How Do You Choose the Best Reverse Osmosis and Nanofiltration Membrane System for an Industrial Facility?
As global demands for clean water increase, more and more industrial facilities are looking toward membrane filtration solutions, such as reverse osmosis (RO) and nanofiltration (NF), to help manage intake, process, and waste water treatment. Using membrane filtration can help your facility reuse wastewater and virtually eliminate discharge fees, and depending on the industry or required use, it can also help a facility efficiently treat raw and/or process water more efficiently than some conventional treatments.
If you think an industrial plant needs to explore its options regarding RO/NF, you might be wondering “How Do You Choose the Best RO/NF System for an Industrial Facility?”
Since there are a variety of options that will depend on what industry the plant serves (oil and gas, petrochemical, food and beverage, etc.), along with which part of the process the filtration is needed and what contaminants need to be removed, this blog article breaks down what to consider when going through the process:
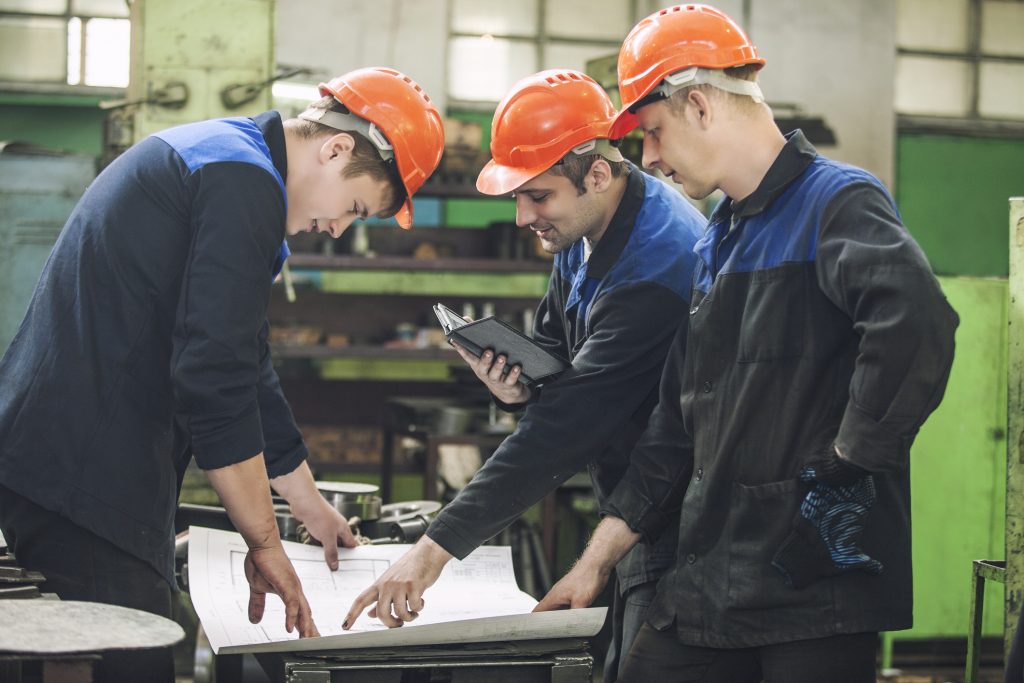
What is the stream characterization?
When a facility is looking to consider RO/NF membrane filtration as a water treatment solution, they first need to consider what the quality characterizations of the liquid stream are in addition to the purity requirements of the treated stream. For example, if a microelectronics facility is looking to use a raw water source, such as a river or lake, to feed their process stream (which requires extremely high-purity water), chances are you are looking at substantial pretreatment process preceding an RO system, followed by ion exchange, which can effectively remove nearly all suspended and colloidal contaminants. Since RO is the finest of all membrane filtration systems (with extremely small pores capable of removing particles as small as 0.1 nm), it is generally a great fit for microelectronics production, among other processes, such as desalination.
