How Much Do Reverse Osmosis and Nanofiltration Systems Cost?
Reverse osmosis and nanofiltration membrane systems are used in a variety of processes and applications, and they are often spoken about in unison as they are similar membrane technologies. They are being utilized more and more by industrial facilities looking to recycle and treat water for reuse and conservation. As water scarcity issues continue to increase, these technologies have become a long-term economical solution for avoiding astronomical discharge and water-usage fees in addition to serving other filtration requirements, such as process-water generation and product concentration.
If you are looking for a separation and/or filtration solution, you might be thinking RO/NF is a good fit. But how much do reverse osmosis and nanofiltration membrane systems cost?
Although it can be difficult to pinpoint exactly what you might be spending on an RO/NF membrane system since the solutions and configurations of these systems can be complex, it is possible to simplify and narrow the cost down to a range.
In the article below, we break down what your facility might be spending for a reliable RO/NF membrane system and outline the various factors that often drive that cost up and down:
What’s included in a basic RO/NF membrane system?
For raw water or wastewater, in particular, the configuration of an industrial RO/NF system will depend on the application and characteristics of the waster in relation to the required level of purity. Although each system is typically unique and custom-designed, most RO/NF membrane systems will have some type of:
-
-
- Inlet collection tank
- Feed pump skid and tank
- Filtration system (typically MF/UF for raw water or wastewater)
- Membrane/module rack
- Receiving tank
- Backwash pumps off the receiving tank for MF/UF
- Chemical cleaning systems
- Compressed air for scouring the membrane when MF/UF is cleaned
- Automation instrumentation (such as PLC controls)
-
The inlet collection tank feeds to a pumping system that normally has two pumps, enabling the system to be run consistently, 24 hours a day. The water then flows to a holding tank large enough for a half hour to an hour’s worth of influent, depending upon the nature of the feed stream. If the feed stream has a lot of variability to it, the tank might need to hold more in order to give the stream time to blend out the ups and downs in the feed source.
From there, the water flows through a prefilter to take out particles large enough to plug the internal fibers of the ultrafiltration (UF) filter, which is usually a type of strainer, though there are different types of designs. From there it gets fed to the UF system, which reduces suspended particles, bacteria, and viruses from going into the RO. It’s often cleaned several times a day with back pulsing and chemical cleaning (in some cases, chlorination) to keep the module sanitized. Every once in a while, a CIP with intense chemical cleaning is performed (once a month or once a quarter). The cleaning skid should be included with the UF/RO/NF membrane system, along with backwash pumps, cleaning pumps, air scour blower, etc.
After UF, the permeate is collected in the holding tank. The purpose of the holding tank has two functions: it’s used to backwash the filter, and it’s also used for forward-flow to the RO unit.
The RO has a cartridge filter housing, and it’s followed by the membrane array specifically designed for that application. A typical array is two by one, where the water goes through stage one, then the brine concentrate goes to a stage two. But there are all kinds of different arrays and they are all designed with computerized modeling tools, depending on the facility’s required flow rate.
From there, the water goes on to a holding tank that has a substantial amount of storage capacity to store enough water in case you have to take the RO down and clean it, and it’s also designed to handle the peak flows to production. So if you have a production that needs 100,000 gallons per day but you use the water over 16 hours, then your storage tank needs to have enough water to cover the 16 hours of consumption. Next are booster pumps that pump the water out of the holding tank to points of use.
On the side of these systems are a separate CIP system for cleaning the RO, and that system is typically also used for cleaning the UF.
