Common Boiler Feed Water Treatment Issues and How to Avoid Them
When treating boiler feed water (the combination of boiler makeup and condensate return water), several issues can arise that cause boiler scaling, corrosion, fouling, and system failure.
Below, we break down the most common boiler feed water issues and how to avoid them to help ensure system efficiency and operational safety. While treating boiler feed water is extremely unique to each individual process and boiler, these are generalized issues that typically occur. Any specific boiler feed water treatment options and/or issues should be analyzed on a case-by-case basis and discussed with your water treatment specialist.
An increase of sludge
What it means
If a boiler is seeing higher-than-normal amounts of sludge (sediment of solids or oil that are usually softer than scale but can get hard and scale after being “baked” onto the heat exchangers), there could be an issue with filtration and/or solids removal upstream or the collected precipitants from poor water treatment. Filtration and softening methods being used to treat the feed water might not being doing their job, and this could spell trouble for piping and boiler efficiency down the line. Solids that settle in the low-flow areas of internal piping can cause an insulation layer to form, causing excessive heating of the tubes causing localized overheating and eventual blowout.
How to avoid it
The best way to combat sludge in a boiler is to eliminate any sludge-causing contaminants before they become an issue in addition to blowing out any sludge accumulations before they have a chance to bake onto high-heat surfaces, where they are extremely difficult to remove.
Sometimes sludge conditioners are helpful internally of the boiler (except for high-pressure boilers . . . in that case, liquid conditioners shouldn’t be used), where they disperse the sludge-causing solids so they can be removed with the blowdown. Otherwise, careful monitoring of the presence of these contaminants is key. Certain polymers and filtration methods are effective for solids removal.
Filtering the feed water for suspended solids should be considered for high-pressure boilers. Technologies such as microfiltration and ultrafiltration are excellent choices for removing suspended solids and colloidal suspensions such as colloidal silica.
Scale buildup
What it means
Scaling is a deposit formed on the inside of piping and heat transfer surfaces when the water is heated and impurities precipitate or settle out leaving behind extremely hard deposits.
Some common feed water contaminants that cause scaling include:
-
-
- Silica
- Iron
- Calcium
- Magnesium
- Aluminum
-
How to avoid it
The level of scaling on a boiler will be determined by the amount of these impurities in relation to the pressure a boiler is run at. For example, many higher-pressure boilers will require a higher quality of water with less contaminants than some lower-pressure boilers. Boilers that generate steam to power turbines, for example, require high-pressure boilers and therefore more complex feed water treatment system to remove as many impurities as possible.
General guidelines for feed water purity will come from the boiler manufacturer. There are some organizations, such as the American Society of Mechanical Engineers, that have contamination limitation recommendations based on the pressure your boiler runs, but again, it’s best to check with the boiler manufacturer for these numbers to be sure. For low-pressure boilers, simple sodium cycle water softeners will work just fine. For high-pressure boilers advanced technologies such as reverse osmosis, electrodeionization, or deionization will be required. Your water treatment specialist should be able to evaluate what is best for your boiler and process.
[Download our free boiler feed water treatment e-book.]
