How to Increase Your Industrial Cooling Tower Efficiency
Although cooling towers are generally some of the most cost-effective cooling mechanisms as compared to other cooling technologies (such as many dry air cooling systems), it is still important to monitor your industrial cooling tower efficiency and run it as seamlessly as possible. This will ensure your facility can:
- Save energy
- Reduce the amount of water being consumed
- Decrease the amount of chemicals required for water treatment
- Extend the equipment service life
- Reduce operating costs, overall
But how can you make sure your cooling tower is being maintained in the most efficient way possible? This article breaks down the complex answer to this question below.
Understand what kind of cooling tower you have
The first step in making sure your cooling tower is being run efficiency is becoming familiar with the type of cooling tower you have and how it works. Different types of cooling towers are exposed to different types of contaminants and require specific treatment.
Some of the most common types are as follows:
Once-through cooling tower systems
Once-through cooling towers draw water from a source such as a river or lake and circulate the water through pipes to absorb heat from steam condensers. The warmed water is then discharged into the environment. Although these systems are generally the easiest and most cost-effective cooling tower option to set up and use, some facilities choose other options for cooling, either because of local regulations (if water is scarce in the area, there might be rules mandating how much water can be withdrawn and discharged in to the local environment) or because it can be difficult to locate a facility in a place that has enough water to draw from. Some facilities are converting their once-through cooling systems into closed-circuit systems.
Open recirculating cooling tower systems
If your facility uses an open recirculating cooling system, the same water is continually used and recirculated throughout the process, removing heat with evaporation. Reusing the water (not lost to evaporation) helps reduce the amount of water needed to run the tower in addition to chemical costs for water treatment, as the chemistry is generally retained in the system. This does, however, increase the likelihood of corrosion and deposition as the solids become more concentrated in the system after evaporation occurs. The heat in combination with open-air conditions can also facilitate bacterial growth and collect contaminants from the air.
Closed recirculating cooling towers
Also known as closed-circuit or closed-loop cooling systems, closed recirculating cooling towers operate similarly to open recirculating systems, except the rejected heat is transferred to a heat exchanger with no part of the process being exposed to the open air. This eliminates contamination once the proper water chemistry is attained and the only time there needs to be makeup water added to the system is if there is a leak.
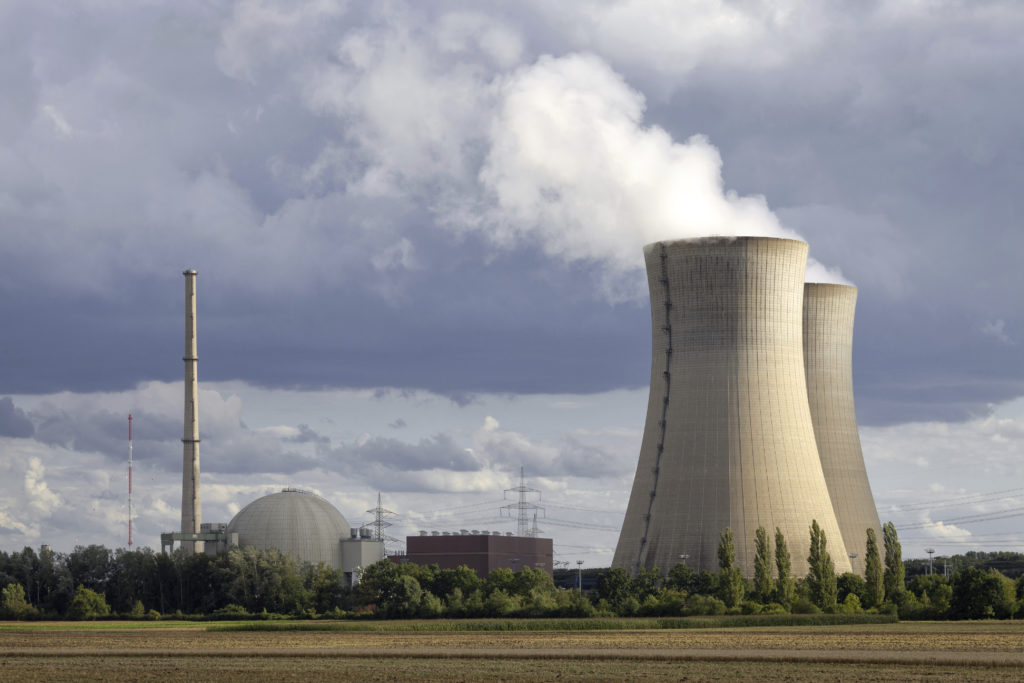
Be aware of source-water quality and the quality of water needed to run the system
Depending on the type of cooling tower you are operating and how it works, your specific water treatment requirements may vary, but in general, the three main areas of the cooling tower process that typically require treatment are: feed water to the cooling tower, circulatory water in the tower, and cooling tower bleed to drain.
Feed water to the cooling tower
Depending on the quality of the cooling tower feed water, you may or may not need treatment here. If a water treatment system is needed at this part of the cooling tower water process, it is usually technology that removes hardness and silica or stabilizes / adjusts the pH.