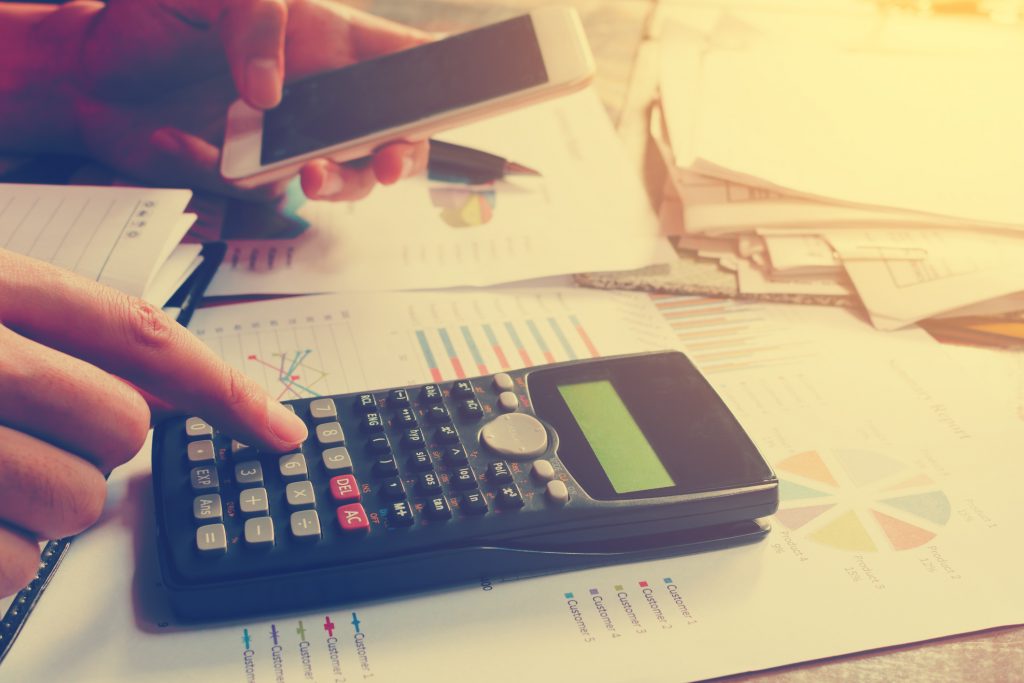
The main factors of RO/NF membrane system cost
Water characterization
The main factor that will drive up and down RO/NF membrane system cost is the characterization of the water—whether it’s surface or well water, and how dirty it is (is there algae, organics, or a lot of metals to cause scaling and fouling?).
With RO/NF, there is usually pretreatment required, but what that treatment entails will depend upon the degree of contaminants. If no pretreatment is used (UF), the RO/NF membranes will likely experience fouling and cause all sorts of problems, possibly even plant downtime.
Flow rates
On both the UF pretreatment and RO/NF devices, there is a linear “scaling up” based on flow (how many are stacked up depend on the flow rate). You can often estimate the cost of the membrane rack by flow rate and the flux rate you’re designing it to.
There are two functions that will affect the cost of the system here: flow rate and how much water you want to make from each membrane. The cleaner the water, the higher the flux rate can be (gallons per day per square foot of membrane surface area).
Construction materials
The last factor that will affect the cost of your RO/NF membrane system is the construction materials. In a municipal application where PVC piping is used, its’s going to be less expensive than an industrial, medical, or power application where all stainless steel piping will add substantial amount to the cost. Piping into the front end of the UF is sometimes PVC or CPVC, whereas piping coming out might be cleaner materials such as polypropylene. PVC piping has chemicals in the makeup material that can leach into the water, so in applications for the pharmaceutical industry, as an example, these pipes require higher end materials to preserve the required purity. Also, some facilities that look to hot-sanitize the piping require stainless steel piping, or piping that can handle the heat.
Other important factors to consider when pricing a RO/NF membrane system
- Up-front planning. Developing the concepts, designs, and regulatory requirements for your project is the first step to planning your RO/NF membrane system. The cost of engineering for this type of project can typically run about 10–15% of the cost of the entire project and is usually phased in over the course of the project, with most of your investment being allocated to the facility’s general arrangement, mechanical, electrical, and civil design. The lower the equipment cost the higher the percentage. The higher the capital equipment cost the lower the percentage.
- Space requirements. When planning for a RO/NF membrane system, the size of your system and your plant location will affect your cost. For example, if your plant is located in a place that is very expensive when it comes to space, you might want to aim for a smaller footprint, if possible.
- Installation rates. Another thing to keep in mind is the installation rates in your area. These sometimes also fluctuate by location, so be sure you’re aware of the cost to install the system and factor this into your budget. In areas where installation costs are high you may want to consider prepackaged modules versus build-in-place facilities.
