How to Remove Lead from Your Industrial Water and Wastewater
Lead (Pb) is perhaps one of the most well-known and closely monitored contaminants found in drinking water, but it is also an area of concern for industrial facilities. These facilities typically pursue lead-removal technologies in order to comply with regulatory wastewater contaminant limitations, though many of the same technologies can be used to help meet process water quality requirements or as part of a reuse and reclamation strategy. In this article, we’ll take a look at how to remove lead from your industrial water and wastewater, and explore some of the benefits and drawbacks associated with the most commonly used treatment technologies.
There are several separation and treatment technologies that are commonly used to remove lead from industrial water and wastewater. Each treatment strategy offers certain advantages or fitness for particular applications; therefore, the best lead removal technology is one that fits a facility’s specific needs. To achieve the best possible lead removal technology, a facility will need to carefully consider stream characteristics such as lead concentration, pH, temperature, flow rate, volume, and BOD. Additionally, a facility will need to consider target lead concentrations, which will depend upon plant location and applicable regulatory requirements as well as the method of discharge for any resulting wastewater and/or sludge. Careful consideration of each of these factors is critical in understanding which types of lead removal and wastewater treatment strategies is best for your facility.
The below list provides a quick overview of water and wastewater treatment technologies that are commonly used for removal of lead:
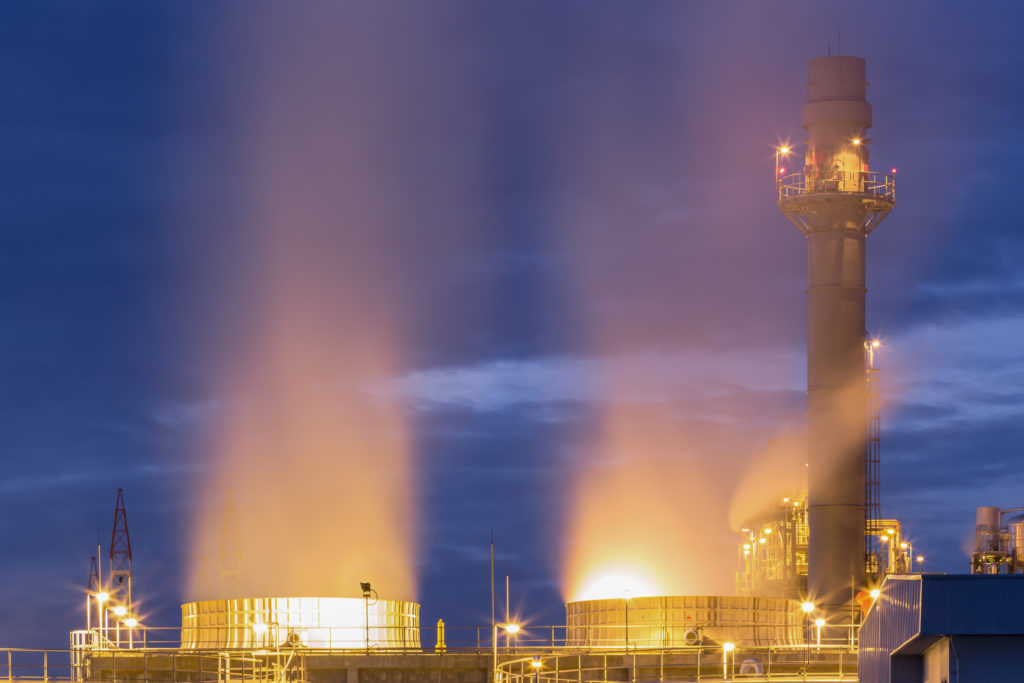
Chemical precipitation
One of the most commonly-used technologies for removing lead from water and wastewater streams, chemical precipitation is a relatively simple and economical process, and is effective for reducing dissolved lead content in streams with high concentrations of the metal.
Chemical precipitation works based on the premise that the solubility of lead (and other heavy metals) depends upon the concentration of the metal and the pH of the solution. The heavy metal precipitation process begins with the addition of a caustic chemical, such as hydroxide, to the wastewater stream in order to increase pH to a point that the dissolved lead precipitates from the solution as solid metal hydroxide particles. Precipitated lead particles are then be removed from the liquid stream through a physical separation process, such as sedimentation or media filtration.
Despite advantages that include cost-effectiveness and the ability to handle high concentrations of lead, chemical precipitation does have its drawbacks. Facilities need to consider that chemical precipitation alone is not adequate for reducing lead content enough to satisfy stringent discharge limits, and must therefore be used in conjunction with other treatment technologies, typically as a means of pre-treatment. Hydroxide precipitation also produces sludge with high water content, so facilities need to be prepared to invest in sludge dewatering technologies and/or shoulder the costs associated with sludge disposal.
Adsorption
Along with chemical precipitation, adsorption is one of the most common technologies used in lead removal applications. Adsorption is a cost-effective means of treating streams with moderate concentrations of lead (usually between 1 ppb and 100 ppm). Among its benefits, adsorption offers no sludge generation, a range of affordable adsorbent materials, and good selectivity for heavy metals.
