slurry removed by vacuum truck, or settled solids are filter pressed and disposed as a solid waste.
MBBRs are often used to remove the bulk of BOD load upstream of other biological treatment processes or used in situations where effluent quality is less important; they are not used for polishing BOD to low effluent levels. They are used for treating wastewaters produced in food and beverage facilities, meat processing and packing plants, petrochemical facilities, and refineries.
Membrane bioreactors, or MBRs, came into common use in the 1990s once membrane modules were submerged directly in the aeration tank, and air scour was implemented to keep the membranes from fouling. MBRs are advanced biological wastewater treatment technologies that combine conventional suspended-growth activated sludge with membrane filtration, rather than sedimentation, to separate and recycle the suspended solids. As a result, MBRs operate with much higher mixed-liquor suspended solids (MLSS) and longer solids residence times (SRTs), producing a significantly smaller footprint with a much higher quality effluent compared to conventional activated sludge.
MBRs primarily target BOD and total suspended solids (TSS). MBR system design varies depending on the nature of the wastewater and the treatment goals, but a typical MBR might consist of aerobic (or anaerobic) treatment tanks, an aeration system, mixers, a membrane tank, a clean-in-place system, and either a hollow fiber or flat sheet ultrafiltration membrane. As a result of its many parts and cleaning processes, MBRs are known for high capital, high operating, and high maintenance costs.
Biological trickling filters are used to remove organic contaminants from both air and wastewater. They work by passing air or water through a media designed to collect a biofilm on its surfaces. The biofilm may be composed of both aerobic and anaerobic bacteria which breakdown organic contaminants in water or air. Some of the media used for these systems include gravel, sand, foam, and ceramic materials. The most popular application of this technology is municipal wastewater treatment and air remediation to remove H2S at municipal sewer plants, but they can be used in many situations where odor control is important.
Anaerobic Wastewater Treatment Technologies
Upflow anaerobic sludge blankets, or UASBs, useanaerobic bacteria to, as mentioned in the intro of this article,breakdown organics without the use of oxygen, resulting with a combustible methane-bearing biogas, treated effluent, and anaerobic sludge. With UASB systems, the general idea is that wastewaters are pumped into the base of the system, where the organics in the wastewater flow through a blanket of sludge before entering the upper gas-liquid-solids (GLS) separator, where collection hoods capture the biogas while allowing the suspended solids to settle and return to the lower reaction zone, while the cleaned effluent overflows out of the top of the system. The biogas (methane and carbon dioxide) is either flared or used to generate steam or electricity for use in other processes at the facility.
The UASB process creates less sludge than aerobic biosystems and therefore needs to be cleaned out and emptied less than other biological treatment systems, but they require skilled operators to maintain optimal hydraulic and anaerobic conditions for UASBs to operate properly. Expanded granular sludge beds, or EGSBs, are a similar process, but EGSBs use a stronger upward force to encourage more wastewater-to-sludge contact.
Anaerobic digesters also useanaerobic bacteria to break down organic waste without oxygen and produce biogas, mostly for sewage treatment, and there are a variety of anaerobic digesters available. They each perform the same process in slightly different ways. Examples include covered lagoons, fixed film, suspended and submerged media, and continuous stirred tank reactors.
Can SAMCO help?
SAMCO has over 40 years’ experience custom-designing and manufacturing wastewater treatment systems, so please feel free to reach out to us with your questions. For more information or to get in touch, contact us here. You can also visit our website to set up a call with an engineer or request a quote. We can walk you through the steps for developing the proper solution and realistic costs for your biological wastewater treatment system needs.
For more information on biological wastewater treatment, see these other articles that might interest you:
-
- What Are the Best Biological Wastewater Treatment Equipment Supply and Technology Companies?
- Common Problems with Biological Wastewater Treatment Systems and How to Avoid Them
- How Much Do Biological Wastewater Treatment Systems Cost?
- Biological vs. Chemical Wastewater Treatment Which Is Better for Your Industrial Facility?