- Level of system automation needed. When it comes to the level of automation you need for your RO/NF membrane system, there are two options. The first is a higher level of automation where you won’t need an operator present for much of the time. With type of automation, you can eliminate much of the human error associated with running the plant, and although this option is more costly up front (an initial investment in more sophisticated PLC controls and instrumentation), the ongoing labor costs are less. The second option is a lower level of automation with less capital cost, but with added labor, this can end up costing you more in the long run. When deciding whether or not to invest in more costly controls, you need to consider what works for your company and staffing availabilities.
- Turnkey and prepackaged systems. If you are able to order your RO/NF membrane system prepackaged, this will typically save you construction time at about the same cost or less. A benefit to having your system prepackaged is that the production facilities and fabrication shops that assemble your system are, more often than not, highly knowledgeable about the type of system they are manufacturing. This results in a quick and efficient fabrication versus build-in-place facilities. Sometimes when you hire a field crew, there is a bit of a learning curve that can add extra time and/or cost to a project. SAMCO specializes in these types of turnkey, prepackaged systems, and for more information about what we offer, you can visit our website here. Installation costs will vary, but typically range between 15–40% of the project cost, depending on the specifics of prepackaging and amount of site civil work needed.
- Shipping the system to your plant. When having your RO/NF membrane system shipped to the plant, you usually want to factor in about 5–10% of the cost of the equipment for freight. This can vary widely depending upon the time of year you are purchasing your system in addition to where your plant is located in relation to the manufacturing facility. When you are looking to purchase your system, check with your manufacturer to see if there is a facility where the system can be constructed closer to you, if not on-site.
- Operation costs. Also keep in mind that particular technology packages cost a certain amount to purchase upfront, but you need to also factor in system operating costs over time. For decisions like these, you need to weigh the pros and cons of initial versus long-term cost investment in addition to what works for your company and staff. You will likely want to look into having someone develop an operating cost analysis so your company can plan ahead for the operating cost over your facility’s life cycle. This might help you consider whether or not you want to spend more on your system initially or over time.
- Other possible costs and fees. When purchasing a RO/NF membrane system, you might also want to keep in mind what other hidden costs and fees might be. For example: Will there be any taxes on the system or additional purchasing fees? What are your possible utility costs to the installation area? Will there be any environmental regulatory fees and/or permits? Any ongoing analytical compliance testing you need to pay for?
Also consider that there will be costs to treating the secondary waste produced by the system. With stringent environmental regulations, you will need to either treat the waste for hauling away or solidify with a filter press/evaporator and transport to third party disposal firm.
Also be sure to ask your system manufacturer about options that might be cheaper to install. They might be able to shed some light on the more installation-friendly systems with suggestions on how to keep your costs to a minimum.
The bottom line
A five to 10 GPM RO/NF membrane system, along with the ancillary equipment (you might add about another $10k with tanks, pumps, and things like that), the system could be about $45,000 to $60,000 for a small, commercial-quality unit. When you get into higher industrial qualities, you can double or triple that cost, whereas a 30 to 50 GPM commercial-quality system would be about $200,000.
A high-end 100 gallon per minute system (GPM) with all the top end instruments stainless steel piping (such as for a power plant with) could be a $1 million system. For a commercial-quality system at 100 gallon per minute system, cost could be as low as $250,000.
When you get into bigger systems, such as a 300 GPM, cost could be $2 to $4 million, depending on what pretreatment type of pretreatment is required.
What Now?
As you can see, there are a variety of factors that go into estimating the cost of an RO/NF membrane system for your facility. SAMCO has over 40 years’ experience custom-designing and manufacturing these types of systems, so please feel free to reach out to us with your questions.
For more information or to get in touch, contact us here to set up a consultation with an engineer or request a quote. We can walk you through the steps for developing the proper solution and realistic cost for your RO/NF membrane system needs.
Some other articles about reverse osmosis and nanofiltration membrane systems you might be interested in include:
- Does Your Facility Need a Reverse Osmosis or Nanofiltration System?
- How Do You Choose the Best Reverse Osmosis and Nanofiltration Membrane System for an Industrial Facility?
- Reverse Osmosis and Nanofiltration Membrane Filtration Systems: Common Problems and How to Fix Them
- What Are the Best Companies for Reverse Osmosis and Nanofiltration Membrane Systems?
- Reverse Osmosis vs Nanofiltration Membrane Process: What Is the Difference?