By definition, adsorption is a process that uses forces of molecular attraction to separate contaminants from water. Adsorbent media are carefully selected for their ability to pull a targeted dissolved material (or “solute”) out of solution, effectively holding the solute to the surface of the adsorbent media as a molecular or atomic film called an absorbate. Physical adsorption technologies are commonly used for lead separation, and the process consists of passing a liquid stream through some type of granular or porous adsorbent media. There are a range of different adsorbent media for lead-removal applications, including activated carbon most commonly, as well as zeolite, and biomass. In some cases, waste by-products from production of olive oil, tea, and other products have successfully been reclaimed for use as adsorbent media as well. Facilities typically choose adsorbent materials based on specific process needs, cost, local availability, and other factors.
While adsorption offers relatively low costs of operation, materials, and waste discharge, it is worth noting certain drawbacks that stem from limited adsorption capacity of most adsorbent materials. When used for streams with higher concentrations of lead or other heavy metals, the cost advantages of adsorption are diminished by the need for more frequent replacement of adsorbent media. As a result, adsorption is best used for streams with moderate to low concentrations of lead, or they are used in a larger wastewater treatment train following some type of pre-treatment.
Ion exchange
Ion exchange (IX) is effective for reducing lead content below stringent regulatory limits, as well as applications where selective removal of lead is desired. Additionally, IX is able to efficiently treat large volumes of water.
IX is a physical-chemical process where a liquid stream is passed through one or more columns that contain a resin substrate. The resin carries an ionic charge that is used to separate out certain targeted contaminants from solution. For lead removal applications, facilities use either a strong acid cation (SAC) or weak acid cation (WAC) resin. As a lead-contaminated stream is passed through the IX unit, the SAC or WAC resin selectively captures charged lead ions from solution, retaining them until the resin undergoes a regeneration cycle. There are also specialty resins that will focus on specific types of ions and removal to low levels, which are used when conventional resins cannot achieve the treatment objectives.
While IX can be a good solution for facilities that need to achieve very low levels of lead in their effluent or process water streams, there are some drawbacks. Most significantly, an IX system will require regular regeneration cycles to recharge the resin for future active cycles. Streams with high concentrations of lead will require more frequent regeneration cycles and result in a shorter lifespan for resin, which can have huge impacts on cost. Additionally, IX can be sensitive to pH, so a facility will need to plan to manage a variable stream pH and/or consider whether pH adjustment is needed ahead of an IX system. Finally, facilities will need to have a plan for treatment and safe disposal of wastes resulting from IX system use, which can include resins, regeneration chemicals, and rinse water—all of which may become contaminated by lead. Generally speaking, the higher the concentration of lead or other heavy metals in a stream, the less cost-effective IX becomes due to higher maintenance and waste discharge costs.
Membrane separation
Membrane separation refers to a group of physical separation technologies that use a permeable barrier to remove certain constituents from a liquid stream. In recent decades, membrane separation technologies have gained on traditional physical-chemical water treatment technologies due to advances in the development of system design and membrane materials. Depending upon the type chosen, membrane separation is capable of removing upwards of 90% of lead from water and wastewater streams, can be used for reclamation of stream constituents, and is effective for use in removing hardness, colors, odors, and TDS in addition to heavy metals such as lead.
The membrane separation process consists of passing a liquid stream through a porous membrane, usually by applying pressure to the stream. The pores in a membrane are specially sized to permit certain particles to pass through, while retaining others. In this way, membrane separation works based on a principle of size exclusion, and various types of membrane technologies are therefore classed according to pore size, with nanofiltration (NF) and reverse osmosis (RO)being the two types of membrane filtration with pores sized small enough to remove divalent cations, like lead. In some cases, facilities may use of multiple types of membrane separation in sequence, such as using ultrafiltration (UF) to pretreat a stream ahead of RO in order to maximize system efficiency and extend membrane life.
Membrane separation offers a high rate of removal for lead and other contaminants, potentially making it a good fit for facilities looking to treat wastewater or process water for reuse, or for those facilities who need to comply with stringent discharge limits on lead or other heavy metals. There are, however, some disadvantages to membrane separation that facilities should consider, which can include high costs for cleaning, maintenance, and replacement of membranes, as well as moderate to high energy consumption and flow rate limitations. Also keep in mind that membranes have a reject stream with a higher concentration of lead that will need to be treated.
Can SAMCO help?
SAMCO has over 40 years’ experience custom-designing and manufacturing wastewater treatment systems, so please feel free to reach out to us with your questions. For more information or to get in touch, contact us here. You can also visit our website to set up a call with an engineer or request a quote. We can walk you through the steps for developing the proper solution and realistic cost for a separation or wastewater treatment system to meet your lead removal needs.
For more articles on wastewater treatment, head on over to our blog. Some that might be of interest to you include:
- How Do You Know If An Industrial Facility Needs a Wastewater Treatment System?
- How to Choose the Best Wastewater Treatment System for Your Plant
- Seven Ways Your Facility Isn’t Meeting Effluent Regulations and How to Solve Them
- The Importance of Wastewater Treatment for Your Facility: Is it Necessary?
- 9 of the Best Industrial Wastewater Treatment Equipment Supply and Technology Companies
- What Is a Wastewater Treatability Study and How Does it Work?
- How Much Does a Water/Wastewater Treatability Study Cost for Your Plant?
- What Are the New Steam Electric Power Generating Effluent Guidelines and What Do They Mean for Your Plant?
- How Much Does a Wastewater Treatment System Cost? (Pricing, Factors, Etc.)