At this point of the process, the proper treatment optimizes the tower evaporation cycles and minimizes the water bleed rate to drain beyond what might be done with chemicals alone.
Circulatory water in the tower
The second area of physical treatment a cooling tower will typically need is for the circulation water within the tower.
Normally some form of side stream filtration is your best bet. This helps keep your cooling tower water free of particles that can build up and foul the cooling tower. By running approximately 10% of the circulated water through the side stream filter, it can be easier to retain a healthy balance of suspended solids that will reduce the particulate fouling of your equipment.
The chemical treatment of a cooling tower will typically occur at this phase within the tower. Proper chemical treatment minimizes scale formation, corrosion of critical equipment, and helps disperse suspended solids so settling can be minimized in low-flow areas.
[Download our free cooling tower water treatment e-book.]
Cooling tower bleed to drain
The last part of treatment required for cooling tower water is the blowdown or bleed from the tower.
Depending on how much water the cooling plant needs to circulate for proper cooling capacity, plants can choose to recycle and recover the water through some type of post treatment in the form of reverse osmosis or ion exchange, especially in places where water might be scarce.
This allows liquid and solid waste to be concentrated and removed while treated water can be efficiently returned to the tower and reused.
Know the materials your unit is made from
The second step in understanding how to efficiently run your cooling tower is to know what the cooling tower is made of. Is it constructed of galvanized or stainless steel? Does it use plastic piping? Fiberglass? Is there a protective coating applied to reduce corrosion? Each of these materials withstands deterioration and environmental factors in different ways.v
Some newer cooling towers are constructed from fiber-reinforced polyester (also known as FRP), which can be lightweight and hold up to higher chemicals usage and ranges in pH. Another common configuration is galvanized metal with a stainless steel sump or basin, which can provide durability without the extremely high cost of a cooling tower made entirely out of stainless steel.
It’s important to know what the tower is made of, what materials are used for what parts, and what the manufacturer and your water treatment specialist recommend in terms of cooling tower water quality to reduce the possibility and/or severity of corrosion and breakdown of equipment over time.
Keep track of your cooling system’s water loss
In cooling towers, water can be lost several ways. Knowing when and how much water your system loses through evaporation, blowdown, drift, and/or leaking is essential in making sure corrective measures are being taken to conserve this water if needed.
Keep in mind these water losses will fluctuate and some can be estimated by the cooling tower manufacturer, but according to the Environmental Protection Agency, these losses and calculations include:
- This is typically about 1% of the rate of recirculating water flow for every 10°F temperature drop that the cooling tower reaches.
- Blowdown or bleed-off. This calculation depends on the number of cycles, level of evaporation, and quantity of makeup water required. It can be calculated if you know the value of any two of these three factors.
- Water carried off by wind or mist is known as “drift” and can vary from 0.05% to 0.2% of the flow rate through the cooling tower without the use of drift eliminators, which can reduce this to negligible amounts.
- Leaks and overflows. Properly running units will not experience leaks or overflows, but if they do occur, the amount of water lost needs to be accounted for the makeup water calculation: Makeup water needed = Evaporation + Drift + Blowdown + Leaks and Overflows
Improve the efficiency of your chemical usage
Working with your water treatment specialist, explore options for monitoring and minimizing the use of chemicals, which can be costly. Closely monitoring cooling tower water chemistry can also help reduce deposition and corrosion, improving system efficiency and extending the service life of your equipment.
Properly pretreating the cooling tower makeup water can help with this as well. Water treatment systems such as ion exchange for softening or reverse osmosis for filtration can lessen the amount of chemicals required to keep heat exchangers and piping free from scaling ad fouling. But as with all water treatment options for cooling tower water, it’s important to consult a specialist who can make recommendations based on your facility’s individual needs.
In conclusion
Being aware of potential cooling tower water treatment issues and knowing how to solve them is essential to the success and efficiency of your process. When it comes to deciding the right solutions for your cooling tower water treatment, it is extremely important to consult a water treatment specialist. The proper maintenance of your system will depend on your plant’s individual needs.
SAMCO has over 40 years’ experience custom-designing and manufacturing cooling tower water treatment systems. With extensive knowledge about cooling tower chemistry and flow dynamic—in addition to several combinations of technologies that can help you treat your individual makeup water, side-stream filtration, and cooling tower blowdown needs—chances are we have a solution for you, so please feel free to reach out to us with your questions.
For more pricing information or to get in touch, contact us here to set up a consultation with an engineer or request a quote. We can walk you through the steps for developing the proper solution and realistic cost for your cooling tower water treatment system needs.
Some other articles about cooling tower water treatment you might be interested in include:
- What Is a Cooling Tower Water Treatment System and How Does It Work?
- How Do You Know If You Need a Cooling Tower Water Treatment System for Your Plant?
- Common Cooling Tower Water Treatment Problems and How to Solve Them
- Treated vs. Untreated Cooling Tower Water: Risks for Your Plant
- Five of the Best Cooling Tower Water Treatment Equipment Supply and Technology Companies
- How Much Does a Cooling Tower Water Treatment System Cost? (Pricing, Factors, Etc.)