NF delivers slightly coarser filtration than RO, with the ability to remove particles as small as 0.002 to 0.005 μm in diameter, so it might be a better choice for softening hard water. NF is a relatively recent technology that was developed mainly for potable water generation, but it removes harmful contaminants, such as pesticide compounds and organic macromolecules, while retaining minerals that RO would otherwise remove. Nanofiltration membranes are capable of removing larger divalent ions such as calcium sulfate, while allowing smaller monovalent ions such as sodium chloride to pass through, which makes it a good choice for concentration and demineralization in some dairy-processing facilities.
What type of membrane should you use?
Membrane configurations can vary, but mostly spiral wound and hollow fiber membranes are used. The quality and overall efficiency of the unit can depend on the type of membrane chosen, which can include:
- Hollow fiber;more suitable for low-solid liquid streams, these membranes are constructed of thousands of hollow fibers that resemble spaghetti and can be efficiently kept clean with occasional backwashing and clean-in-place (CIP) technology.
- Plate and frame; these membranes are placed on top of plate-like structures that collect solids on the inside of the supporting plate. These have low packing densities and can be less efficient than other filtration methods, but they are generally easy to use and clean. Typically used on solutions difficult to filter. They are also among the lower-cost membranes but higher-cost systems.
- Spiral-wound; spiral-wound membranes are among the commonly used. They are composed of flat sheets of membrane between mesh-like spacers that are wound around a central tube (this tube collects the permeate after filtration) and placed within a casing. They are relatively compact and can be used in high-volume applications with low suspended solids.
- Tubular; several tube-like membranes are placed within a pipe/shell, and as the stream is passed through the tubes, it transfers the permeate to the pipe/shell side. These can be less permeable with a lower packing density and are generally used for hard-to-treat streams, such as those with high TDS, TSS, and oils, greases, and fats.
Are there pre- or post-treatment needs for your RO/NF membrane treatment system?
RO and NF membrane systems are rarely used alone; they are generally part of a technology “train.” Since they can foul or scale pretty easily, they usually require some type of pretreatment, such as microfiltration, again, depending on the quality of the incoming stream versus the needed stream quality after filtration.
There is also usually some type of byproduct that needs to be recovered or disposed of after the filtration. When designing your RO/NF system, this should be taken into consideration, as well. For example, sometimes the byproduct might be something valuable (such as silver), or in other cases, it could be something expensive to dispose of. Byproducts are always important to keep in mind when developing a plan for filtration.
What is the result of a treatability study and/or pilot test?
A treatability study is a study or test that will determine if the water stream can be treated for your process and how it needs to be treated. If the study is done correctly, it will clearly identify the contaminants present in your water stream, helping ensure the proper treatment solutions are considered and implemented in your RO/NF membrane treatment system. It can help your facility understand what pre- and post-treatment might be needed, as well as the bypass ratio, amount of recovery the system will yield, and how efficient you can expect the process to be.
This step is critically important when choosing the best treatment system for your plant. After having a roadmap of maybe two or three technology platforms that meet your base and operating cost, running an efficient treatability test will help validate the assumptions you’ve made about possible contaminations and solutions to remove them. This streamlines to process and takes out any guesswork, ensuring your facility is getting the best possible solution for your unique situation.
Also keep in mind that even though the study might seem thorough on paper, there’s nothing better than running pilot testing in the field to validate the treatment/technology assumptions, optimize design, because during this phase, other problems can arise and be found prior to choosing the components of your system, which can help save you from any process water hiccups or effluent violations down the line.
How can SAMCO help?
SAMCO has over 40 years’ experience custom-designing and manufacturing RO/NF systems for a range of industries and solutions, so please feel free to reach out to us with your questions.
For more information or to get in touch, contact us here to set up a consultation with an engineer or request a quote. We can walk you through the steps for developing the proper solution and realistic cost for your RO/NF treatment system needs.
Head on over to our blog to learn more about industrial filtration and process separation technology. Some articles that might be of specific interest to you include:
- Does Your Facility Need a Reverse Osmosis or Nanofiltration System?
- Reverse Osmosis and Nanofiltration Membrane Filtration Systems: Common Problems and How to Fix Them
- What Are the Best Companies for Reverse Osmosis and Nanofiltration Membrane Systems?
- Reverse Osmosis vs Nanofiltration Membrane Process: What Is the Difference?
- What Are Reverse Osmosis and Nanofiltration and How Do They Work?