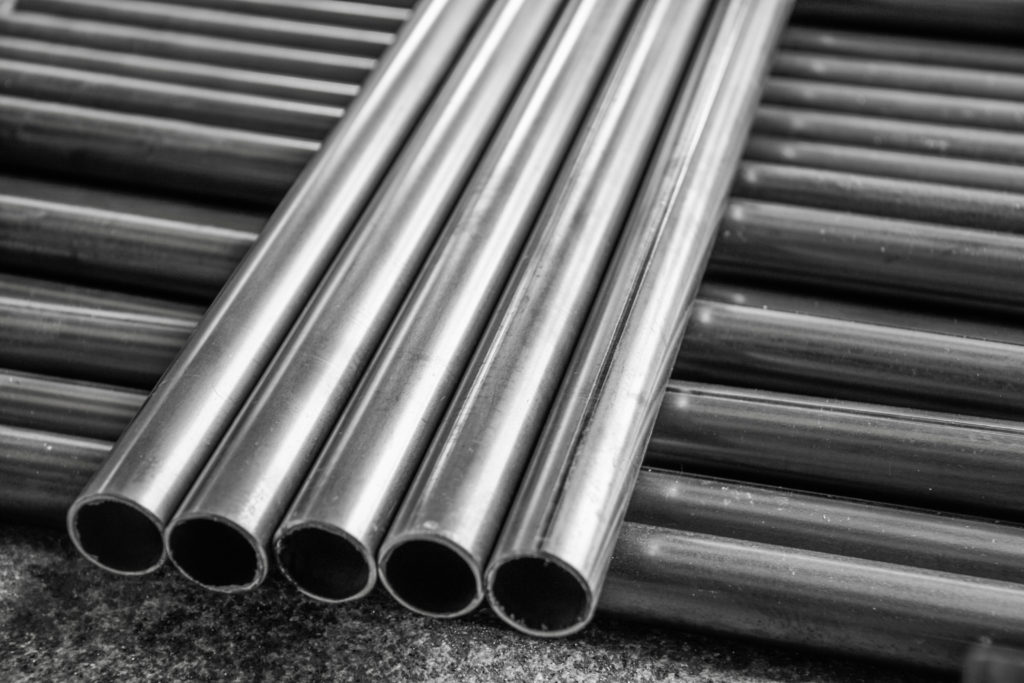
System corrosion
What it means
Corrosion in boilers, or the breakdown of the metal elements of the device, can happen for a variety of reasons. The most common reason is the presence of dissolved oxygen and carbon dioxide, which eat away at areas of the boiler causing system stress and cracking. The higher the boiler pressures, the more severe the corrosion. When chlorides are present at an unacceptable level, chloride stress cracking can also occur.
Corrosion typically occurs in the parts of the boiler that are heated the most, where high temperatures and cracking in the metals accelerate the breakdown of the materials. There are several types of corrosion that can occur in a boiler, and the type you might encounter can depend on the proper pH, level of oxygen, amount of solids, and overall design of the boiler.
How to avoid it
High-quality oxygen scavengers can be effective in removing these dissolved gases from boiler feed water in addition to deaerators. These two methods are widely used in the removal of the harmful gases that can break down and wreak havoc on boiler tubing and equipment. Managing the internal chemistry within proper pH levels along with an overall internal chemistry program is also critical.
Foaming and Priming
What it means
Foaming and priming in a boiler occurs when there are high amounts of dissolved solids present at the water surface. When the steam is generated, these impurities bubble up (foaming) and evaporate with the steam (priming), latching on to superheaters and turbines, decreasing their efficiency. Foaming is the production of persistent foam or bubbles in boilers, which do not break easily. Foaming is due to presence of substances like oils (which greatly reduce the surface tension of water).
Priming and foaming usually happen simultaneously. It’s best to avoid them because:
-
-
- they can cause dissolved salts to deposit on superheater and turbine blades, reducing system efficiency
- they might allow dissolved salts to enter other parts of the system, thereby reducing the service life of the affected machinery
-
How to avoid it
The best way to avoid foaming and priming is to maintain a low level of dissolved solids and control alkalinity in your boiler. Membrane filtration, ion exchange, and softening can be helpful, as well as making sure pH remains between 8.5 and 9.5.
How SAMCO can help
A good overall boiler feed water treatment program includes:
-
-
- proper pretreatment of the feed water to the boiler (the strategy is to remove harmful impurities before they enter the boiler)
- a good program of internal chemistry control (this consists of a proper chemical feed and blowdown program to control scaling, fouling, sludge, and TDS buildup)
- a proper treatment program to condition the steam condensate to control return line corrosion
-
SAMCO has years of experience helping our customers understand this complex chemistry and providing a wide variety of superior boiler feed water treatment technologies, including a host of filtration and resin services. If you have questions about how your boiler’s specific makeup might affect your treatment system, feel free to contact us and set up a call with one of our engineers or visit our boiler feed water treatment page here.
Other SAMCO articles that relate to boiler feed water include:
-
-
- How to Choose the Best Boiler Feed Water Treatment Technologies for Your Plant
- Do You Need a Boiler Feed Water Treatment System for Your Plant?
- Scaling vs. Corrosion: Why It Matters for Your Boiler Feed Water System
- 10 of the Best Boiler Feed Water Treatment Equipment Supply and Technology Companies
- How Much Should a Boiler Feed Water Treatment System for a Thermal Power Plant Cost?
- How Much Does a Boiler Feed Water Treatment System Cost? (Pricing, Factors, Etc.)
- What Is a Boiler Feed Water Treatment System and How Does It Work?
-